涂层电阻Rc在腐蚀1~5 d内逐渐变小,表明涂层表面的氧化膜受到破坏,且并未生成腐蚀产物层,5~30 d Rc值逐渐增大并呈现较大波动,说明涂层表面不断发生着钝化膜的溶解与腐蚀产物的生成,两者存在竞争关系,腐蚀第30 d时由于生成了较多腐蚀产物,Rc再次增大。Rct的变化趋势是逐渐增大,并且Rct?Rc,说明随着腐蚀进行,腐蚀产物的传输过程逐渐成为控制腐蚀过程的主要因素。由于腐蚀产物堵塞了涂层的孔隙,造成离子扩散难度增加和涂层导电面积减小,Rct不断上升。Rp为极化电阻,代表了体系的总阻抗大小,阻抗膜值随腐蚀时间逐渐增大,说明腐蚀产物层阻碍了腐蚀性离子的渗入及对基体的破坏,其作为物理屏障保护了基体,减缓了腐蚀速率,此结果与腐蚀失重结果一致。
图8a和b分别是Zn15Al涂层的Nyquist图和Bode图,同样采用两个时间常数对阻抗谱进行拟合,拟合电路如下图8c所示,拟合结果见表5。根据表5中的拟合结果,Zn15Al涂层的腐蚀过程也可分为两个阶段。腐蚀初期(1~5 d),膜层电阻Rc维持在较高水平,这是因为涂层表面覆盖着不均匀的ZnO膜,而腐蚀后期(10~30 d),Rc下降一个数量级。结合图5不难看出,由于絮状腐蚀产物层致密性欠佳,10 d后腐蚀性Cl-已渗入至腐蚀产物层中,导致膜层的耐蚀性能显著降低,因此Rc迅速降低。但随着腐蚀时间延长,Rct由初期的几欧姆升高至后期的几百欧姆,这表明腐蚀产物层的堆积对涂层孔隙起到了封堵作用,阻碍腐蚀介质向内部扩散,减缓了涂层基体的腐蚀速率,因此Rct显著升高。随时间延长,Zn15Al涂层体系Rp不断增大,说明涂层的腐蚀速率不断降低,耐蚀性能提高,该结论与腐蚀失重结果一致,但Zn15Al涂层的阻抗膜值总体低于5083Al合金涂层,5083Al合金涂层的耐蚀性能更优异。两种涂层极化电阻对比值如图9所示。
表5 Zn15Al涂层EIS拟合结果
图9 中性盐雾环境下两种涂层的极化电阻对比
3 分析及讨论
对两种涂层进行盐雾加速腐蚀实验,腐蚀形貌及腐蚀失重结果表明,腐蚀初期5083铝合金涂层表现为局部腐蚀,而Zn15Al涂层为均匀腐蚀,且5083铝合金涂层腐蚀速率低于Zn15Al涂层。这是因为5083铝合金涂层中,作为固溶强化的主要合金元素Mg[36],部分以β-Al3Mg2相析出,β相电极电位低于Al基体而发生优先溶解,形成初期局部腐蚀形貌。β相溶解后裸露出Al基体发生自钝化生成Al2O3,Al2O3的PBR值约为1.5,致密性较好,能完整覆盖在Al基体表面,起到保护和修复涂层的作用。β相与Al基体间的微电偶作用抑制了Al基体的全面腐蚀,降低Al基体的腐蚀速率。此外,Ren等[37]研究表明,Mg可以降低Al基体的表面能来降低其腐蚀速率。同时,铝合金在熔炼过程中,Al2O3和MgO高温烧结形成尖晶石结构MgAl2O4,其结构致密,化学稳定性好,阻碍了Cl-渗透扩散,在提高铝合金涂层耐蚀性方面也有一定的积极作用。而Zn15Al涂层中,Al含量仅占15%,主要元素Zn的自钝化能力明显低于Al,因此Zn15Al涂层表面氧化膜保护性欠佳,初期腐蚀速率高于5083铝合金涂层。
随腐蚀时间的延长,两种涂层的腐蚀产物逐渐覆盖了涂层表面,腐蚀后期5083铝合金涂层呈致密的块状腐蚀形貌,直至100 d时腐蚀产物层中仍无Cl渗入。Zn15Al涂层发生均匀腐蚀,腐蚀产物为絮状疏松的细针状形貌,10 d时腐蚀产物层中即有Cl渗入,并进一步扩散至涂层基体。以上腐蚀形貌观察结果表明,5083铝合金涂层表面腐蚀产物层薄而致密,而Zn15Al涂层的腐蚀产物层虽厚但疏松。
结合XRD实验结果,5083铝合金涂层的腐蚀产物主要由Al(OH)3组成,Zn15Al涂层的腐蚀产物主要为Zn(OH)2和Zn5(OH)8Cl2·H2O。Cl-侵入涂层时生成的碱式氯化锌Zn5(OH)8Cl2·H2O易溶于水,对涂层的保护作用甚微,这里不再讨论。对于难溶性Al(OH)3和Zn(OH)2,这些腐蚀产物沉积在涂层表面,有利于提高涂层的自封闭作用,切断腐蚀介质的渗入,提高涂层的耐蚀性能,现详细讨论难溶性腐蚀产物对涂层基体的防护作用。
对难溶物而言,可通过热力学的溶度积常数Ksp表示其溶解/沉淀的难易程度,其饱和溶液存在如下平衡:
(10)
该平衡的平衡常数Ksp可表示为:
(11)
溶度积常数代表了生成沉淀所需的最低离子浓度的沉积。由兰氏化学手册可得,25 ℃中性溶液中Al(OH)3、Mg(OH)2和Zn(OH)2的Ksp分别为1.33×10-33、5.6×10-12和1.2×10-17 kJ/mol [38],将其代入 式(11)计算可得,生成沉淀需要的极限离子浓度分别为c(Al3+)=1.33×10-12 mol/L,c(Mg2+)=5.61×102 mol/L和c(Zn2+)=1.2×10-3 mol/L,即Al(OH)3沉淀所需的阳离子比Zn(OH)2低9个数量级。因此,Al(OH)3更易形成沉淀覆盖在涂层表面。
动力学方面,腐蚀产物的沉积速率与其在盐雾氛围中的过饱和度相关。过饱和度是指实际环境中金属离子浓度与其形成沉淀所需的最低浓度的比值,可表示为[39]:
(12)
其中,c为实际环境中金属离子的浓度,c*为沉积所需最低离子浓度。假设体积V为一单位常数1,则实际环境中的金属离子浓度c可通过失重腐蚀结果获得,沉积所需的临界离子浓度c*可通过上述溶度积获得,代入 式(12)得到Al(OH)3和Zn(OH)2的过饱和度表达式:
