[摘 要] 为解决车轮用钢服役过程中的大气腐蚀问题,通过中性盐雾试验研究了590 MPa 和780 MPa 级别2 种汽车车轮用钢590CL 和780CL 在5%NaCl 溶液中性盐雾环境下的初期腐蚀行为,并采用辉光光谱仪、金相显微镜、扫描电子显微镜(SEM)、X 射线衍射仪(XRD)和电化学测量等手段表征了盐雾试验后腐蚀产物的形貌、结构、腐蚀速率及电化学行为。结果表明,在中性盐雾试验48 h 后,2 种车轮用钢表面均出现红锈,二者腐蚀速率为590CL>780CL。在3.5%NaCl 溶液中测量的极化曲线和电化学阻抗谱结果与上述结果有较好的一致性。590CL 和780CL 这2 种钢材的腐蚀产物主要为γ-FeO(OH),还含有部分α-FeO(OH)和Fe3O4,腐蚀产物对基体基本没有保护作用。
[关键词] 车轮钢;中性盐雾试验;腐蚀产物;微观结构;电化学测试
0 前 言
车轮作为汽车的重要运动组成部件之一,在高速行驶过程中,承受循环交变载荷作用,其最主要的损伤形式是磨损和疲劳[1-4]。除了磨损和疲劳损伤,长期苛刻的服役环境也是影响车轮寿命的重要原因之一。由于常年行驶在户外环境中,四季的交替、地域的变化以及自然条件的变化都将对车轮形成严峻的考验,酸雨、除冰雪、风沙、沿海盐雾、工业大气等众多复杂的环境因素都会对车轮造成腐蚀作用[5]。钢板是汽车生产的主要原料之一,在各行各业及日常生活中应用也颇为广泛。钢铁腐蚀对人类的正常生活和所处的环境以及国家的基本资源都产生了巨大危害,钢铁腐蚀问题不容忽视[6],车轮的腐蚀会造成安全隐患,影响汽车的使用寿命和运行安全。国内汽车行业对材料防腐性能要求越来越高,各主机厂已将腐蚀控制要求作为衡量产品质量的重要指标[7]。因此进行腐蚀试验评价车轮钢的耐蚀性能变得越来越重要。
由于专用车,例如农机用车、垃圾清运车和洒水车等的使用环境特殊,车轮在服役过程中也会遭受更多恶劣环境的影响,对车轮用钢的耐腐蚀性能也提出了更高的要求。为了提高车轮钢的耐腐蚀性能,新型车轮钢中添加了Cr 元素。目前对热轧车轮用钢基板腐蚀的研究较少,为了延长汽车在恶劣环境中的服役寿命,降低能源消耗,针对车轮用钢基板开展相关的腐蚀研究具有重要意义。吴菲等[8]利用周期浸泡及电化学试验研究了C 和Si 含量对车轮钢腐蚀速率的影响,发现Si 含量增加使得车轮钢自腐蚀电位升高,表面电荷转移电阻增大,从而耐腐蚀性能得到提高,但对C 和Si 元素影响车轮钢耐腐蚀性能的原因未进行分析。曾伟等[9]通过盐雾试验对车轮钢轮辋材料进行预腐蚀,随腐蚀时间的延长,平均腐蚀速率呈先减小后增加再减小的趋势,但未对腐蚀产物和形貌进行细致的研究分析。杨文斌等[10]在车轮钢表面制备出Fe 基和Co 基合金局部修复涂层,在酸雨溶液中Co 涂层表现出优异的耐腐蚀性能。
本工作针对590 MPa 和780 MPa 2 种不同强度级别的汽车车轮用钢,对比研究了中性盐雾环境下二者初期的腐蚀速率、腐蚀产物微观形貌和组成及电化学腐蚀行为。
1 试 验
1.1 试 材
试验材料为某钢厂生产的车轮用钢590CL 和780CL,主要化学成分(质量分数)如表1。
表1 2 种钢材主要化学成分(质量分数) %
中性盐雾试验试样尺寸为150 mm×70 mm×4 mm,经过酸洗和乙醇超声清洗后,吹干,用胶带封装四边后备用。电化学试样尺寸为10 mm×10 mm×4 mm,经过酸洗处理后,除去表面氧化皮,乙醇擦拭表面晾干后备用。
1.2 盐雾加速试验
