山东肥城段长输天然气螺旋缝埋弧焊钢管,尺寸为φ508mm×6.4mm,钢级L320,采用3PE防腐蚀工艺。全线设计压力3.9MPa,最大工作压力3.5MPa,实际运行3.0MPa,天然气瞬时流量417Nm3/h。管道投用4a后出现腐蚀穿孔,造成天然气泄漏事故。
本工作分析了管道腐蚀穿孔的原因,制定预防和控制腐蚀措施,以期防止管道进一步腐蚀穿孔,消除安全隐患。
理化检验
◆◆
1 基材性能
◆◆
基材取样位置为接近腐蚀穿孔的区域,依据GB/T 4336-2002《碳素钢和中低合金钢 火花源原子发射光谱分析方法(常规法)》,使用直读光谱仪检测材料的化学成分;从钢管管体和焊缝处取样,依据GB/T 228.1-2010《金属材料 拉伸试验》进行拉伸试验;从钢管管体、焊缝和热影响区分别取样,依据GB/T 2106-1980《金属夏比(V型缺口)冲击试验方法》进行夏比V型冲击试验。
试验结果表明:基材试样均符合GB/T 9711.1-1997《石油天然气工业—输送钢管交货技术条件 第1部分:A级钢管》标准要求,即腐蚀不是由基材缺陷造成的。
◆◆
2 天然气组分检测
◆◆
管道内输送的介质成分(体积分数/%)为:甲烷93.276%,乙烷3.631%,丙烷0.662%,异丁烷0.117%,正丁烷0.116%,异戊烷0.05%,正戊烷0.024%,C6+0.086%,二氧化碳1.428%,氮气0.61%。管道内输送的介质中含有N2和CO2,虽然CO2气体不具有腐蚀性,但一旦溶于水,对钢铁的腐蚀比强酸还要严重。
◆◆
3 腐蚀孔的宏观形貌
◆◆
观察腐蚀穿孔的管段,发现管段底部存在水,呈规则的带状分布,见图1,点蚀均发生在管段底部内壁。这表明,经过水压试验后,该管段底部长期存在积水。
图1 腐蚀孔位置图
由图2可见,腐蚀孔直径约5.6mm,腐蚀孔周围是直径为20mm的腐蚀坑,外壁光滑,表明腐蚀是由内壁开始的,直至腐蚀穿孔,造成天然气泄漏。
由图2还可见,腐蚀坑为圆形,腐蚀坑周围存在腐蚀产物,且腐蚀产物表面多孔,呈片状。这符合二氧化碳腐蚀产物特征:碳化物在表面形成多孔、海绵状、片状或针状结构,有利于FeCO3的沉积。
图2 腐蚀孔内壁形貌
与腐蚀孔相邻区域,发现有四个较大的腐蚀坑,分别用1号、2号、3号、4号表示,见图3。对管道剩余壁厚进行测量,结果表明,4号腐蚀坑处壁厚仅为2.15mm,存在腐蚀穿孔的危险。
图3 腐蚀坑形貌
◆◆
4 管材显微组织
◆◆
在管段腐蚀坑位置取样,进行金相检验,结果表明,失效管段的组织均为铁素体和珠光体,未见异常组织,见图4。腐蚀孔周边并未发现组织缺陷及裂纹。图4中,非金属夹杂物为圆形、黑色、分布不规则,根据GB/T 10561-2005《钢中非金属夹杂物的含量测定标准评级图显微检验法》,此非金属夹杂物为环状氧化物。其大小符合为D类细系1级,直径为3~8μM。根据金属材料断裂理论,如果非金属夹杂物的尺寸小于8μM,则不是裂纹源,因此,该环状氧化物不会产生腐蚀。
图4 腐蚀坑附近金相组织 100×
◆◆
5 腐蚀产物分析
◆◆
对腐蚀产物进行扫描电子显微镜(SEM)和能谱(EDS)分析,结果见图5和表1。可以看出,腐蚀产物为结晶状立方体形貌。EPS结果表明,该结晶体成分主要为Fe,C,O,其原子百分比约为1∶1∶3。根据SEM结果及EDS结果推断这种结晶状产物为FeCO3。
图5 腐蚀产物的SEM形貌
在管段内壁的腐蚀坑附近刮取腐蚀产物进行XRD衍射图谱分析,结果见表2。可以看出,内壁的腐蚀产物主要为FeCO3和铁的氧化物。
表1 腐蚀产物能谱分析结果
表2 腐蚀产物XRD分析结果
结果与讨论
综上所述,管道基材满足生产标准要求,显微组织无异常,腐蚀原因与基材关系不大。钢管底部的积水,推测是管道经过水压试验后,清管不净,留存在管道内的。管道输送介质中含有CO2,溶于水后,对钢管具有腐蚀性,会产生CO2腐蚀。腐蚀产物主要为FeCO3,铁的氧化物,可知腐蚀与氧腐蚀、CO2腐蚀都有关系。
