1 引言
近年来,汽车消费者和生产企业对汽车腐蚀问题日益重视。车身腐蚀不仅有碍汽车美观性,而且会导致强度下降,影响到行车的安全性。车身防腐性能提升的途径主要有:一使用耐腐蚀性能好的车身板材,如镀锌板等;二增加防腐辅助工艺,如空腔注蜡、喷蜡等。三优化电泳结构设计,保证车身电泳涂层厚度,使之具有充分的耐腐蚀能力。其中第三者在车身防腐过程中充当着十分重要的角色,是防止车身发生由内至外腐蚀的主要手段。作为车身设计部门的工程师,第三者也是关注的重点。
车身的内腔具有复杂的结构,往往也是电泳涂层厚度不足问题的高发区域。工程上为了检验车身电泳后内腔的漆膜厚度,以评估电泳结构设计的可行性,采用的方法一般是通过试制样车,电泳烘干后进行切割解剖,然后使用测厚仪器进行人工逐点测量、记录。当发现风险区域,发生结构更改,再次验证时仍需重复试制-电泳-割车-测量步骤。这种“试制-纠错”的模式耗费了大量的人力、物力,并且时间周期长,不利于产品开发的快速迭代。近年来电泳虚拟仿真技术的发展使得在设计阶段就同步验证车身电泳涂层厚度成为了可能,这一技术的应用有效减少了实车试制、切割次数,解放了人的重复劳动,节约了开发的成本,缩短了验证的周期。
2 基于仿真技术的车身电泳涂层验证及优化
2.1 电泳涂层的仿真技术目前各汽车企业采用的大多是阴极电泳工艺,高分子带电微粒在电场的作用下向阴极运动并沉积在车身表面形成电泳漆膜。电泳仿真是通过数值计算的方法,基于法拉第电沉积理论实现电泳膜厚模拟的。
2.1.1电泳涂层计算原理电泳过程伴随流体运动、能量转换、能量传输、电场作用等一系列动态变化的过程,很难通过直接观测的方法得到电泳工艺的准确行为特征,而数值分析可基于一定的数学模型得到完整的流场、电场及化学特性参数信息。
车身电泳过程中,涂料粒子在电流的作用下运动,在阴极表面沉积成膜,而电泳涂膜本身是存在电阻的,漆膜厚度增长,涂膜电阻也随之增大,当电阻达到一定值后,膜厚便不再增加。在对车身电泳的仿真中,电流分布的计算在每个时间步可以看作是一个准稳态问题。仿真计算原理如下。
初始时刻,即车身进入电泳槽瞬间,时间为0,膜厚为0,槽液中电压为电极电压:
通过有限元法计算得到整个车身的电场分布状态,进而可以得到初始时刻车身表面各处的电流密度:
其中Rs表示电阻。
由法拉第定律推导的电泳涂膜厚度理论计算式可知,时刻的电泳涂膜厚度可由时刻的电流密度和涂料化学物理特性决定,即:
其中,涂料的化学物理参数通过涂料参数标定实验获得。
ti+1时刻的电阻受ti时刻的涂膜厚度影响:
进而可以得到ti+1时刻车身表面各处的电流密度:
重新计算电场分布,进行下一轮迭代,直到电泳结束。
2.1.2电泳仿真过程ECoatMaster 是一款能实现整车宏观分析和局部分析的电泳仿真软件,目前在多家汽车企业得到应用,功能强大,界面友好。
运用ECoatMaster软件电泳仿真分析首要任务是建立常用参数,即涂料参数、电泳槽模型、工艺参数,接着输入车体的3D数据,划分网格,设置边界条件,搭建有限元模型,最后提交计算,得出分析结果。
1)涂料参数测试。
对于车身电泳膜厚,准确的计算及模拟必须以实验为基础,受到电泳涂料化学物理特性的影响,阴极电泳沉积效率一般低于100%。为得到实际电泳沉积效率,获得用于电泳仿真分析的沉积参数,首先进行了福特盒实验以确定电泳漆的基本泳透能力,然后以车身材料圆片试样为实验对象进行了简化模型的电泳实验,以获得实际电泳涂料沉积相关参数并用于车身电泳膜厚仿真计算。
实验参数标定方法见图1。首先搭建电泳实验平台进行实验,记录实验过程中膜厚及电流;然后设定初始沉积参数集,建立实验仿真模型,将仿真结果与实验结果比较,若吻合度满足要求,则参数标定合格。否则,修改沉积参数,进一步仿真计算,反复迭代,直到仿真结果与试验结果吻合良好。
电泳试验操作平台如图2所示。
2)电泳槽模型,如图3所示。
包括电泳槽几何尺寸、电极截面形状、电极尺寸、电极安装位置及数量。
3)工艺参数。
主要包括:电泳有效时间、车身输送轨迹、电泳电压程式等。
4)网格划分及边界条件设置。
对整车模型自动划分网格,设置边界条件,搭建有限元模型。
5)提交计算。
先进行整车宏观运算,然后在宏观计算结果基础上截取关注区域进行局部精算。
6)后处理。
