摘要
采用电弧喷涂技术在EH36钢表面制备了5083铝合金涂层和Zn15Al涂层,结合扫描电子显微镜 (SEM)、X射线衍射仪 (XRD)、电化学测试和腐蚀失重等方法对比研究了两种涂层在中性盐雾环境下的耐蚀性能。结果表明,随着腐蚀的进行,两种涂层的腐蚀速率均逐渐下降,且5083Al合金涂层的腐蚀速率明显低于Zn15Al涂层。形貌观察结果表明,5083铝合金涂层的腐蚀产物呈致密块状,Cl-无明显渗入;而Zn15Al涂层的腐蚀产物呈疏松的细针状,盐雾腐蚀10 d后有Cl-沉积在腐蚀产物层中并逐渐渗入至涂层基体。5083铝合金涂层的腐蚀产物主要为Al(OH)3,Zn15Al涂层腐蚀产物主要由Zn(OH)2和Zn5(OH)8Cl2·H2O组成。结合溶度积常数Ksp和过饱和度的理论计算,Al(OH)3沉积所需Al3+浓度更低、沉积速度更快,因此5083铝合金涂层更倾向于形成致密的腐蚀产物层。这一结果与电化学阻抗谱 (EIS) 测试结果相吻合,随腐蚀时间延长,两种涂层的极化电阻逐渐增大,且5083铝合金涂层的极化电阻高于Zn15Al涂层,说明腐蚀产物致密性是影响两种涂层耐蚀性能的主要原因。
关键词: 电弧喷涂 ; 5083Al涂层 ; Zn15Al涂层 ; 盐雾腐蚀性能
本文引用格式
肖文涛, 刘静, 彭晶晶, 张弦, 吴开明. 两种电弧喷涂涂层在中性盐雾环境下的耐蚀性能对比研究. 中国腐蚀与防护学报[J], 2023, 43(5): 1003-1014 DOI:10.11902/1005.4537.2022.284
XIAO Wentao, LIU Jing, PENG Jingjing, ZHANG Xian, WU Kaiming. Corrosion Resistance of Two Arc Spraying Coatings on EH36 Steel in Neutral Salt Spray Environment. Journal of Chinese Society for Corrosion and Protection[J], 2023, 43(5): 1003-1014 DOI:10.11902/1005.4537.2022.284
腐蚀是现代海洋工业普遍关注的主要问题之一,它影响着海洋材料的使用可靠性,造成了巨大的经济损失。研究表明,金属材料构件的腐蚀通常都发生在表面或从表面开始,因此对金属构件采取表面改性措施如热喷涂等,不但能够提高金属构件的服役寿命,还能减少金属材料的消耗[1,2]。目前热喷涂按喷涂方法主要分为线材火焰喷涂、粉末火焰喷涂、爆炸喷涂、超音速火焰喷涂、等离子喷涂和电弧喷涂等。其中,电弧喷涂金属涂层,如Al、Zn、铝锌合金涂层,由于低成本、高效益和显著的防腐性能,被广泛用于海洋防腐环境中。涂层既可以作为阻挡侵蚀的屏障,也可以为基材提供阴极保护[3~7]。
电弧喷涂是将金属或合金丝制成熔化电极,由电动机驱动,在喷枪口相交产生短路而引发电弧、熔化,借助压缩空气雾化成颗粒并高速喷向经过预处理的工件表面,形成涂层[8~11]。与其他涂层工艺相比,金属与钢基材的粘合具有高亲和力,但由于熔化的金属液滴在基底上扩散速度较快,并且撞击到基体表面过程中可能发生飞散现象,其冷却后不均匀沉积在基底上,在热应力的作用下使得涂层中仍存在气孔和裂纹等缺陷[12~15]。
