钛合金因其优异的机械性能、良好的生物相容性和优异的耐腐蚀性能而成为航空、航天、生物以及航海工业中不可或缺的结构材料。 钛合金表面在大气或者海水中会立即生成1 层保护膜,使之处于钝化状态。 在常温海水环境中不发生点蚀和缝隙腐蚀,是目前已知的抗常温海洋环境腐蚀最优异的金属材料。 虽然钛合金表面易钝化而防腐,但是在中等载荷和转速下很容易被擦伤从而导致钝化膜的破坏,加剧腐蚀。 在海水环境中对于摩擦学的研究具有重要的意义,对于海洋设备的开发和利用,尤其是能为海水液压传动系统提供技术指导和理论依据。 海水液压传动系统以海水作为工作介质,具有环境相容性,其广泛应用于水下机器人、深海设备、海上采油平台等领域。 当腐蚀和摩擦共同作用于金属时,机械和电化学因素的共同作用会产生复杂的反应并促进其失效。 腐蚀磨损一般是指发生在腐蚀介质中的磨损现象,是力学因素、化学因素以及电化学因素及其交互作用的结果。
研究腐蚀磨损交互作用需要测量电化学腐蚀作用和摩擦作用各自的速度,由于它们是同时发生于同一个腐蚀磨损体系中,因此难以用传统的失重法同时分别地测出材料的磨损和电化学腐蚀速度。 为此研制了1 种电化学腐蚀磨损装置,对腐蚀磨损体系进行电化学控制和监测,提出了1 种研究电化学腐蚀和机械磨损相互作用的分析方法,对TC4 钛合金在海水环境下的电化学腐蚀以及耐腐蚀磨损性能进行了研究。
1 实验部分
1. 1 试验设备
在国产MMW - 1 型立式万能摩擦磨损试验机上进行TC4 钛合金的腐蚀磨损试验,采用销- 盘滑动接触方式,由于要对TC4 钛合金的电位和电流进行监控,对该试验机进行了部分改装,将电化学工作站引入腐蚀磨损体系,图1 为改装后的腐蚀磨损试验机工作原理示意图。 其工作过程为: 圆柱形陶瓷销试样安装在主轴上并随轴转动; 环形下试样固定不动,并始终浸泡于海水之中,环试样只有上表面接触海水,其余表面密封。 在腐蚀磨损过程中,钛合金下试样作为工作电极,其腐蚀电化学信号输出至带有电脑测控的CHI760C 型电化学恒电位仪,在试验槽内安装Pt 辅助电极和鲁金毛细管,鲁金毛细管通过盐桥连接至饱和甘汞参比电极( SCE) ,组成三电极系统,从而可进行相应的电化学测量和监控。 在试验中均以下试样作为研究对象,测定其在不同试验条件下的腐蚀磨损性能。
1. 2 腐蚀磨损定量测试
在腐蚀磨损过程中,材料的破坏包括材料因素、电化学因素、力学因素和环境因素的共同作用。 在腐蚀介质中,电化学因素和力学因素对材料产生明显地腐蚀磨损交互作用。 一般来说材料的总磨损量VT大于纯腐蚀量Vc与纯磨损量Vm之和,其增加量可称为腐蚀磨损交互作用量ΔV:
而腐蚀磨损交互作用量ΔV 又可分为两部分:
腐蚀对磨损的促进量Vcm以及磨损对腐蚀的促进量Vmc,即:
1. 2. 1 VT的测定
采用精度为0. 1 mg 的电子天平准确称量在开路电位条件下的腐蚀磨损试验前后TC4 钛合金试样的失重,进而得到TC4 钛合金的体积损失量。
1. 2. 2 Vm的测定
采用阴极保护法测定TC4 钛合金的纯磨损量,阴极保护电位为- 1 000 mV(SCE) ,此时腐蚀作用被抑制,材料的损失可以看作单纯机械磨损失重,进而得到TC4 钛合金的体积损失量。
1. 2. 3 Vc与Vmc的测定
采用电化学方法来测定TC4 钛合金在静态腐蚀条件下以及摩擦过程中的腐蚀电流密度。 按照美国材料与试验协会制定的研究腐蚀和磨损交互作用的标准ASTM G1119 - 04[13],根据实测塔菲尔极化曲线求得极化电站Rp以及阴极和阳极的极化率ba和bc,通过公式(4) 计算腐蚀电流密度:
然后通过法拉第公式可以将腐蚀电流密度转化为腐蚀作用所产生的体积损失量Vc与Vmc,公式如下:
其中t 为腐蚀磨损的持续时间,F 是法拉第常数( 96 500 C /mol) ,ρ 是TC4钛合金的密度,M 是钛合金的原子量,n 为TC4 钛元素的化合价。 腐蚀对磨损的促进量Vcm不能直接测量出来,但是可以通过公式( 3) 计算得出。