计算结果如图10所示。可以看出,Al(OH)3过饱和度是Zn(OH)2的109倍,过饱和度与腐蚀产物的沉积速率成正比。因此,Al(OH)3的沉积速率快。上述分析从热力学和动力学角度共同印证了5083铝合金涂层的腐蚀产物层更加致密。
图10 Al(OH)3和Zn(OH)2的过饱和度
通过形貌观察和腐蚀产物成分分析,5083铝合金表面腐蚀产物层的致密性更优异。由于腐蚀产物层对涂层基体的孔隙起到封堵作用,减缓了基体的腐蚀速率,因此,在EIS测试中5083铝合金涂层表现出更高的阻抗值。并且,随时间延长,阻抗值逐渐增大,表明腐蚀产物层的堵塞作用进一步增强,这与腐蚀失重的结果相吻合,涂层的耐蚀性能主要与腐蚀产物层的阻碍作用相关。综上,5083铝合金涂层的耐蚀性能更好,更适合应用于海洋大气环境下对钢铁材料的表面涂层防护。
4 结论
(1) 5083铝合金涂层的厚度、显微硬度和结合强度均高于Zn15Al涂层,且孔隙率略低于Zn15Al涂层。
(2) 腐蚀形貌观察表明,5083铝合金涂层的腐蚀产物呈致密块状,Cl-无明显渗入;而Zn15Al涂层的腐蚀产物呈疏松的细针状,盐雾腐蚀10 d后有Cl-沉积在腐蚀产物层中并逐渐渗入至涂层基体。
(3) XRD结果表明,5083铝合金涂层的腐蚀产物主要为Al(OH)3,Zn15Al涂层腐蚀产物主要由Zn(OH)2和Zn5(OH)8Cl2·H2O组成。溶度积常数和过饱和度的理论计算表明,Al(OH)3更倾向于以更低Al3+的浓度、更快的速率沉积在涂层表面。因此,5083铝合金涂层的腐蚀产物层更加致密。
(4) 通过EIS测试可得,两种涂层的极化电阻随腐蚀时间逐渐增大,且5083铝合金涂层的极化电阻高于Zn15Al涂层。这一结果与腐蚀产物致密性相吻合,也与腐蚀失重结果一致,说明腐蚀产物致密性是影响两种涂层耐蚀性能的主要原因。
参考文献
1 Liu S, Wang Y P, Wang S F. Several discussions on metal corrosion and protection [J]. Mod. chem. Res., 2022, (09): 23
1 刘 帅, 王艺澎, 王少峰. 金属腐蚀与防护问题的若干探讨 [J]. 当代化工研究, 2022, (09): 23
2 Xie C F. Introduction to metal corrosion principle and protection [J]. Total Corros. Control, 2019, 33(07): 18
2 谢春峰. 金属腐蚀原理及防护简介[J]. 全面腐蚀控制, 2019, 33(07): 18
3 Wang Y X, Zhang Y, Zhang C M, et al. The development and application of arc spraying technology [J]. Agric. Equip. Veh. Eng., 2010, (03): 26
3 王有喜, 张 勇, 张春明 等. 电弧喷涂技术的发展及应用 [J]. 农业装备与车辆工程, 2010, (03): 26
4 Zeng Z, Sakoda N, Tajiri T. Corrosion behavior of wire-arc-sprayed stainless steel coating on mild steel [J]. J. Therm. Spray Technol., 2006, 15: 431
doi: 10.1361/105996306X124446
5 Chen T C, Chou C C, Yung T Y, et al. Wear behavior of thermally sprayed Zn/15Al, Al and Inconel 625 coatings on carbon steel [J]. Surf. Coat. Technol., 2016, 303: 78
doi: 10.1016/j.surfcoat.2016.03.095
6 Rogers F S. Thermal spray for commercial shipbuilding [J]. J. Therm. Spray Technol., 1997, 6: 291
doi: 10.1007/s11666-997-0060-2
7 Wood R J K, Speyer A J. Erosion-corrosion of candidate HVOF aluminium-based marine coatings [J]. Wear, 2004, 256: 545
doi: 10.1016/S0043-1648(03)00564-7
8 Soechting F O. A design perspective on thermal barrier coatings [J]. J. Therm. Spray Technol., 1999, 8: 505
doi: 10.1361/105996399770350179