Zn是热喷涂防腐技术领域中应用最早且最多的涂层材料。Zn涂层对钢铁基体的腐蚀防护作用主要体现在以下几个方面:物理屏蔽、牺牲阳极作用和腐蚀产物堵塞[16]。英国钢铁研究协会BISRA在1940年对采用热喷涂、电镀及热浸等工艺制备的Zn涂层进行了长达12年的暴露测试[17],包含了农村,沿海和工业区以及海洋浸没等多种测试环境,测试发现Zn涂层随着时间的延长其腐蚀速率变化不大。Al涂层与Zn涂层相比最显著的区别是Al涂层的腐蚀产物难溶于水,因此Al涂层对钢铁基体的防护寿命比Zn涂层长得多。美国在1964年对热喷涂锌铝涂层耐腐蚀性能研究进行了暴露实验[18],结果表明在酸性环境中,纯Al涂层相比于纯Zn涂层而言具有更优越的腐蚀防护性能。锌铝涂层同时具有纯Zn和纯Al涂层的性能优点,又能弥补二者各自的缺点。日本在1986年对热喷涂的Zn、Al、Zn15Al涂层进行海洋腐蚀测试[19],结果表明7 a后Zn涂层在海洋浸没部分出现降解,而Al和Zn-Al涂层依旧表现出极好的耐腐蚀性能,18 a后大多数厚度为175 μm的Al和Zn-Al涂层仍保持其出色的腐蚀防护性能,涂层富Zn相的选择性腐蚀以及氢氧化铝的生成是其具有良好耐腐蚀性的主要原因,且Al含量占15%~22%时,涂层耐蚀性能最好[20]。
此外,牺牲阳极金属如Mg的加入可能会对电弧喷涂涂层具有更好的耐蚀性能,然而,似乎少有利用这些金属[21~23]来定量评价电弧喷涂涂层的电化学性能。5083铝合金作为高镁合金的代表,其优良的耐蚀性能使其广泛应用于船舶、交通运输和海洋平台等环境中。
因此,本文首先在船用EH36钢板上电弧喷涂5083铝合金涂层和Zn15Al涂层,然后对比研究两种涂层在模拟海洋大气下的耐蚀性能,分析其腐蚀机理,为海洋环境下钢结构的涂层防护提供理论指导。
1 实验方法
基材选用EH36钢板,喷涂材料选用5083铝合金丝和Zn15Al合金丝,直径均为Φ2 mm,其具体成分如表1所示。喷涂前先对试样进行喷砂处理,然后采用KZ-600型电弧喷涂机进行电弧喷涂,涂层厚度约为200 μm,不做封孔处理。5083铝合金的喷涂电压为34 V,工作电流为140~160 A,空气压力0.6 MPa,喷涂距离150 mm;Zn15Al的喷涂电压为34 V,工作电流为100~120 A,空气压力0.6 MPa,喷涂距离150 mm。喷涂完毕后将样品线切割成尺寸为50 mm×50 mm×5 mm的试样,并用酒精除油、去离子水清洗、吹干后放入干燥皿中备用。
表1 丝材化学成分 (mass fraction / %)
利用THV-1MD型维氏硬度仪对涂层的表面硬度进行测量,测试过程按照GB/T 9790-2021的方法进行[24],将相对两面顶角为136°的正四棱锥体压头以0.3 kgf压入被测表面,试验力保持30 s后卸除,通过微调目镜直至看清试样表面的压痕,然后测量压痕对角线的长度,把对角线的长度带入下式即可得到显微硬度值,取10个点的平均值。
(1)
式中,HV为维氏硬度 (kgf/mm2),F为施加到试样上的力 (kgf),d为压痕长度 (mm)。
