被称为“工业之米”的紧固件(连接件)是应用最广泛的基础零件之一,在工程建筑、轨道交通、桥梁工程、矿井巷道、航空航天、军工装备等领域中扮演着至关重要、不可或缺的角色。然而,紧固件连接一旦失效,轻则影响装备的运行状态,造成经济损失,重则酿成重大灾难性事故,造成恶劣的社会影响。
高强度风电紧固件的质量问题主要表现为螺栓断裂、安装失效、螺纹脱扣等,其中螺栓断裂是最主要的质量问题,氢脆则是引起螺栓断裂的重要因素之一。
氢脆是指工件吸收原材料中的氢元素含氢过高而导致的韧度和延迟断裂强度降低的现象,这种现象是材料-环境-应力相互作用而发生的一种环境脆化,是氢导致材质恶化的一种形态。
氢脆现象是妨碍螺纹紧固件高强度化的一大因素,危害性极大,氢脆对螺栓的影响已经是一个研究螺栓断裂的重要方面。
金属中氢的来源有“内含”的及“外来”的两种:前者指材料在冶炼、热加工、热处理及随后的机械加工(如焊接、酸洗、电镀等)过程中所吸收的氢;而后者是指材料在致氢环境的使用过程中所吸收的氢。致氢环境既包括含有氢的气体,如H2,H2S等;也包括金属在水溶液中腐蚀时阴极过程所放出的氢。
研究表明,实际使用的螺栓在自然环境下发生氢脆断裂的主要是淬火的马氏体系钢,一般发生在屈服强度大于620 MPa,洛氏硬度大于31的高强度材料。材料中对氢脆敏感的影响因素是:随着钢的强度的提高,其变脆指数升高,而持久强度降低,说明钢的强度越高,对氢脆越敏感。
由于氢脆具有延迟性和突发性,所以它的危害很大。氢脆存在如下几个显著特征:
(1)恶化力学性能,特别是会显著降低材料的伸长率和断面收缩率;
(2)改变断裂机制,形成不同的断口形貌,主要表现为随材料中氢浓度的提高,断裂模式由延性韧窝断裂向脆性解理或沿晶断裂转变;
(3)断裂发生突然,无明显征兆,因而往往引起严重后果。
氢脆发生机理
氢脆开裂的实质是氢进入材料内部而导致裂纹形核和扩展,氢进入材料内部的过程如图1所示,导致氢脆失效必须同时具备三个条件:① 材料对氢损伤敏感;② 拉应力(通常来自外部施加的载荷或残余应力);③ 氢原子。如果这三个条件有足够的重叠量,在一定的时间内,氢损伤会导致裂纹的萌生和扩展,直至断裂发生。
图1 氢进入金属内部原理图
氢脆失效发生的时间可能会随着各种条件的严重程度和氢来源的不同而变化。应力和氢被认为是诱发因素,而材料的敏感性是氢脆发生的根本原因,如图2所示。
图2 延迟氢脆失效的三个必要条件的交集
目前普遍认为氢脆发生的主要理论如下:
(1) 氢压理论:氢原子进入材料内部后,一部分氢原子被各种氢陷阱(如位错、晶界、第二相等)捕获达到局部平衡,而另外一部分氢原子会在材料内部复合成氢分子,存在于微裂纹、孔洞及开裂的第二相界面等空腔。
一旦氢原子复合成氢分子,就会导致空腔周围的氢浓度下降,并且氢压的产生使空腔周围形成一个应力场,远处的氢原子会在浓度梯度和应力梯度的作用下不断地向空腔迁移。
当空腔内氢气压力值达到材料的屈服强度时,空腔周围的材料就会发塑性变形。如果空腔位于材料近表面,材料的屈服变形将导致表面产生氢鼓泡,引发氢致裂纹。
氢压理论解释了钢中白点、酸洗及电镀裂纹等无外加应力的氢脆现象,但对于氢原子导致的可逆塑性损失及拉伸加载时的氢致开裂等现象并不适用。
(2) 弱键理论:Troiano理论模型认为氢原子进入晶格间隙时,氢的ls电子进入过渡族金属的d带,使d带电子密度升高,s与d带重合部分增大,因而原子间排斥力增加。