9 Toma D, Brandl W, Marginean G. Wear and corrosion behaviour of thermally sprayed cermet coatings [J]. Surf. Coat. Technol., 2001, 138: 149
doi: 10.1016/S0257-8972(00)01141-5
10 Wang B Q. Erosion-corrosion of thermal sprayed coatings in FBC boilers [J]. Wear, 1996, 199: 24
doi: 10.1016/0043-1648(96)06972-4
11 Hermanek F J. Automation of the thermal spray process [J]. SAE Trans., 1982, 91: 2213
12 Jandin G, Liao H, Feng Z Q, et al. Correlations between operating conditions, microstructure and mechanical properties of twin wire arc sprayed steel coatings [J]. Mater. Sci. Eng., 2003, 349A: 298
13 Chaliampalias D, Vourlias G, Pavlidou E, et al. High temperature oxidation and corrosion in marine environments of thermal spray deposited coatings [J]. Appl. Surf. Sci., 2008, 255: 3104
doi: 10.1016/j.apsusc.2008.08.101
14 Choe H B, Lee H S, Shin J H. Experimental study on the electrochemical anti-corrosion properties of steel structures applying the arc thermal metal spraying method [J]. Materials, 2014, 7: 7722
doi: 10.3390/ma7127722
15 Paredes R S C, Amico S C, d'Oliveira A S C M. The effect of roughness and pre-heating of the substrate on the morphology of aluminium coatings deposited by thermal spraying [J]. Surf. Coat. Technol., 2006, 200: 3049
doi: 10.1016/j.surfcoat.2005.02.200
16 Schmidt D P, Shaw B A, Sikora E, et al. Corrosion protection assessment of barrier properties of several zinc-containing coating systems on steel in artificial seawater [J]. Corrosion, 2006, 62: 323
doi: 10.5006/1.3280665
17 Hudson J C, Stanners J F. The effect of climate and atmospheric pollution on corrosion [J]. J. Appl. Chem., 1953, 3: 86
doi: 10.1002/jctb.5010030208
18 Hoar T P, Radovici O. Zinc-aluminium sprayed coatings [J]. Trans. IMF, 1964, 42: 211
doi: 10.1080/00202967.1964.11869929
19 Kuroda S, Kawakita J, Takemoto M. An 18-year exposure test of thermal-sprayed Zn, Al, and Zn-Al coatings in marine environment [J]. Corrosion, 2006, 62: 635
doi: 10.5006/1.3280677
20 Büteführ M. Zinc-aluminium-coatings as corrosion protection for steel [J]. Mater. Corros., 2007, 58: 721
doi: 10.1002/(ISSN)1521-4176
21 Jiang Q, Miao Q, Liang W P, et al. Corrosion behavior of arc sprayed Al-Zn-Si-RE coatings on mild steel in 3.5% NaCl solution [J]. Electrochim. Acta, 2014, 115: 644
doi: 10.1016/j.electacta.2013.09.156