按照GB/T8642-2002[25]中的方法,采用ETM105D型电子万能试验机对涂层的结合强度进行测试。圆柱状试样直径为25 mm,将试样没有涂层的一面进行喷砂处理,用E7胶将涂层面和非涂层面粘在直径相等的不锈钢圆柱上,100 ℃下固化3 h后进行拉伸测试,拉伸速率为1.8 mm/min。每种样品分别测试3组有效数据取平均值。
采用BX-51M型金相显微镜观察涂层的表面形貌,并利用Photoshop软件的灰度法 (孔隙颜色识别) 对涂层孔隙率进行测量:首先将截面扫描电镜 (SEM) 图片导入Photoshop软件,在图片上选取一个区域,由于孔隙和其他区域具有不同的灰度值,因此将孔隙的像素除以选中区域的像素就得到了孔隙率,每种涂层取3次测量的平均值。采用中性盐雾实验模拟海洋大气环境。按照GB/T10125-2021[26]开展实验,NaCl浓度5% (质量分数),温度 (35±1) ℃,pH范围为6.5~7.2。盐雾实验时间2400 h,在不同时间节点将两种涂层试样取出后,用去离子水冲洗干净、吹干,然后采用各种分析测试方法对样品的腐蚀行为进行表征分析。采用数码相机拍照记录两种涂层的宏观腐蚀形貌。利用Apreo S Hivac场发射SEM对两种涂层的表面及截面微观腐蚀形貌进行观察及能谱分析。利用Xpert PRO MPD型X射线衍射仪 (XRD) 分析腐蚀产物成分,XRD的工作管电压为40 kV,工作电流为40 mA,采用Cu Kα靶辐射,扫描方式为掠入射,对XRD测试数据用Jade6.5软件进行分析拟合。为便于试样表面腐蚀产物分析及截面试样腐蚀形貌观察,用于SEM微观形貌观察及XRD物相分析的试样均抛光后再开展盐雾实验。
腐蚀失重速率的测定按照JBT7901-1999[27]开展。首先采用精密天平 (精度0.1 mg) 准确称量样品重量,然后分别在盐雾腐蚀实验第1、2、5、10、20和30 d将样品取出,按照GB/T16545-2015[28]规定去除腐蚀产物,清洗吹干后再次称量样品重量,腐蚀速率按如下公式计算[27]:
(2)
式中,R为腐蚀速率 (mm/a),M和M1分别表示试样腐蚀前后的质量 (g),S为试样的表面积 (cm2),T为试样的腐蚀时间 (h),D为试样密度 (kg/m3),为保证数据可靠性,每个时间节点3个重复样品取平均值。
采用Zennium E4电化学工作站对盐雾腐蚀实验后样品进行电化学阻抗谱 (EIS) 测试。测试时间节点与失重实验相同,测试频率范围为105~10-2 Hz,激励信号交流正弦波幅值为10 mV,测试结果用ZsimpWin3.3软件拟合。
2 实验结果
2.1 两种涂层的物理性能
表2为5083铝合金涂层和Zn15Al涂层的涂层厚度、显微硬度、结合强度和孔隙率等物理性能参数。一般来说,电弧喷涂涂层的孔隙率低于5%时涂层质量较好[29],因此两种涂层均能对基体金属起到较好的保护作用。涂层厚度与结合强度亦能反应出涂层对基体的保护性能,5083铝合金涂层的厚度和结合强度略高于Zn15Al涂层,而孔隙率略低于Zn15Al涂层,表明5083铝合金涂层具有更优异的耐蚀性能。同时,5083铝合金涂层的显微硬度高于Zn15Al涂层,表明5083铝合金涂层具有较高的耐磨损性能。
表2 5083铝合金和Zn15Al涂层物理性能
2.2 两种涂层在中性盐雾环境下的腐蚀速率