另外,当氢原子在裂纹尖端应力集中区域偏聚时,局部氢原子聚集产生的氢压会促进裂纹尖端基体界面处的金属原子键断裂,加速裂纹的萌生与扩展,使主裂纹快速失稳断裂。
弱键理论基于假设裂纹的萌生与扩展是完全由应力作用下金属原子键断裂的结果,其断裂扩展所消耗的能量主要来源于表面能的增加,并且应力诱导下聚集的氢原子可大大降低金属原子键的结合力。氢原子导致金属键弱化的理论仅适用于脆性材料,而对于塑性变形过程并不适用。
(3) 氢原子降低表面能理论:基于弱键理论提出了氢原子降低表面能理论,即氢原子吸附在金属表面或任何一个可以当作表面的内部缺陷,使表面的化学位发生变化,表面能下降,使裂纹易于形核和扩展。
该理论认为裂纹尖端表面存在的应力集中可吸附氢原子,降低材料的表面能,临界应力降低而引发氢脆,该理论同样没有考虑钢中塑性变形的情况。
(4) 氢原子促进局部塑性变形理论:上世纪80年代实验发现,氢原子可以促进裂纹表面位错运动与增殖。氢原子进入钢中后,会偏聚在位错或其它弹性缺陷的应力场附近形成Cottrell气团,位错密度越高的区域聚集的氢浓度越大。
位错上的氢原子会降低位错间及位错与第二相间的交互作用能,使位错运动的阻力减小且可动性增强,导致裂纹尖端应力集中区域偏聚了大量位错及氢原子,从而引发局部塑性变形。
虽然塑性变形能够在一定程度上缓解裂纹尖端应力集中而钝化裂纹,但是剧烈的局部塑性变形会使裂纹尖端产生大量的微孔洞,主裂纹通过不断兼并微孔洞导致材料的塑性急剧下降并最终发生断裂,使断口形貌呈现局部韧窝和准解理的混合断裂特征,但是此理论很难解释完全解理的脆性断裂行为。
(5) 氢原子促进应变诱发空位形成理论:基于氢脆断口中小而浅的纳米韧窝形貌,有学者提出了氢原子促进应变诱发空位形成理论。理论认为氢原子的聚集会促进空位的形成并加速空位的合成,导致微孔洞的形成以及裂纹尖端逐渐失稳而发生断裂。
氢原子不仅促进位错的运动并发生塑性变形导致空位的形成;而且可以稳定已形成的空位,促进空位的形成及合并,这与氢原子促进局部塑性变形理论类似。
氢脆的影响因素
1 外部因素
(1) 温度:氢脆在-30~30 ℃最敏感,一般发生在-100~150 ℃范围内,在低温或高温时氢脆敏感性降低。随温度的升高,氢在金属中的溶解度、扩散速率升高。温度不仅有利于氢渗透也有利于氢的复合,是一种双重影响。
(2) pH值:pH值的大小直接决定了H+的含量,进而可能影响氢的生成,但并不是简单的pH值越低氢脆越容易发生。不同的材料和溶液会有不同的影响结果,通常情况下,由于pH降低,H+增多有利于氢的产生,氢脆敏感性升高。有研究发现,电镀中pH降低有利于能抑制氢脆的富钴相的形成,从而降低了材料的氢脆敏感性。
(3) 氧化还原电位:电位越负越有利于析氢反应的发生,因此更有利于氢脆的发生。电位降低,氢脆敏感性增高,特别是在对材料进行阴极保护时,控制保护电位对预防氢脆更重要。
(4) 特殊离子的影响:环境中的离子主要通过影响氢的产生,进而影响材料的氢脆。其中由于硫化氢或硫离子引发的应力腐蚀开裂是目前国内外学者研究的焦点,特别是在研究含硫原油输油管道的环境脆断时,氢脆机理以硫化氢氢脆为主。亚硫酸根离子也能促进氢渗透,特别是在含有二氧化硫的大气氢渗透中作用更明显。其他的离子如氯离子能破坏金属氧化膜,间接促进氢渗透,而且含氯离子环境如海洋环境等是材料脆断的敏感介质,对氢脆也有一定的影响。