中性盐雾试验按照GB/T 10125-2021“人造气氛腐蚀试验 盐雾试验”,采用Q-FOG CCT-1100 循环腐蚀试验箱,使用5%NaCl 溶液盐雾气氛,测试48 h,将试样置于室内自然干燥0.5 h,然后用流水冲洗表面残存溶液,再用乙醇清洗,然后凉风吹干观察试样表面变化情况。
1.3 测试表征
采用失重法计算试样的腐蚀速率,根据ISO 8407“金属和合金的腐蚀·腐蚀试验试样中腐蚀产物的去除”中规定,腐蚀试验前用分析天平测试试样质量,盐雾腐蚀后的试样用含3.5 g/L C6 H12 N4 缓蚀剂的50%(体积分数)盐酸溶液浸泡,在常温下用水和酒精分别清洗,然后凉风吹干后进行称重。不同周期的质量损失数据计算5 个平行试样的均值。
采用GDS 850A 型辉光光谱仪(GDS)对酸洗后的590CL 和780CL 钢板元素随深度分布情况进行表征,采用电压700 V,电流20 mA。
采用OLYMPS 激光共焦显微镜观察试验用钢的金相组织。
采用S-3400N 扫描电镜(SEM)观察试样表面腐蚀形貌,并用能谱仪(EDS)分析腐蚀产物的化学成分。
使用D8 Advance 型X 射线衍射仪(XRD)分析腐蚀产物的物相,采用Co 靶Kα 辐射,电压35 kV,电流40 mA。
电化学测试使用的是PARSTAT 2273 电化学工作站,测试溶液为3.5%NaCl 溶液,使用三电极体系进行试验:参比电极为饱和氯化银电极(Ag/AgCl),辅助电极为铂电极,车轮用钢590CL 和780CL 分别为工作电极。极化曲线试验前把试样浸泡10 min,扫描电位为-0.25~0.25 V(vs OCP),扫描速率为1 mV/s。电化学阻抗的测量振幅为10 mV,频率范围1.0×(10-2 ~105) Hz,测量后用ZSimp-win 软件对其数据进行拟合。
2 结果与讨论
2.1 表面成分与形貌
图1 为2 种不同强度级别的车轮用钢590CL 和780CL 酸洗板浅表层Si、Mn 和Cr 元素深度分布状态(GDS)。其中,Si 在腐蚀表面的富集有利于形成更小粒度的α-FeO(OH);Cr 与O 形成Cr2O3钝化膜,阻止腐蚀基体,提高材料的耐蚀性能。根据GDS 结果可知,Si、Mn 和Cr 3 种元素在590CL 酸洗板表面的含量均比780CL 表面低,Si 和Mn 的含量差别较小,而780CL 的Cr 元素含量较590CL 高0.4%左右。
图1 2 种典型车轮用钢590CL 和780 CL GDS 曲线
图2 为2 种典型车轮用钢590CL 和780CL 基体组织。可见,590CL 的基体组织主要为铁素体和珠光体,780CL 的基体组织主要为铁素体和贝氏体。
图2 2 种典型车轮用钢590CL 和780 CL 基体组织
图3 为2 种典型车轮用钢590CL 和780CL 表面酸洗后的微观形貌。可见,590CL 样品表面更为粗糙,存在大量凹坑;780CL 样品表面质量较好。
图3 2 种典型车轮用钢590CL 和780 CL 表面酸洗后的微观形貌
EDS 能谱结果(表2)显示,590CL 样品表面主要元素分布为Mn、Fe,780CL 样品表面主要元素分布为Mn、Fe、Cr。
表2 2 种典型车轮用钢590CL 和780CL 的EDS 检测结果(质量分数) %
2.2 腐蚀产物宏观形貌