中性盐雾环境下两种涂层的失重速率如图1所示,可以看出,5083铝合金涂层的腐蚀速率显著低于Zn15Al涂层,说明前者对基体金属的保护能力较好。腐蚀初期,两种涂层的腐蚀速率均较高,随着腐蚀时间的延长,两种涂层的腐蚀速率逐渐下降直至平稳,表明腐蚀后期由于腐蚀产物覆盖在涂层表面,从而堵塞了涂层的孔隙,对金属起到保护作用,使得腐蚀速率减缓。5083铝合金的稳态腐蚀速率为0.210 mm/a,Zn15Al涂层的稳态腐蚀速率为1.362 mm/a。
图1 中性盐雾环境下两种涂层的腐蚀速率
2.3 两种涂层的腐蚀形貌
图2为5083铝合金涂层和Zn15Al涂层在中性盐雾环境下的表面宏观腐蚀形貌。5083铝合金涂层腐蚀初期表现出明显的局部腐蚀特征,腐蚀2 d时涂层表面形成了大面积白色的腐蚀产物,但覆盖不均匀;随着腐蚀时间的延长,样品表面腐蚀产物越来越多,30 d时腐蚀产物已经覆盖了涂层大部分表面,至100 d时涂层已基本被腐蚀产物所覆盖。对于Zn15Al涂层,其腐蚀表现为均匀腐蚀,涂层表面均匀的覆盖有白色腐蚀产物;随腐蚀时间延长,腐蚀产物增厚,30和100 d时涂层表面呈现致密、完整的腐蚀产物层。
图2 5083铝合金和Zn15Al涂层在中性盐雾环境下的表面宏观腐蚀形貌
图3分别是5083铝合金涂层和Zn15Al涂层在中性盐雾环境下表面微观腐蚀形貌。5083铝合金涂层的腐蚀产物较为致密,随着腐蚀时间的延长,腐蚀产物之间紧密连接形成块状。腐蚀至100 d时,腐蚀产物已经变得十分致密,在内应力作用下形成龟裂状的腐蚀形貌。EDS分析可知,腐蚀产物中以O、Al和Mg为主,并掺杂有2.15% Cl,腐蚀性Cl可能沉积在腐蚀产物层表面,其是否渗透扩散至涂层中将在后续截面形貌中具体说明。Zn15Al涂层的腐蚀产物形貌与5083铝合金涂层明显不同,腐蚀产物主要呈细针状和细小腐蚀颗粒,没有形成大块完整致密的腐蚀产物层。EDS分析可知,腐蚀产物中Zn成分占主导,同时含有O、Al及少量Cl,Cl可能沉积在腐蚀产物层中亦可能渗入涂层基体中,待后续通过截面形貌进一步分析。
图3 中性盐雾环境下5083铝合金和Zn15Al涂层表面微观腐蚀形貌
5083铝合金涂层和Zn15Al涂层在中性盐雾环境下截面微观腐蚀形貌如图4和5所示。为便于观察区分涂层与腐蚀产物层,截面试样在盐雾腐蚀实验前先对表面进行抛光处理。如图3所示,5083铝合金涂层在腐蚀前5 d腐蚀产物较薄,较难观察到;随腐蚀时间延长,略有腐蚀产物生成但未完全覆盖在涂层表面;腐蚀时间延长至100 d时,腐蚀产物层平均厚度最厚达到41 μm,且分布仍不均匀。同时,从截面扫描EDS结果中可以看出,腐蚀至100 d时Cl仍未渗入进涂层中。图5中,Zn15Al涂层的腐蚀产物在腐蚀初期第2 d便少量成形,随着腐蚀时间延长,腐蚀产物逐渐增厚,呈现絮状腐蚀产物的特征;腐蚀100 d时,腐蚀产物层厚度约为223 μm,整体均匀的覆盖在涂层表面。结合EDS能谱分析,10 d时Zn15Al涂层的腐蚀产物层中即有Cl的渗入,100 d时Cl通过腐蚀产物层大量渗入至涂层基体中,表明Zn15Al涂层的致密性欠佳,其中,孔洞为Cl渗入提供扩散通道,加速了涂层基体的腐蚀。
图4 中性盐雾环境下5083铝合金涂层截面微观腐蚀形貌
图5 中性盐雾环境下Zn15Al涂层截面形貌
