声子诊断技术(Phonon Diagnosis Technology,PDT)是一种针对管道隐患治理工作中存在的占压、超埋深以及穿越管道而开发的检测评价管道本体的先进检测技术。其能够检测出管道本体的腐蚀、机械损伤、冶金缺陷、裂纹等问题,并能定量给出检测结果。本文介绍了声子诊断技术的基本原理、实施过程以及在国内的首个成功应用案例。证明可以应用在河流、高速公路、铁路、建筑物占压段管道本体检测和安全评价,同样可以对平台间海底管道、保温层下管道进行完整性评价。
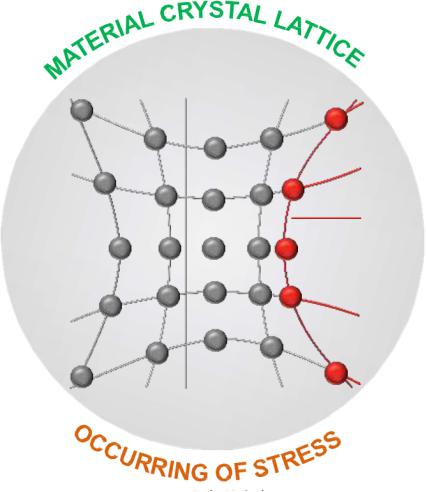
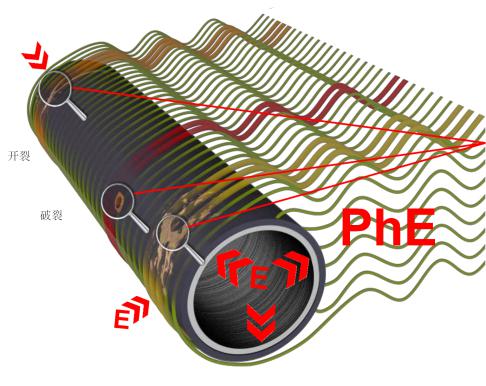
图2 声子产生宏观图
2.活跃与非活跃缺陷
原子链断裂释放出的声子能量信号被采集,该区域即声子活跃区域(PhAA)。信号数据被传入软件,结合被检测物的基本技术数据和现场测量参数,进行数据分析。活跃缺陷是指在活跃区域的一种累积的或正在发生的活动。它正在发生,而且不断增长。这种缺陷的发展随着正常的声子能量在结晶状态形成的能量格的过程而发展。非活跃缺陷或异常是指在活动区域没有进一步的活动,或缺陷形成是在声子能量无法量化的非正常过程中,即人为的、维修过的、箍下的针孔或简单的缺陷,没有使金属恶化的迹象。
3.适用范围
声子能量的单位是分贝(db),其数值低于5分贝。声子诊断检测基本不受到外界干扰,因为它只收集低于5分贝的声子能量。收集到的声子活跃区数据用专有软件进行处理可以确定缺陷的位置,类型和严重程度。声子诊断技术通过分析声子活跃区声子发射所产生的信号来区分缺陷的类型。它可以识别的缺陷类型有腐蚀缺陷、机械损伤、制造缺陷、应力腐蚀、氢脆、类似裂纹缺陷。处理过的数据被用于分析技术对象的实际状态,即存在明显的或潜在的缺陷,来预测技术对象的使用寿命、可能性和继续运行的条件。
实施过程
1.完善管道基本信息
声子诊断技术的实施方法,首先要收集管道的基本信息如建成年代、材质、管径、壁厚、防腐层材料、运行压力和温度等,这些基本信息对于检测结果有直接的影响,需最大可能保证其准确性。
2.确定传感器安装位置
传感器安装选在占压少并且易于开挖的位置,一般选在要检测管段的两端,管段长度不超过1公里。
3.预声子诊断(PRE-PD)
预声子诊断是指在声子监测之前验证两端传感器之间信号是否能形成通路,作为正式声子监测的前提。
4.声子监测(PD Monitor)
声子监测则是连续不间断进行声子能量信号采集,用于评价管道本体各位置的活跃型缺陷。
5.数据分析并出具报告
通过专业的软件对采集的数据进行分析,得出缺陷位置分布图,并确定出各处缺陷的类型、严重程度、截面方向、范围误差等参数,对缺陷进行定量定性分析。最终出具专业的检测报告来指导修复工作。
6.开挖验证
通过开挖比对,验证声子诊断管道各缺陷点是否准确。
应用案例
1.实施过程介绍
本次检测应用在中石化某输油管线上进行,表1为管道的基本信息。此段管道通过内检测发现有多处管体缺陷(大小在壁厚的6%--40%之间不等),通过声子诊断技术可以相互验证。现场没有直接占压,后期开挖验证方便。