图4 为2 种不同强度级别的车轮用钢590CL 和780CL 在5%NaCl 盐雾气氛下腐蚀不同时间后试样表面腐蚀产物的宏观形貌。从图中可以看出,未经盐雾腐蚀的试样中590CL 的表面相比780CL 略粗糙,780CL 试样表面更为致密,与图3 中表面酸洗后试样表面微观形貌一致。腐蚀试验进行2 h,590CL 和780CL 酸洗板表面均出现了褐棕色的腐蚀产物,随着腐蚀时间延长至6 h,590CL 和780CL 表面红棕色腐蚀产物增多且颜色加深,覆盖率95%以上;腐蚀时间进一步延长至24 h 后,钢板表面锈层明显增厚,呈现亮红褐色;盐雾腐蚀48 h 后,590CL 和780CL 表面锈层呈黄褐色,其中纹路区域腐蚀产物呈棕褐色,其纹路边缘为黑色,锈层面积可达100%。
图4 2 种典型车轮用钢在中性盐雾腐蚀不同时间后的表面宏观形貌
2.3 腐蚀速率
图5 为2 种不同强度级别的车轮用钢590CL 和780CL 的质量损失随试验时间变化的曲线。根据盐雾腐蚀后试样的宏观形貌图可知,难以通过锈蚀出现时间的早晚及红锈面积来判断2 种试样的耐蚀性,而根据腐蚀质量损失[11]来衡量二者耐蚀性相对更为准确。根据图5 可知,质量损失速率为590CL>780CL,随着腐蚀时间的延长,二者的腐蚀速率略有下降,总的来说,780CL 的耐腐蚀性相对较好。这符合GDS 元素深度分布规律,Cr 是主要铁素体形成元素,与氧结合能生成耐腐蚀的Cr2O3钝化膜,是保持耐蚀性的基本元素之一。
图5 中性盐雾试验中2 种典型车轮钢的质量损失曲线和质量损失速率曲线
2.4 腐蚀产物微观形貌及物相
图6 为试样经中性盐雾试验48 h 后的表面微观形貌。如图所示,腐蚀产物多数以球状存在,且堆积行为比较明显。经放大后观察到腐蚀产物呈针尖发散的球团状,纹路区域棕褐色腐蚀产物主要以块状存在。腐蚀产物能谱(EDS)分析结果见表3,根据EDS 检测结果可知,590CL 和780CL 试样表面腐蚀产物的存在形式主要为Fe 的氧化物。
图6 中性盐雾试验48 h 后2 种典型车轮用钢表面腐蚀产物的微观形貌
表3 中性盐雾试验48 h 后2 种典型车轮用钢表面腐蚀产物的EDS 检测结果(质量分数) %
图7 为试样经中性盐雾试验48 h 后的截面微观形貌。590CL 截面锈层疏松且存在较多裂纹,厚度在8.14~18.20 μm 之间,对基体的保护作用较差;780CL截面锈层内层与基体结合较为致密,保护作用较好,外层较为疏松,厚度在5.75~6.35 μm 之间。截面EDS 能谱结果如表4。
图7 中性盐雾试验48 h 后2 种典型车轮用钢截面腐蚀产物的微观形貌
表4 中性盐雾试验48 h 后2 种典型车轮用钢截面腐蚀产物的EDS 检测结果(质量分数) %
图8 为中性盐雾试验48 h 后腐蚀产物的XRD 谱,并对其物相含量进行半经验定量拟合计算,结果见表5。结果表明,车轮用钢590CL 和780CL 表面腐蚀产物大多为γ-FeO(OH),还含有少部分α-FeO(OH)和Fe3O4。XRD 结果表明腐蚀产物主要为Fe 的氧化物,与EDS 能谱分析结果一致。保护性锈层α-FeO(OH)的含量较低,锈层对钢板表面的保护作用较小,这与腐蚀速率试验结果保持良好一致。
图8 中性盐雾试验48 h 后2 种典型车轮用钢表面腐蚀产物的XRD 谱
表5 中性盐雾试验48 h 后2 种典型车轮用钢表面腐蚀产物的物相含量(质量分数) %
2.5 电化学性能
自腐蚀电流密度的大小也可用于表征腐蚀速率,自腐蚀电流密度越大,则材料腐蚀速率越大,越容易发生腐蚀[12]。
图9 为3.5%NaCl 溶液中浸泡10 min 后测得车轮用钢590CL 和780CL 的电化学阻抗谱和极化曲线。
图9 2 种典型车轮钢在3.5%NaCl 溶液中的极化曲线和电化学阻抗谱