两种涂层在中性盐雾环境下的腐蚀产物厚度如表3所示。Zn15Al涂层的腐蚀产物层厚度大于5083Al合金涂层的腐蚀产物层厚度,说明Zn15Al涂层的腐蚀速率快于5083Al合金涂层。并且,Zn15Al涂层中Cl的渗入进一步证明了涂层的致密性欠佳,Zn15Al腐蚀产物层表现出厚度大但不致密的特征,因此该腐蚀产物层对涂层基体的保护作用较弱,表现出较高的腐蚀速率。
表3 中性盐雾环境下腐蚀产物层厚度
2.4 腐蚀产物成分
对5083铝合金涂层和Zn15Al涂层进行腐蚀产物成分分析,两种涂层经盐雾腐蚀100 d后的XRD如图6所示。5083铝合金腐蚀产物层中主要由Al单质、尖晶石结构的MgAl2O4和腐蚀产物Al(OH)3、Al2O3组成。MgAl2O4是铝合金在熔炼过程中由Al2O3和MgO高温烧结而成的,其结构致密,化学稳定性好,反应式如 式 (3) 所示[30,31]。大气环境下Al发生腐蚀的电化学反应如 式 (4) 和 (5) 所示,总反应如 式 (6) 所示[32],Al2O3为Al(OH)3脱水产物,两者均不易溶解,性能较稳定。Zn15Al涂层的腐蚀产物主要由Zn(OH)2和Zn5(OH)8Cl2·H2O组成,亦有少量的Al(OH)3生成。在腐蚀过程Zn发生溶解,与OH-结合生成Zn(OH)2,对应阳极、阴极的电化学反应如 式 (7) 和 (5) 所示,总反应如 式 (8) 所示,当Cl-侵入涂层时将会生成锌的碱式氯化盐Zn5(OH)8Cl2·H2O,反应如 式 (9) 所示[33]。这种以部分离子取代原有腐蚀产物结构中的空位从而形成新的腐蚀产物的过程,使得这些碱式复盐疏松、易溶[34,35]。
图6 中性盐雾环境下腐蚀100 d后两种涂层的XRD谱
2.5 电化学阻抗谱
5083Al合金涂层和Zn15Al涂层经盐雾腐蚀实验后,将其浸没于3.5% NaCl溶液中进行EIS测试,结果如图7和8所示。根据阻抗谱的特征,将5083铝合金涂层的腐蚀分两个阶段。腐蚀初期 (1~2 d),Nyquist图在低频段表现为45°斜线,说明存在扩散行为,这是由于涂层表面存在孔隙,腐蚀介质向涂层内部扩散所致。随腐蚀时间延长 (5~30 d),Nyquist图中低频扩散现象消失,这是因为腐蚀产物逐渐堵塞了孔隙,不再有腐蚀介质的扩散。并且,从图7b的Bode图中可以看出,相位角峰不对称且明显宽化,表现出两个时间常数的特征。因此,采用如下图7c和d的等效电路图分别拟合上述两个阶段的电化学阻抗谱,其中Rs表示溶液电阻,Rc表示涂层电阻,Rct表示电荷转移电阻,Rp为极化电阻,为Rs、Rc、Rct之和,代表了体系的总阻抗大小,Qc和Qct为相位角元件,拟合结果如表4所示。
图7 5083铝合金涂层电化学阻抗谱及等效电路
图8 Zn15Al涂层电化学阻抗谱及拟合电路
表4 5083铝合金涂层EIS拟合结果
免责声明:本网站所转载的文字、图片与视频资料版权归原创作者所有,如果涉及侵权,请第一时间联系本网删除。
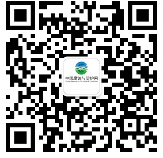
官方微信
《腐蚀与防护网电子期刊》征订启事
- 投稿联系:编辑部
- 电话:010-62316606
- 邮箱:fsfhzy666@163.com
- 腐蚀与防护网官方QQ群:140808414