(5) 热处理:对于高强度螺纹紧固件,尤其是10.9级和12.9级螺栓,不但使用中碳合金结构钢,而且还要进行热处理。如在淬火加热时,较高的加热温度下,氢很容易渗入工件应力集中的区域如螺栓头杆结合处。
(6) 酸洗:酸洗是把工件放在稀盐酸中搅动10~15 min,是工件电镀过程中产生渗氢作用的主要环节。在酸洗中钢所吸收的氢含量随时间的平方根而成线性增长达到饱和值,在pH值较低的溶液中其饱和值较高,而pH值较高时则饱和值较低。
(7) 电镀除油:渗氢的环节主要存在于电镀除油中,由于阴极除油的速度较快,生产中多采取阴极和阴阳极交替联合除油,但阴极除油过程会产生大量的氢原子附着在工件表面,从而产生渗氢。在电镀镀锌过程中,阴极上除了锌的沉积外还有氢的析出,因此,镀锌时同样会产生渗氢现象。由于锌有阻止氢渗透作用,当工件表面沉积一层锌后该镀层将阻碍氢原子向工件内部扩散。同理,若工件在镀锌前已有渗氢,镀锌后,其内部的氢亦不易逸出。
2 内部因素
(1) 材料强度水平:一般氢脆敏感性随材料硬度、强度的升高而增高,由于应力梯度有利于氢扩散,所以材料在使用、焊接等处理工艺过程中造成的残余应力会使其氢脆敏感性提高。
(2) 合金元素:氢与不同的金属元素的结合作用能力、在其中的扩散速度不同造成不同金属材料的氢脆敏感性也不同。如在铁镍二元合金中,氢的渗透速度随镍含量的增加而增大,钛合金对氢脆的敏感性较其他金属更高,已经成为研究热点;铁铝合金中炭或铝的含量升高能适当抑制氢脆。
(3) 材料微观结构:不同的金属以及合金都有不同的微观结构,氢原子在金属中主要是通过晶界或空隙扩散,而且主要偏聚在晶界,夹杂物等缺陷处。位错密度越高,越有利于氢的扩散传输,从而增高氢脆敏感性;相反金属碳化物、晶间沉积物、转变奥氏体结构等的数量越多,分布越均匀,氢脆敏感性越低,且材料的晶粒越细、分布越均匀、缺陷越少,材料抗氢脆性能越好。
不同晶体结构中,由于强度级别高,且含有大量的位错、板条界等组织缺陷,马氏体比贝氏体、珠光体、铁素体、奥氏体、沉积硬化钢的氢脆敏感性高;贝氏体比珠光体、铁素体的氢脆敏感性高;抑制氢脆方面奥氏体不如铁素体,虽然与马氏体具有相同的晶体结构,但点阵常数的差异会导致铁素体/马氏体相界附近产生一定的畸变能,并在铁素体中形成较高密度的可动位错,可带动氢原子发生迁移,而且两相的比例及晶粒大小也影响氢脆敏感性。
紧固件氢脆现象研究现状
北京航空材料研究所等针对几种不同螺栓氢脆失效开展相关研究:
(1) 某固体火箭发动机燃烧室壳体后封头螺钉在加压至11.8 MPa时断裂失效,低于设计要求的24.1 MPa,螺钉材料为30CrMnSiNi2A超高强度钢。
螺钉均断裂于第一扣螺纹处,断口的宏观特征呈暗灰色,断口平齐,断面可见放射棱线,如图3所示,断口上存在两个不同的区域特征:Ⅰ区呈结晶颗粒状,Ⅱ区呈纤维状。Ⅰ区(源区)微观呈沿晶形貌,晶粒轮廓鲜明,晶界面上布满了细小条状的撕裂棱线,可见“鸡爪状”形貌和二次裂纹,Ⅱ区呈韧窝断裂特征。测试结果显示,螺钉基体的氢含量质量分数均小于0.0001%,质量分数小于0.0001%的氢含量并不易导致30CrMnSiNi2A螺钉发生氢致脆性断裂。
图3 断口形貌