对极化曲线(图9a)进行拟合,结果如表6 所示。结果表明,腐蚀电流密度590CL >780CL,阻抗模值780CL>590CL,590CL 和780CL 的电化学阻抗图只有1个容抗弧,综合考虑,认为样品本身相当于1 个电阻与1 个电容并联,即可采用图10[13]所示电路模型对EIS进行拟合(其中,Rs 为溶液电阻;Qc 为腐蚀产物电容;Rc 为腐蚀产物电阻)。结合图9 和图10 可知,780CL样品表面的低频阻抗模值高达1 235 Ω·cm2 以上,590CL 的电阻可达780 Ω·cm2 以上。阻抗值越大,自腐蚀电位越小,材料的耐腐蚀性能越好,因此780CL 的耐腐蚀性优于590CL。极化曲线和电化学阻抗图结果规律性保持一致。除此之外,电化学的结果与质量损失的结果规律也相同。
图10 图8 中EIS 的等效电路模型[13]
表6 极化曲线的拟合结果
3 结论
(1)在中性盐雾试验48 h 后,2 种车轮用钢表面均出现红锈,红锈面积可达100%,其质量损失和腐蚀速率为590CL>780CL。780CL 的耐腐蚀性相对较好,认为主要由于780CL 中Cr 含量较高。
(2)590CL 和780CL 的腐蚀产物主要为Fe 的氧化物,两者腐蚀产物呈针尖发散的球团状,主要存在形式为γ-FeO(OH),还含有部分α-FeO(OH)和Fe3O4,其中对试样基体具有保护性作用的α-FeO(OH)含量较低,说明产生的红锈对基体基本没有保护作用。
(3)电化学试验结果表明,780CL 的耐腐蚀性能优于590CL,电化学结果与中性盐雾试验及腐蚀速率结果保持一致。
[参 考 文 献 ]
[1] Hernández F C R, DEMAS N G, DAVIS D D, et al.Mechanical properties and wear performance of premium rail steels[J].Wear, 2007, 263(1-6): 766-772.
[2] 郑文龙.钢的腐蚀磨损失效及其分析方法[C]/ /石油和化工设备管道防腐技术与对策专题研讨会文集.厦门:中国石油石化工程研究会,2010:21-43.ZHENG W L.Corrosion and wear failure of steel and its analysis method[C]/ /Proceedings of the National Petroleum and Chemical Industry Corrosion and Protection Technology Exchange Conference.Xiamen: China Petroleum and Petrochemical Engineering Research Association,2010:21-43.
[3] EKBERG A, ?kesson B, KABO E.Wheel/rail rolling contact fatigue-Probe, predict, prevent[J].Wear,2014,314:2-12.
[4] ZENG D, LU L, ZHANG J, et al.Effect of micro-inclussions on subsurface-initiated rolling contactfatigue of a railway wheel[J].Journal of Rail and Rapid Transit, 2016,230(2): 544-553.
