分析讨论
1号弯管
C元素作为一种强化元素,可以提高碳钢的强度和硬度,从而提高耐磨损、耐冲刷腐蚀的能力。1号弯管中C元素含量偏低,使得其硬度降低,耐磨性下降,耐冲刷腐蚀的能力下降。1号弯管处于高压疏水管线,内部流速较高,与流体接触的表面在高速流体的作用下,表面材料不断被冲蚀掉,导致管道减薄。由于表面材料不断损失,故氧化膜不易留存,因而也起不到保护基体的作用。
另外,钢中的S是有害元素,会与Mn元素形成MnS塑性非金属夹杂物,影响钢的抗氢致裂纹(HIC)和抗硫致应力开裂(SSC)性能。但无论是金相分析还是微观形貌分析,都未观察到其对壁厚减薄的直接影响。
通过上述分析认为,1号弯管内的高速流体导致管道受到冲刷作用,发生壁厚减薄,属于冲刷腐蚀。若在其上游设置节流孔板,将增加管道中的流动阻力,降低流体的压力,起到保护管道的作用,避免管道发生因冲刷腐蚀导致的减薄。
2号弯管
2号弯管表面氧化膜是三类样品中最厚的,且基体无可见的形变特征和机械作用导致的材料损失,说明氧化膜隔离了流体对基体的直接作用。从工况条件分析,2号弯管位于给水系统的旁路,内部流速缓慢,不足以对管道材料产生冲刷作用。但流动的介质加速了氧化膜的溶解和氧通过氧化膜向基体的扩散,导致氧化膜在溶解的同时也不断生长,最终使管壁减薄,符合流动加速腐蚀的过程。另外,2号弯管微观形貌呈鱼鳞状,也属于典型的流动加速腐蚀形貌。
尽管2号弯管中的S元素含量也偏高,但分析中同样未观察到其对壁厚减薄的直接影响。
通过上述分析认为,2号弯管发生壁厚减薄的特征表现为氧化膜的加速溶解和生长,属于流动加速腐蚀。根据目前对流动加速腐蚀的认识,更换碳钢材料,使用Cr含量高于1%的低合金钢是较有效的途径。对于正在使用的碳钢管道,应加强管道壁厚的监测。
1、2号弯管虽然同属于弯管,但内部流速差异很大,因此发生壁厚减薄的机理完全不同,处理方式也截然不同,在工程实际中应注意区别。
3号孔板
与1号弯管相比,3号节流孔板下游的弯管并未发生明显的壁厚减薄现象,说明节流孔板的存在确实可以降低流速、降低流体压力,从而避免管道发生因高速流体导致的冲蚀减薄。但是3号孔板自身出现了减薄穿孔,在损伤表面观察到的大量细微韧窝,说明材料表面的各细微局部均分别受到了外力的作用。
分析其工况认为,外力的来源与流体经过孔板时产生的气泡有关:流体经过孔板时压力下降,低于流体的饱和蒸汽压力,于是产生气泡,即闪蒸;当下游流体的压力回升,气泡发生溃灭,对材料局部造成巨大冲击,即汽蚀。从材料已发生的微区塑性变形来看,其原因主要为汽蚀。
综上,尽管3号孔板有效抑制了下游弯管的冲刷腐蚀,但该节流孔板的结构形式导致流体通过时对孔板材料产生了汽蚀作用,导致孔板壁厚减薄并穿孔。因此应优化节流孔板的设计或者使用多级节流孔板。
结束语
经过上述分析,得出以下结论。
(1)1号弯管内的高速流体导致了冲刷腐蚀,造成管壁减薄。解决措施为:①在管道适当位置安装一定的分流系统来分担流量,或增大管径,降低管道中的流速。②提高管道中Cr元素含量,使用更加耐冲刷腐蚀的低合金钢或不锈钢。③减少弯管的使用或增大弯管的曲率半径,缓解由于流体方向改变而造成的扰流程度。
(2)2号弯管内发生的是以氧化膜加速溶解和生长为特征的流动加速腐蚀。解决措施为:①提高钢管中的Cr元素含量或更换耐流动加速腐蚀的材料(如不锈钢)。②控制氧浓度在合理的范围内(主要通过控制加入联氨的量),控制腐蚀发生的环境。③加强对流动加速腐蚀敏感区域的壁厚测量力度。
(3)流体经过节流孔板时产生气泡溃灭导致对材料的汽蚀是3号孔板壁厚减薄、穿孔的原因。解决措施为:①根据具体的使用工况(如系统的流量、流速等)重新设计孔板,如孔径、孔板厚度等。②设计多级孔板,通过多次降压,避免汽蚀的发生。
免责声明:本网站所转载的文字、图片与视频资料版权归原创作者所有,如果涉及侵权,请第一时间联系本网删除。
-
标签: 核电站原因碳钢管道壁厚减薄
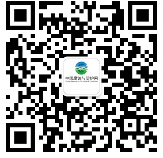
官方微信
《腐蚀与防护网电子期刊》征订启事
- 投稿联系:编辑部
- 电话:010-62316606-806
- 邮箱:fsfhzy666@163.com
- 腐蚀与防护网官方QQ群:140808414