双金属复合管是由两种金属管道组合而成的一种新型管道,其外管是普通的碳钢管,承受管道系统的工作压力;内管是耐蚀合金管,具有优异的耐蚀性能。双金属复合管改变了传统金属材料的单一性和局限性,通过碳钢基体保证管道的整体强度和机械指标,使管道的使用寿命大大提高,使用成本降低,因而双金属复合管具有广泛的应用前景。
双金属复合管的工艺流程
双金属复合管分为机械复合和冶金复合,其中以机械复合居多,即将碳钢基管和不锈钢管穿在一起采用水压、爆炸及旋压等方法生产,工艺流程如图1所示。
图1 工艺流程
双金属复合管常见问题及原因分析
目前酸性气田存在大量的H2S或CO2,由于服役环境恶劣,输送管材必须具有较好的抗H2S,CO2,Cl-腐蚀性,管道输送介质为气液混合介质,H2S或CO2溶于水形成弱酸,会造成碳钢管道的严重腐蚀。其中H2S腐蚀为电化学腐蚀、氢致开裂和硫化物应力腐蚀开裂,典型特征是局部腐蚀;CO2腐蚀主要是电偶腐蚀和电化学腐蚀,典型特征是局部腐蚀和均匀腐蚀。此外,Cl-促进局部腐蚀,使腐蚀向管材基体纵深发展而形成氯化物点蚀,最终导致管道穿孔。
检查双金属复合管时发现其部分内壁存在较大范围的锈迹,也有一部分双金属复合管内壁存在水锈,现场管线腐蚀情况如图2所示。
图2 现场管线腐蚀情况
1 双金属复合管发生电偶腐蚀的基理
(1) 管帽密封不严,存在破损,双金属复合管进厂管端没有用胶带密封,运输过程中进入铁屑等污染物,并且堆场多雨空气湿度大。
(2) 喷砂除锈管端密封不严,吹扫设备未能将进入双金属复合管内壁钢砂吹扫干净;手工除锈时,铁屑通过破损管帽进入管中。
双金属复合管316L衬管表面发生铁污染,铁损伤导致钝化膜破损,引起破损点和钝化膜保护区的大阴极小阳极的电偶腐蚀。
316L不锈钢耐蚀的原因是表面形成致密、稳定牢固的氧化膜,如图3所示。
图3 不锈钢表面形成钝化膜Cr2O3示意
双金属复合管发生电偶腐蚀原理:腐蚀电位较低的金属和电位较高的金属接触而形成腐蚀原电池,其结果是电位较高的金属发生阴极反应,导致其腐蚀过程受到抑制;电位较低的金属发生阳极反应,导致其腐蚀过程加速,如图4所示。
图4 电偶腐蚀示意
2 双金属复合管形成电偶腐蚀的原因
(1) 材料表面条件不同(划伤、摩擦、焊接),如图5所示。
图5 双金属复合管形成电偶腐蚀
(2) 一般情况下,随着阴阳极面积比值的增加,作为阳极的金属腐蚀速率也增加。
(3) 海水等电导率高的介质,电偶电流可分散到离接触点较远的阳极表面,阳极所受腐蚀较为均匀。但如果在软水或普通大气等电导率较低的介质中,腐蚀会集中在离接触点较近的阳极表面,相当于阳极的有效面积减少,增加了阳极局部表面的溶解速率。
3 措施及建议
(1) 避免异种金属合金的相互接触。
(2) 切忌形成大阴极-小阳极的不利于防腐蚀的面积比。
(3) 不同腐蚀电位的金属接触面采取绝缘措施。
(4) 如发现铁污染等使316L表面钝化膜损坏的情况,可对锈蚀位置抛光,去除浮锈,抛光后需符合最小壁厚要求,用不锈钢酸洗钝化膏均匀覆盖在抛光位置,与未抛光位置至少搭接50 mm,用自来水(水中Cl-质量浓度不能超过30 mg/L)对钝化位置冲洗或用清洁湿抹布擦除钝化膏,使其形成钝化膜。对316L不锈钢酸洗钝化后,用内窥镜质量检验合格,如图6所示。
图6 内窥镜复验双金属复合管内壁情况
结 语
高酸性油气田腐蚀环境恶劣,碳钢难以满足要求,加入缓蚀剂能起到一定的效果,但稳定性不够,耐蚀合金价格昂贵。双金属复合管具有良好的综合性能,对强腐蚀环境的油气田,其性价比优势明显。为保证双金属复合管的服役周期,防止铁污染和抑制电偶腐蚀尤为重要,可以在双金属复合管的管口处放置吸潮包,同时采用密封性好的管帽密封后,用无痕胶带缠好。保证双金属复合管的质量,以便应对强腐蚀环境的油气田,延长双金属复合管道的使用寿命。
免责声明:本网站所转载的文字、图片与视频资料版权归原创作者所有,如果涉及侵权,请第一时间联系本网删除。
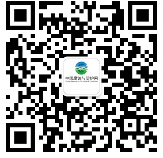
官方微信
《腐蚀与防护网电子期刊》征订启事
- 投稿联系:编辑部
- 电话:010-62316606
- 邮箱:fsfhzy666@163.com
- 腐蚀与防护网官方QQ群:140808414