[5] 郭明晓, 潘 晨, 王振尧,等.碳钢在模拟海洋工业大气环境中初期腐蚀行为研究[J].金属学报, 2018, 54(1):65-75.GUO M X, PAN C, WANG Z Y, et al.A study on the initial corrosion behavior of carbon steel exposed to a simulated coastal-industrial atmosphere[J].Acta Metallurgica Sinica,2018, 54(1): 65-75.
[6] 张 琳, 王振尧, 赵春英,等.碳钢和耐候钢在盐雾环境下的腐蚀行为研究[J].装备环境工程, 2014, 11(1):1-6.ZHANG L, WANG Z Y, ZHAO C Y, et al.Study on corrosion behavior of carbon steel and weathering steel in salt spray test [J].Equipment Environmental Engineering,2014, 11(1): 1-6.
[7] 金泉军,梁 韬,吕玲芳,等.不同腐蚀试验方法对镀锌材料的防腐性能评价研究[J].材料保护,2023,56(2):51-56.JIN Q J, LIANG T, LV L F, et al.Evaluation of the anticorrosion performance of galvanized materials using different corrosion test methods [J].Materials Protection, 2023,56(2): 51-56.
[8] 吴 菲,肖 峰,江 波,等.C 和Si 含量对车轮钢腐蚀行为的影响[J].腐蚀与防护,2017,38(2):124.WU F, XIAO F, JIANG B, et al.Effects of C and Si content on corrosion behavior of wheel steel[J].Corrosion &Protection, 2017,38(2):124.
[9] 曾 伟,王少杰,韩 靖,等.预腐蚀对ER8 车轮钢磨损行为的影响[J].材料导报, 2019, 33(24): 4 152-4 156.ZENG W, WANG S J, HAN J, et al.Effect of pre-corrosion on wear behavior of ER8 wheel steel[J].Materials Reports, 2019, 33(24): 4 152-4 156.
[10] 杨文斌,夏金龙,肖 乾,等.ER8 车轮钢激光熔覆涂层在酸雨环境下的磨损与腐蚀性能分析研究[J].表面技术,2023, 52(1): 314-324.YANG W B,XIA J L,XIAO Q,et al.Performance analysis of laser cladding coating on ER8 wheel steel in acid rain environment [J].Surface Technology, 2023, 52 ( 1):314-324.
[11] 黎 敏,郝玉林,姚士聪,等.中性盐雾环境中典型汽车用钢的初期腐蚀行为[J].电镀与涂饰, 2019, 38(18):1 015-1 021.LI M, HAO Y L, YAO S C, et al.Early corrosion behavior of typical automotive steel sheets in neutral salt spray test[J].Electropating & Finishing, 2019, 38 ( 18):1 015-1 021.
[12] 黄 雄,朱春东,于凤群.DP590 双相高强钢焊缝在模拟酸雨溶液中的腐蚀行为[J].热加工工艺,2017,46(17):187-190.HUANG X, ZHU C D, YU F Q.Corrosion behavior of DP590 dual-phase high-strength steel welding seam in simulated acid rain solution[J].Hot Working Technology,2017,46(17):187-190.
[13] 韩军科,严 红,黄 耀,等.耐候钢表面氧化皮的结构特征及其对大气腐蚀行为的影响[J].金属学报,2017,53(2):163-174.HAN J K, YAN H, HUANG Y, et al.Structural features of oxide scales on weathering steel and their influence on atmospheric corrosion[J].Acta Metallurgica Sinica, 2017,53(2):163-174.
免责声明:本网站所转载的文字、图片与视频资料版权归原创作者所有,如果涉及侵权,请第一时间联系本网删除。
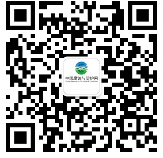
官方微信
《腐蚀与防护网电子期刊》征订启事
- 投稿联系:编辑部
- 电话:010-62316606
- 邮箱:fsfhzy666@163.com
- 腐蚀与防护网官方QQ群:140808414