22 Xiao Y X, Jiang X H, Xiao Y D, et al. Research on Zn-Al15 thermal spray metal coating and its organic painting composite system protection performance [J]. Proc. Eng., 2012, 27: 1644
doi: 10.1016/j.proeng.2011.12.632
23 Asgari H, Toroghinejad M R, Golozar M A. Effect of coating thickness on modifying the texture and corrosion performance of hot-dip galvanized coatings [J]. Curr. Appl. Phys., 2009, 9: 59
doi: 10.1016/j.cap.2007.10.090
24 State Administration for Market Regulation, Standardization Administration of the People's Republic of China. GB/T 9790-2021 Metallic materials—Vickers and Knoop microhardness tests of metallic and other inorganic coatings [S]. Beijing: Standards Press of China, 2021
24 国家市场监督管理总局, 国家标准化管理委员会. GB/T 9790-2021 金属材料 金属及其他无机覆盖层的维氏和努氏显微硬度试验 [S]. 北京: 中国标准出版社, 2021
25 General Administration of Quality Supervision, Inspection and Quarantine of the People's Republic of China.GB/T 8642-2002Thermal spraying--Determiantion of tensile adhesive strength [S]. Beijing: Standards Press of China, 2003
25 中华人民共和国国家质量监督检验检疫总局. GB/T 8642-2002 热喷涂 抗拉结合强度的测定 [S]. 北京: 中国标准出版社, 2003
26 State Administration for Market Regulation, Standardization Administration of the People's Republic of China. GB/T 10125-2021 Corrosion tests in artificial atmospheres—Salt spray tests [S]. Beijing: Standards Press of China, 2021
26 国家市场监督管理总局, 国家标准化管理委员会. GB/T 10125-2021 人造气氛腐蚀试验 盐雾试验 [S]. 北京: 中国标准出版社, 2021
27 State Administration of Machinery Industry, Instrument Functional Materials Standardization Technical Committee. JB/T 7901-1999 Metals materials-Uniform corrosion - Methods of laboratory immersion testing [S]. Beijing: China Machine Press, 2004
27 国家机械工业局, 仪表功能材料标准化技术委员会. JB/T 7901-1999 金属材料实验室均匀腐蚀全浸试验方法 [S]. 北京: 机械工业出版社, 2004
28 General Administration of Quality Supervision, Inspection and Quarantine of the People's Republic of China, Standardization Administration of the People's Republic of China. GB/T 16545-2015 Corrosion of metals and alloys-Removal of corrosion products from corrosion test specimens [S]. Beijing: Standards Press of China, 2016
28 中华人民共和国国家质量监督检验检疫总局, 中国国家标准化管理委员会. GB/T 16545-2015 金属和合金的腐蚀 腐蚀试样上腐蚀产物的清除 [S]. 北京: 中国标准出版社, 2016