1. 3 试验条件
本试验的研究材料为TC4 钛合金,其化学成份( 质量分数计) 为6. 25% Al,4. 21% V,0. 22% Fe,0. 19%O,0. 0073%H,Ti 余量。 TC4 钛合金加工为环形试样,其尺寸为外径52 mm,内径38 mm,高度10 mm,其暴露在海水中的面积为11. 5 cm2 . 为了避免在试验过程中异种金属接触可能产生的电位干扰以及电偶腐蚀,对偶材料选用不导电的氧化铝陶瓷( 硬度为HV 1800) ,氧化铝试样为圆柱形,其尺寸为4. 8 m × 13 m. 试验中的腐蚀溶液为按照ASTMG1148 - 98 标准配置的人工海水,配置海水的pH 值用0. 1 mol /L 的NaOH 溶液调节至8. 2.铝陶瓷对摩在不同载荷,转速固定为100 r /min[图2( a) ]和不同转速,载荷固定为50 N[图2( b) ]时的开路电位- 时间以及摩擦系数- 时间曲线。 由图2 可以看出: 未摩擦时,钛合金的电位稳定在- 0. 22 V附近,摩擦刚一启动,TC4 钛合金的开路电位急剧下降; 摩擦过程中,开路电位保持在低值并且有一定的波动; 当摩擦结束时,开路电位开始升高。
在摩擦过程中,TC4 钛合金的开路电位随着载荷和转速的升高而明显降低。 在载荷固定为50 N 时,TC4 钛合金的摩擦系数随着转速的升高而缓慢增加; 在转速固定为100 r /min 时,载荷不超过100 N时摩擦系数基本上不随载荷的变化而变化,而当超过100 N 时,摩擦系数随着载荷的升高明显增加。
TC4 钛合金在海水中具有优异的耐腐蚀性能是由于其表面存在致密的TiO2钝化膜,但当上下试样腐蚀磨损试验在开路电位条件下进行,并且测量了其摩擦过程中的开路电位变化。 为了表征摩擦作用对TC4 钛合金腐蚀速度的影响,测量了静态腐蚀以及摩擦过程中的极化曲线,扫描范围为- 1 ~1 V,扫描速率为10 mV/s,并用公式( 4) 计算其腐蚀速度。 对TC4 钛合金在阴极保护条件下的磨损量进行了测量,其保护电位为- 1 000 mV( SCE) . 每次试验前后将下试样清洗干净,烘干并称重,取3 次试验失重数据的平均值换算为体积磨损量,并用JSM -5600LV 型扫描电子显微镜( SEM) 观察钛合金试样的磨痕表面形貌。
2 结果与讨论
2. 1 开路电位测量
图2所示为在海水环境下,TC4 钛合金与氧化产生摩擦时,表面的钝化膜受到连续的破坏,新鲜表面的产生促进了钛合金的腐蚀,从而导致开路电位急剧下降,摩擦过程中的电位变化实际上是TC4 钛合金钝化膜破坏- 修复的动态平衡过程的结果。 电位的下降是由于阳极区域流过的电流和阴极区域流过的电流要在某一电位位置达到平衡。 在同一载荷下,转速的增加能够导致上下试样滑动接触时间间隔的缩短,从而减少了钝化膜修复的时间,表面钝化膜的破坏严重,所以转速的增加使得开路电位下降的幅度增大。 在同一转速下,随着载荷的增加导致上下试样接触面塑性变形变得严重,从而增加了钝化膜破坏的程度,所以载荷的增加同样使得开路电位下降的幅度增大。
2. 2 极化曲线测量
在海水环境下,TC4 钛合金在静态以及摩擦过程中( 100 N,200 r /min) 的极化曲线如图3 所示。 从图3 中可以看出: 摩擦作用使得TC4 钛合金的自腐蚀电位负移,腐蚀倾向加大。 在静态以及摩擦过程中TC4 钛合金均具有明显的钝化现象,表明TC4 钛合金在海水下钝化能力极强,在磨损过程中由于钝化膜的破坏而产生的新鲜表面能迅速复原。 摩擦作用明显增加了钛合金的腐蚀电流密度,摩擦对腐蚀的促进作用非常显着。 通过公式( 4) 对静态以及摩擦过程中的极化曲线处理求得的腐蚀电流密度icorr以及腐蚀电位Ecorr如表1 所示。 由表1 可知静态腐蚀中TC4 钛合金的电流密度仅为2. 97 μA/cm2,表明静态下TC4 钛合金具有优异的耐腐蚀性能,而在摩擦过程中TC4 钛合金的腐蚀电流密度为2. 44 ~3. 17 mA/cm2 ,提高了3个数量级,并且随着摩擦作用的增强( 载荷和转速的增加) ,腐蚀电流密度缓慢增加。 这表明摩擦作用明显提高了TC4 钛合金的腐蚀速度,腐蚀磨损之间存在明显的交互作用。
