镁合金由于其质轻高强的特性,在航天航空领域内广泛应用。低差压铸造作为一种反重力铸造工艺,可以减少铸件气孔、缩孔、缩松、针孔缺陷;提高铸件表面品质;差压铸造的补缩压力较大,补缩效果明显,降低疏松缺陷产生倾向,可同时降低铸件凝固时的热裂倾向,因此,低差压铸造得到了广泛的应用。随着大型镁合金壳体铸件在航天、航空领域应用不断扩大,为了获得高品质铸件,低(差)压铸造技术得到了广泛应用和发展。航天航空用ZM5、ZM6镁合金和稀土耐热镁合金壳体类铸件大多为I类铸件,需要100%进行X射线探伤,铸件内部质量要求较高。ZM5、ZM6合金壳体型芯一般采用粘土砂表干型,外型采用粘土砂湿型;稀土耐热镁合金壳体型芯采用树脂砂,外型采用粘土砂湿型,采用差(低)压铸造工艺生产,浇注的铸件经常会出现疏松、裂纹、偏析、气孔和熔剂夹渣等铸造缺陷……
本课题结合壳体铸件的生产特点,总结差(低)压铸造中经常遇到的铸造缺陷并提出相应的解决措施。
一 铸件分析
图1为壳体类零件三维图。材料为ZM5,尺寸为为Φ420 mm×700 mm,要进行100% X射线探伤,属I类铸件。铸件常见缺陷有疏松、偏析、裂纹、熔剂夹杂以及气孔缺陷。
图1:典型壳体类零件三维图
二 常见缺陷产生与防止
1、疏松的产生和防止
疏松是镁合金铸件出现的主要缺陷,分布面广,难于补缩。镁合金结晶温度区间较宽,凝固收缩率大,凝固时糊状凝固的倾向很大,常常导致液态收缩和凝固收缩所形成的微孔分散并且得不到外部合金的液体补充,形成疏松,有时候甚至由于凝固收缩时晶间拉应力过大而出现缩裂现象。
在镁合金壳体铸造中疏松主要出现在铸件厚、薄过渡区和缝隙浇道附近,以及冷铁与芯砂的交接处。通过对出现的缩松评级,普遍为4级缩松,有的甚至达到了严重的5级缩松。而铸件属于I类铸件,要求最高别只能是3级,必须严格控制疏松等级。
工艺设计
壳体铸件的工艺大多采用顺序凝固的原则,系统内由缝隙浇道、过渡浇道、横浇道到连接升液管口的直浇道顺序凝固,从而保证铸件补缩通道畅通,充分发挥差(低)压铸造的补缩优势[3]。图2为镁合金壳体铸件浇注系统。采用设置冷铁、石墨砂调节局部冷却速度,增设缝隙浇道和过渡浇道缩短补缩距离等措施。
图2:镁合金壳体浇注系统
图3为镁合金壳体铸件冷铁布置示意图。缝隙浇道前要设置冷铁,冷铁位置和厚度对减轻浇口前疏松尤为重要,缝隙浇道不仅要对准冷铁,错开冷铁间隙,而且要保证缝隙浇道两侧冷铁有足够的宽度,缝隙浇道前冷铁还要由厚到薄逐渐过渡,冷铁边缘用石墨砂过渡,石墨砂也要由厚到薄逐渐过渡。
图3:镁合金壳体冷铁布置示意图
在工艺设计时,在凸台部位一般都设置冷铁加强激冷以减小热节,但当凸台过厚时容易产生疏松缺陷,即使增加冷铁厚度也很难消除。在凸台部位设计补缩浇道增加补缩,可有效消除疏松缺陷。
浇注温度
降低浇注温度可减轻铸件过热,有利于降低疏松等级,但不是温度越低越好,温度过低会降低补缩效果。一般情况下,当浇注大直径立筒时可适当降低浇注温度,浇注小直径立筒时,浇注温度要适当提高。
浇注工艺
在保证铸型充满的前提下,充型速度一般选下限,既可以避免充型时产生紊流、飞溅造成卷气,又能延长金属液对浇道的烘烤时间,从而调整铸件凝固速度,强化顺序凝固效果。根据生产经验,升液速度要高于充型速度。