29 Wang F. Corrosion bahaviors of Zn, Al, and ZnAl coatings in simulated deep-ocean environment [D]. Qingdao: China University of Petroleum (East China), 2015
29 王 芳. 电弧喷涂Zn、Al、ZnAl涂层在模拟深海环境下的腐蚀行为研究 [D]. 青岛: 中国石油大学(华东), 2015
30 Liu W, Lan Z, He L Z. Types and source of inclusions in 5182 aluminum alloy melt [J]. Light Alloy Fabr. Technol., 2018, 46(3): 15
30 刘 旺, 兰 政, 何立子. 5182 铝合金熔体夹渣物种类及其来源研究 [J]. 轻合金加工技术, 2018, 46(3): 15
31 Chen W P. Study on reaction behavior of in-situ MgAl2O4 spinel formation [D]. Suzhou: Soochow University, 2017
31 陈伟鹏. 氧化镁—氧化铝原位合成镁铝尖晶石反应行为的研究 [D]. 苏州: 苏州大学, 2017
32 Grilli R, Baker M A, Castle J E, et al. Localized corrosion of a 2219 aluminium alloy exposed to a 3.5% NaCl solution [J]. Corros. Sci., 2010, 52: 2855
doi: 10.1016/j.corsci.2010.04.035
33 Yin Q. Study on the corrosion mechanism of zinc with different influence factors in simulated atmosphere [D]. Hefei: University of Science and Technology of China, 2019
33 尹 奇. 模拟大气环境下不同影响因子对锌腐蚀的作用机制研究 [D]. 合肥: 中国科学技术大学, 2019
34 Rodriguez J J S, ?lvarez C M, Gonzáalez J E G. EIS characterisation of the layer of corrosion products on various substrates in differing atmospheric environments [J]. Mater. Corros., 2006, 57: 350
doi: 10.1002/(ISSN)1521-4176
35 Odnevall I, Leygraf C. Formation of NaZn4Cl (OH)6SO4·6H2O in a marine atmosphere [J]. Corros. Sci., 1993, 34: 1213
doi: 10.1016/0010-938X(93)90082-R
36 Gao W B. Sensitization behavior and environmentally assisted cracking of AA5083-H128 Al-Mg navy alloy [D]. Tianjin: Tianjin University, 2018
36 高文斌. 船舰用铝镁合金AA5083-H128的敏化析出行为和环境敏感断裂 [D]. 天津: 天津大学, 2018
37 Ren J M, Ma J B, Zhang J, et al. Electrochemical performance of pure Al, Al-Sn, Al-Mg and Al-Mg-Sn anodes for Al-air batteries [J]. J. Alloy. Compd., 2019, 808: 151708
doi: 10.1016/j.jallcom.2019.151708
38 Dean J A. Lange's Handbook of Chemistry [M]. 13th ed. New York: McGraw-Hill, 1985
39 Zhang S, Liu J, Tang M, et al. Role of rare earth elements on the improvement of corrosion resistance of micro-alloyed steels in 3.5% NaCl solution [J]. J. Mater. Res. Technol., 2021, 11: 519
doi: 10.1016/j.jmrt.2021.01.041
免责声明:本网站所转载的文字、图片与视频资料版权归原创作者所有,如果涉及侵权,请第一时间联系本网删除。
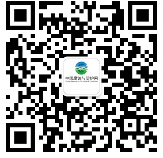
官方微信
《腐蚀与防护网电子期刊》征订启事
- 投稿联系:编辑部
- 电话:010-62316606
- 邮箱:fsfhzy666@163.com
- 腐蚀与防护网官方QQ群:140808414