材质检查表明,螺钉的显微组织均为回火马氏体、下贝氏体及少量的残余奥氏体。螺钉的硬度值为49 HRC左右,抗拉强度σb约为1690 MPa,然而,螺钉材料的初始设计强度σb=(1500±98) MPa。螺钉的断裂原因主要是由于螺钉材料的抗拉强度偏高,增大了螺钉的氢脆敏感性。
(2) 30CrMnSiNi2A螺栓在使用过程中发生大量开裂或断裂现象,检测结果发现螺栓的组织正常,显微硬度测试结果换算所得的洛氏硬度和抗拉强度符合技术要求,而测得基体的氢含量质量分数为0.0004%左右。工程经验表明,该氢含量足以使30CrMnSiNi2A钢发生氢脆断裂,因此,螺栓的断裂主要与氢含量过高有关。
(3) 某发动机右进气道螺栓在空中发生断裂,螺栓材料为30CrMnSiA,螺栓为重复使用件,表面进行电解除油和除去旧锌层后,进行表面电镀锌,镀锌完成后进行(190±10) ℃/4 h的除氢处理。螺栓断裂于第一扣螺纹根部,断口较平整,呈黑灰色,局部可见闪光小刻面特征。
对失效螺栓和同炉批二次镀锌的完好螺栓进行金相组织检查,结果表明,失效螺栓的组织为回火马氏体,而完好螺栓的组织为回火索氏体,如图4所示。对失效螺栓和同炉批二次镀锌的完好螺栓进行显微硬度检测,如表1所示。可见断裂螺栓的硬度和强度皆高于完好螺栓,并且抗拉强度高于规定要求(1080~1280 MPa)。同炉批螺栓中的氢含量较高,如表2所示。失效分析结果表明,螺栓发生氢脆断裂主要与螺栓材料强度偏高和氢含量较高有关。
图4 螺栓组织形貌对比
表1 螺栓硬度检测及强度换算结果
表2 同炉批螺栓的氢含量测试结果(wt%)
(4) 某飞机起落架螺桩安装一段时间后发生了断裂,断裂位于第一扣螺纹根部。螺桩材料为300M,表面经镀镉-钛处理。螺桩断口宏观形貌如图5(a)所示,分成两个区域:Ⅰ区断面粗糙、暗灰色,呈结晶颗粒状,约占断口总面积的1/3;Ⅱ区平坦、银灰色,占断口总面积的2/3左右。Ⅰ区的高倍形貌呈沿晶断裂特征,晶界面并不光滑,而是布满了细小条状的撕裂棱线,局部可见“鸡爪状”形貌,如图5(b)所示。Ⅱ区为瞬断区,呈韧窝断裂特征。
图5 螺桩断口形貌
对断口Ⅰ区由边缘向内部依次进行能谱成分分析,在沿晶区未发现镉元素,沿晶裂纹的产生与镉脆无关。由螺桩断口的微观特征可知,螺桩的断裂性质为氢脆断裂。由所测螺桩的硬度换算出抗拉强度为1892 MPa,符合技术规定σb=(1960±100) MPa的要求。
对失效螺桩、与失效螺桩同批电镀的一件无机械损伤的螺桩、新制无机械损伤的螺桩以及原材料进行氢含量测试,结果如表3所示。可以看出,失效件氢含量高于与失效螺桩同批电镀的无机械损伤的螺桩,略高于原材料的氢含量;而且,除失效件外,与失效螺桩同批次螺桩及新制螺桩的氢含量均低于原材料,由此表明,失效螺桩氢含量偏高与电镀及除氢工艺无关,而与机械损伤有直接关系。因此,表面机械损伤是导致螺桩氢脆断裂的主要原因。
表3 螺桩氢含量测试结果(wt%)
氢脆控制措施
1 电镀件驱氢
由于电镀过程渗氢造成的氢脆问题不可避免,所以对于氢脆敏感的高强度紧固件,需对其过程工艺包含电镀过程进行严格控制,以最大程度降低氢脆发生的风险。
高强度紧固件在电镀后2 h内需及时进行驱氢处理。根据材质及镀层的不同,驱氢工艺也不同,例如:普通电镀锌的低碳合金钢紧固件的驱氢烘烤温度为190~210 ℃,烘烤时长为 4~24 h。其目的是通过加强氢原子的热运动,使聚集于材料表面的氢原子从工件表面逸出或在内部扩散,降低局部浓度,减轻氢原子的聚集,以防止氢脆断裂。