将计算结果导入XPlorer软件中,进行可视化处理,获得车身表面电泳膜厚分布云图,拾取关键点获得电泳膜厚精确数值。
2.2 车身电泳结构
优化流程车身结构设计是一个多次迭代开发的过程,常常伴随多次结构更改及优化才能锁定最终的数模数据。对车身进行防腐性能开发,进行电泳结构优化时,必须兼顾车身强度、刚度等其他性能要求,将电泳同步分析融入车身开发流程体系当中,图4为车身开发过程中电泳结构优化流程。
电泳同步工程分析的合理介入,在设计阶段就能对方案进行可行性评估,减少了实车验证的次数,加快了车身开发迭代的速度,极大节约成本和缩短验证周期,同时提升了产品质量。
3 某车型大梁电泳涂层验证及优化
实例3.1 某车型大梁电泳仿真实例分析
大梁内腔结构复杂,钣金间隙小,电泳液流动不畅,局部腔体电泳液甚至无法进入,或腔体形成电磁屏蔽,电场强度很弱,导致内表面电泳漆膜厚度薄。再加上大梁位于车身底部,工作环境潮湿,容易受到泥水侵蚀。薄弱的电泳涂层无法抵御腐蚀的发生,使大梁内腔成为腐蚀的高发区。图5为某车型大梁,实车观测生锈主要发生在大梁中段。
在整车宏观计算的基础上截取大梁区域进行电泳仿真精算,仿真结果如图6所示。
从分析结果看,大梁中段加强板下表面电泳漆膜厚度为0.01~3.86μm,电泳涂层未达到膜厚要求,不足以抵御腐蚀的发生。仿真结果预示生锈区域与实车生锈观测结果吻合一致,说明了电泳仿真模型的正确性。
3.2 某车型大梁电泳结构优化电泳仿真结果为设计人员指明了结构缺陷,明确了结构更改的区域范围。对仿真结果进行进一步工程分析可发现:存在问题区域电场强度较弱,不足以保证充分的涂料电沉积作用;电泳工艺孔距离过大,内腔电泳液流动不充分;电泳时排气受阻,易产生气泡。上述因素导致了电泳上漆困难。
为此,提出针对性的更改措施,对结构进行优化:加强板侧面增加筋条,保证与大梁侧面离空5mm,形成5x10mm通道,同时增加一φ20mm电泳孔,确保电泳过程中液体流动通畅;在加强板底部增加5个φ16mm排气孔,消除气泡的影响,同时有利于消除电磁屏蔽,保证电泳充分。优化后大梁加强板结构如图7所示。
泳膜厚为3.51~11.8μm,相比原结构膜厚有所提升,但仍存在小块面积漆膜厚度偏薄,未能满足防腐要求。
对结构进行深入分析发现,虽然大梁加强板增加了电泳工艺孔,但大梁底部未开孔仍形成封闭结构,因此第二次结构优化在大梁底部增加3个φ16进液孔,大梁侧面增加2个φ16错位孔,保证电泳液顺畅进出大梁内腔,如图9所示。
第二次优化后仿真结果如图10所示。大梁加强板电泳漆膜厚度为8.93~14.44μm,漆膜厚度到达了防腐目标要求。
优化后结构经评估同时满足车身强度、刚度等其他性能要求。数模锁定后,进行实车试制验证,在加强板上选取10个测量点,使用漆膜测厚仪测量膜厚,仿真结果与实测结果如图11所示,数据吻合性较好。
经过工程分析,提出优化方案,先经仿真验证,最后实车验证,漆膜厚度达到设计要求。说明改进措施有效,可以实施,确保大梁内腔区域防腐蚀性能良好,提高了使用寿命。
4 总结
本文主要介绍了在设计阶段引入电泳仿真技术进行同步分析的一种新的电泳涂层验证手段。实践证明这种手段是卓有成效的。利用电泳仿真同步分析技术,能在设计阶段就暴露出电泳结构设计缺陷,为结构优化指明方向;通过电泳仿真手段对结构更改的可行性进行验证,能够减少传统模式“试制-割车”次数,从而减少人力、物力耗费,节约开发成本;同时能够缩短验证的周期,加快产品开发迭代速度,并能保证产品的质量,为企业赢得竞争力。
更多关于材料方面、材料腐蚀控制、材料科普等方面的国内外最新动态,我们网站会不断更新。希望大家一直关注中国腐蚀与防护网http://www.ecorr.org
责任编辑:王元
投稿联系:编辑部
电话:010-62313558-806
中国腐蚀与防护网官方 QQ群:140808414
免责声明:本网站所转载的文字、图片与视频资料版权归原创作者所有,如果涉及侵权,请第一时间联系本网删除。
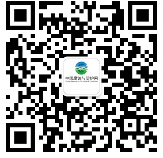
官方微信
《中国腐蚀与防护网电子期刊》征订启事
- 投稿联系:编辑部
- 电话:010-62316606-806
- 邮箱:fsfhzy666@163.com
- 中国腐蚀与防护网官方QQ群:140808414