◆◆
1 氧腐蚀
◆◆
管道底部长期积水,且管道敷设1a后才投入使用,管材底部与管道内积水和空气中的氧反应,生成了Fe(OH)2,进一步氧化后生成Fe(OH)3。水解生成的羟基氧化铁FeO(OH),经脱水和进一步氧化之后变成Fe2O3,与此同时也有少量的Fe(OH)2脱水生成FeO。
因此,在通常情况下Fe的氧腐蚀产物为FeCO3和FeO的混合物,即为Fe3O4。氧腐蚀为均匀腐蚀,形成了Fe3O4膜覆盖在母材金属表面,详见式(1)~(5)。
2Fe+2H2O+O2→2Fe(OH)2(1)
2Fe(OH)2+(1/2)O2+H2O→2Fe(OH)3(2)
2Fe(OH)3-2H2O→Fe2O3·H2O(3)
Fe(OH)3-H2O→FeO(OH)(4)
8FeO(OH)+Fe2++2e-→3Fe3O4+4H2O(5)
◆◆
2 CO2腐蚀
◆◆
管道投产后,管道底部仍然有积水存在,天然气中含有CO2,当CO2溶于水后,对钢铁具有极强的腐蚀性。腐蚀产物表面多孔,呈片状,符合CO2腐蚀产物特征,有利于FeCO3的沉积,表明腐蚀为CO2腐蚀。
XIA等认为,碳钢在CO2腐蚀时,产生FeCO3覆盖的区域与未覆盖的金属区域形成了电偶腐蚀,产生了点蚀,最终表现为局部腐蚀穿孔。
CO2腐蚀反应见式(6)~(10)
CO2+H2O→H2CO3(6)
H2CO3→H++HCO3-(7)
HCO3-→H++CO32-(8)
2H++Fe→Fe2++H2(9)
Fe2++CO32-→FeCO3(10)
其腐蚀总反应为见式(11)
CO2+H2O+Fe→FeCO3+H2(11)
◆◆
3 各因素对腐蚀的影响
◆◆
CO2水溶液的腐蚀性并不是由溶液pH决定,而是由溶液中CO2含量决定的。所以输送天然气压力越高,CO2溶解度越大,CO2含量越大,溶液腐蚀性越强。
研究表明,在相同的PH条件下,CO2水溶液的腐蚀性比HCl水溶液还要高。高流速增大了腐蚀介质到达金属表面的传质速率;且高流速阻碍和破坏了金属表面形成保护膜,也加速了金属钝化过程。因此,流速越大,材料的腐蚀速率越高。
此外,在低温阶段,CO2腐蚀速率随温度的升高而增大。
结论与建议
基材符合GB/T 9711.1-1997《石油天然气工业—输送钢管交货技术条件 第1部分:A级钢管》生产标准要求,腐蚀并非因基材缺陷造成的;管道建成后1a内未投用,由于管道底部存有水,上部为空气,空气中的氧进入水中,对管道底部形成了均匀的氧腐蚀;天然气中的CO2进入管道底部水中,对管道底部形成了CO2腐蚀,氧腐蚀与CO2腐蚀共同作用于管道底部,形成了管道底部的腐蚀坑与腐蚀孔。
针对腐蚀问题,建议采用如下措施以改善腐蚀问题:
(1)改变金属的使用环境,以降低环境对金属的腐蚀;
(2)使用缓蚀剂;
(3)外加电流与牺牲阳极保护;
(4)开展管道清管与内检测;
(5)通过控制管道运行压力、温度、流速,减少刚投产管道CO2腐蚀风险。
更多关于材料方面、材料腐蚀控制、材料科普等方面的国内外最新动态,我们网站会不断更新。希望大家一直关注中国腐蚀与防护网http://www.ecorr.org
责任编辑:王元
《中国腐蚀与防护网电子期刊》征订启事
投稿联系:编辑部
电话:010-62313558-806
邮箱:fsfhzy666@163.com
中国腐蚀与防护网官方 QQ群:140808414
免责声明:本网站所转载的文字、图片与视频资料版权归原创作者所有,如果涉及侵权,请第一时间联系本网删除。
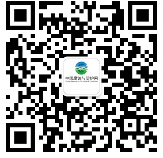
官方微信
《中国腐蚀与防护网电子期刊》征订启事
- 投稿联系:编辑部
- 电话:010-62313558-806
- 邮箱:fsfhzy666@163.com
- 中国腐蚀与防护网官方QQ群:140808414