2. 3 腐蚀磨损交互作用
通过上述相对应的试验方法得到腐蚀磨损过程中VT、Vc、Vcm以及Vmc的结果,然后根据定量计算公式,计算出腐蚀磨损过程中的各个组份分量,进而得出各分量所占的比例,由于TC4 钛合金在海水中静态下的腐蚀速度非常小,Vc可以忽略不计,数据分析结果见表2. 从表2 中可以看出,腐蚀磨损交互作用量占总腐蚀磨损量的比例ΔV /V 为10. 2% ~34. 1%,这说明在本试验工况条件下TC4 钛合金的损耗10. 2% ~ 34. 1% 是由于海水的腐蚀磨损交互作用造成的,从而表明在海水环境下TC4 钛合金的腐蚀与磨损的交互作用不可忽视。 纯磨损量占总腐蚀磨损量的比例为65. 9% ~ 89. 8%,这说明在腐蚀磨损过程中磨损作用明显大于腐蚀作用,表明力学因素是造成腐蚀磨损失重的主要因素。 另外,随着摩擦作用的增强( 载荷和转速的增加) ,交互作用量减小,这表明腐蚀磨损交互作用在低载荷低转速下尤其明显。
图4 显示了腐蚀磨损过程中各分量组成部分以及所占的比例。 从图4 中可以看出: 虽然摩擦极大地提高了TC4 钛合金的腐蚀速度,但是摩擦对腐蚀的促进作用Vmc占总腐蚀磨损的比例Vmc /V 仅有3. 1% ~ 12. 2%,并且随着摩擦作用的增强而减小。腐蚀对磨损同样产生了明显地促进作用,其促进量占总腐蚀磨损的比例Vcm /V 为7. 1% ~ 21. 9%,这说明腐蚀介质促进了TC4 钛合金的脱落,同样Vcm /V随着摩擦作用的增强而减小。
磨损对腐蚀的促进作用可以归结为: 摩擦作用使得TC4 钛合金表面产生塑性变形,并导致局部变形区域位错、空位、晶面等缺陷的密度急剧增大,残留内应力聚集,该区域具有高的腐蚀活性,形成微观“应变差异电池”,同时摩擦过程中的搅拌作用促进了阴极反应过程,促进腐蚀的进行,在摩擦表面产生了局部小孔腐蚀,使得摩擦过程中的腐蚀电流急剧增大。 图5( a) 中清晰可见TC4 钛合金磨痕表面的腐蚀坑。 腐蚀对磨损的促进作用归结如下: 腐蚀磨损过程中磨屑的产生可视为低周疲劳脱落过程,疲劳过程导致磨痕表面形成裂纹[图5( b) ],裂纹尖端附近的位错和空位等缺陷导致裂纹处具有高的腐蚀活性,海水的腐蚀作用加速了裂纹的扩展和繁殖,从而加速了钛合金磨屑的脱落。
3 结论
a. 在人工海水中TC4 钛合金腐蚀磨损时开路电位降低,腐蚀电流密度大幅增加。
b. 在本试验工况条件下,腐蚀磨损交互作用量占总腐蚀磨损量的比例ΔV /V 为10. 2% ~34. 1%,腐蚀磨损交互作用不可忽视。
c. 摩擦对腐蚀的促进作用Vmc占总腐蚀磨损的比例Vmc /V 仅有3. 1% ~ 12. 2%,并且随着摩擦作用的增强而减小。 腐蚀对磨损也产生了明显地促进作用,其促进量占总腐蚀磨损量的比例Vcm /V 为7. 1% ~ 21. 9%,同样随着摩擦作用的增强而减小。
更多关于材料方面、材料腐蚀控制、材料科普等方面的国内外最新动态,我们网站会不断更新。希望大家一直关注中国腐蚀与防护网http://www.ecorr.org
责任编辑:王元
《中国腐蚀与防护网电子期刊》征订启事
投稿联系:编辑部
电话:010-62313558-806
邮箱:fsfhzy666@163.com
中国腐蚀与防护网官方 QQ群:140808414
免责声明:本网站所转载的文字、图片与视频资料版权归原创作者所有,如果涉及侵权,请第一时间联系本网删除。
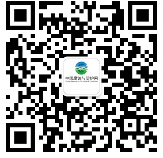
官方微信
《中国腐蚀与防护网电子期刊》征订启事
- 投稿联系:编辑部
- 电话:010-62313558-806
- 邮箱:fsfhzy666@163.com
- 中国腐蚀与防护网官方QQ群:140808414