表1 管道基本信息
名称 |
检测长度 |
建设年代 |
材质 |
直径/壁厚 |
设计/运行压力 |
温度 |
介质 |
防腐层材料 |
中石化某输油管线 |
1km |
1978年 |
16Mn |
720mm/8mm |
4.2Mpa/3.0Mpa |
常温 |
原油 |
沥青 |
经过现场勘查,确定传感器安装管道两端的位置,作为信号采集点。对管道开挖出长度3米、两侧各1米、管底悬空1米的操作坑,管道防腐层环向剥离宽度约为0.5米,并对管道进行清理打磨,露出金属光泽。
分别在起点和终点信号采集点安装PD探头,其中起点为主要检测点。启动设备,开始收集管道声子能量信号,进入预声子诊断过程。
上一步结束后,进入声子监测过程,此过程由设备不间断收集管道声子能量信号。
图3 管道走向平面图
图4 PDT数据采集系统
图5 起点PD探头
图6 终点PD探头
表2 PDT验证数据对照表
位置 |
内容 |
距原点距离(m) |
范围 (m) |
缺陷位置(hh:mm) |
最大深度(mm) |
深 度 (%) |
缺陷类型 |
验证结论 |
DF-1 |
报告 |
0 |
0±0.9 |
6:00 |
2.5±0.5 |
31.25 |
腐蚀 |
准确 |
验证 |
/ |
0~0.5 |
4:00-7:00 |
3.0 |
37.50 |
腐蚀 |
||
DF-23 |
报告 |
157.27 |
157.27±2.5 |
6:00 |
2.0±0.5 |
25.00 |
腐蚀 |
较准确 |
验证 |
/ |
154.5 |
12:00 |
1.1 |
13.75 |
焊接管 |
||
DF-26 |
报告 |
166.29 |
166.29±0.8 |
6:00 |
2.5±0.5 |
31.25 |
腐蚀 |
准确 |
验证 |
/ |
166.00 |
4:00-7:00 |
3.5 |
43.75 |
腐蚀 |
||
DF-28 |
报告 |
191.69 |
191.69±0.9 |
6:00 |
2.5±0.5 |
31.25 |
腐蚀 |
较准确 |
验证 |
/ |
191.5~192 |
4:00-8:00 |
1.5 |
18.75 |
机械损伤 |
DF-28在距离1#信号采集点约191.5~192米(604#+8.5~604#+9m)位置,在管道4~8点钟方向,发现多处机械损伤,形状类似于楔状,最大深度为1.5mm(图11)。
图7、DF-1 管道腐蚀坑
图8、DF-23焊接金属管
图9、DF-26管道腐蚀坑
图10、DF-28机械损伤
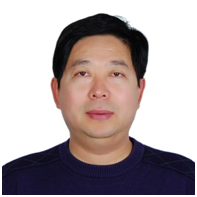
免责声明:本网站所转载的文字、图片与视频资料版权归原创作者所有,如果涉及侵权,请第一时间联系本网删除。
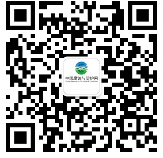
官方微信
《中国腐蚀与防护网电子期刊》征订启事
- 投稿联系:编辑部
- 电话:010-62316606-806
- 邮箱:fsfhzy666@163.com
- 中国腐蚀与防护网官方QQ群:140808414