需要注意的是,驱氢处理并不能使氢原子全部逸出工件表面,氢原子向金属内部扩散需要的能量比较小,而向外扩散要克服表面能和金属镀层的阻碍,所以逸出表面的氢原子只是一部分,驱氢只能减轻而不能彻底消除氢脆风险。
另外,如果对氢脆敏感的高强度紧固件进行重复电镀,尽管每次电镀后都严格执行驱氢工艺,但氢原子在材料内部会逐渐累积,其氢脆的风险也会越来越高,所以具有氢脆倾向的高强度紧固件不允许多次电镀。
除了在电镀过程中减少接触氢的机会以及严格执行驱氢工艺之外,还可以通过选择无氢脆风险的涂覆表面处理方式,如机械镀锌、粉末渗锌及锌铝涂层等。
2 除油
除油过程是电镀中的重要环节,必须预防以下问题:抗拉强度大于1200 MPa的工件,不允许采用化学阴极除油和阴阳极交替除油,宜采用阳极除油;对于高强度紧固件,宜采用较大电流密度下短时间除油,因为消耗相同电流时,电流密度越高,金属的渗氢越小。
3 酸洗
为去除紧固件表面氧化皮进行酸洗时,应尽量采用稀释的盐酸并加入缓蚀剂和表面活性剂,严禁用强酸洗,同时可采用喷砂、喷丸及液体喷砂等机械手段代替酸洗。
高强度紧固件材料在酸洗过程中应注意预防以下几点:对于弹性紧固件一般不进行强酸洗;对于抗拉强度大于1200 MPa的工件不允许用强酸洗,其表面的氧化皮采用喷砂或喷丸处理;对于抗拉强度在1000 MPa以上的螺纹紧固件,在表面无氧化膜的情况下,酸洗时间尽量减少,控制在1~3 min。酸洗所用酸的浓度不宜太高,在3%~5%之间为佳。
4 热处理
在连续式网带炉加热时,在保证炉内有足够的保护气氛,碳势在0.33%~0.4%的前提下,尽量减少载气富化气的供给量,使炉内氢的浓度降低,也就使工件中氢的渗人量减少。
适当降低淬火加热温度。由于氢在金属中的溶解度与温度有关,所以降低温度,可减少螺栓的吸氢量,对35CrMo,40Cr,42CrMo钢淬火或复碳工艺,加热温度一律控制在850 ℃(淬火)~870 ℃(复碳)。
在保证螺纹紧固件达到各项力学性能指标的基础上(尤其把强度和保证应力控制在合格范围内),要对工件的硬度控制在中间差范围,尽量不要在硬度值上限。
结论与展望
高强度风电紧固件氢脆断裂是一个比较复杂的问题,针对当前的研究现状,为推动将来紧固件向高强度的方向发展,提出以下建议及展望:
(1) 目前高强度风电紧固件发生氢脆断裂前缺少检测、监测手段,完善紧固件氢脆风险的评价方法和评价体系,以便及时获得准确的判断和信息反馈。深入紧固件氢脆机理研究,完善紧固件氢脆问题的标准体系建设。
(2) 高强度紧固件氢脆控制研究相对薄弱,尤其对紧固件制造过程的氢脆问题缺乏切实有效的控制手段,因此,亟需制定相应的生产工艺规范和管理措施控制氢脆现象发生。如对紧固件制造过程中热处理、酸洗、电镀等工艺进行优化研究,减少氢对紧固件的危害。
(3) 开发适用于风电紧固件且无氢脆问题的高性能新材料,如复合材料紧固件等。
免责声明:本网站所转载的文字、图片与视频资料版权归原创作者所有,如果涉及侵权,请第一时间联系本网删除。
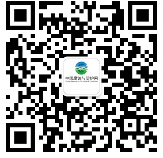
官方微信
《腐蚀与防护网电子期刊》征订启事
- 投稿联系:编辑部
- 电话:010-62316606
- 邮箱:fsfhzy666@163.com
- 腐蚀与防护网官方QQ群:140808414