增加保压压力可以强化合金凝固期间补缩能力,从而填充枝晶间的微缩孔,但压力过大会导致铸件变形、粘砂和跑火等,因此压力也不是越大越好,一般保压压力为30kPa~60kPa。
2、偏析的产生和防止
镁合金的偏析一般是成分偏析,常会导致铸件直接报废。合金熔炼工艺和铸件凝固条件都会引起铸件产生偏析缺陷。通过调整精炼温度、改善激冷能力以及降低浇注温度,可有效降低偏析缺陷产生倾向。
精炼温度
镁合金熔炼过程中,相对镁合金熔点高的其他金属是重金属。重金属元素偏析的现象是由于重金属元素未能完全融入合金液中,提高精炼温度,重金属元素能够更好地熔入合金液中,铸件中重金属元素的偏析现象明显减少。
激冷能力及浇注温度
成分偏析易产生于厚壁冷铁间隙处和厚壁间的薄壁处,在这些部位放置石墨砂加强激冷,减轻局部过热可有效防止偏析缺陷的产生。
降低浇注温度,缩短合金凝固时间,降低合金过冷度,防止重金属在凝固过程中析出,减轻了偏析的产生。在耐热镁合金壳体的生产中,降低浇注温度,偏析缺陷得到了极大改善。
3、裂纹的产生和防止
裂纹是铸件致命的铸造缺陷,在铸件上呈现直的或者曲折的隙缝与裂口,断面处被氧化呈黑色或者深灰色,易产生在凸台的厚薄交接处和下端框处,工艺设计、原材料质量和冷铁位置都会导致裂纹缺陷。
工艺设计
当铸件设计多个相邻较近的凸台时,见图4,在凸台间的薄壁处易产生裂纹缺陷。通过设计合理的防裂拉筋,可有效消除裂纹缺陷。
图4:裂纹产生处
控制原材料质量
由金属的遗传性可知,原料镁锭的成分决定了铸件的质量。镁锭的一系列缺陷,在铸造后能遗传给浇注后的铸件。当原生镁锭有裂纹缺陷时,浇注的铸件会产生批次性裂纹缺陷,因此加强对原生镁锭裂纹缺陷的控制可有效消除批次性裂纹缺陷的产生。
冷铁位置
稀土耐热镁合金收缩大,凝固时受阻碍极易产生裂纹缺陷,裂纹一旦产生就会发展并贯穿到底,是一种致命缺陷,因此,造型时冷铁间隙要足够大,否则会阻碍合金的收缩而产生裂纹。一般冷铁间隙不小于5 mm,圆弧面冷铁要向心,防止后部相抵住。
4、熔剂夹杂的产生和防止
镁合金熔炼中熔剂起着很重要的覆盖和精炼作用,使用不当,会在铸件浇注位置的下部、内浇口附近及死角处产生熔剂夹杂缺陷,是镁合金铸件的常见缺陷之一,主要来源于精炼剂及熔炼工具的洗涤剂。合金液静置时间、熔剂的使用和浇注条件都会导致熔剂夹杂[4]。
镁合金精炼后要有一定的静置时间,将合金液精炼后静置时间由20 min延长至30 min,延长静置时间后,保证了熔剂能够有充足的时间从合金液体中分离出去,铸件的熔渣夹杂程度会得到明显改善。
合金采用氩气精炼,精炼熔剂用量取下限,仅用于覆盖,减少熔剂用量;熔剂坩埚的温度控制在800 ℃,使熔炼工具和升液管上的熔剂容易流下,这些措施都可以减轻熔剂夹杂缺陷的产生。
升液管距离坩埚底部要有足够的距离,防止浇注时将熔剂吸入升液管而浇入铸件。
5、气孔的产生和防止
气孔是壳体中常见缺陷。一般分为卷入性气孔和侵入性气孔,升液管使用情况、冷铁质量、型砂透气性、铸型烘烤质量和浇注速度等因素都会影响铸件气孔缺陷的形成。
升液管使用情况
升液管经过多次使用,由于长期浸泡在合金液中会腐蚀,局部腐蚀过快会形成凹坑,随着使用时间延长,凹坑会加深直至漏气,因升液管漏气而产生的气孔较大,因此升液管在使用之前必须经过认真检查,发现有凹坑要及时更换。
冷铁品质
若气孔出现在与冷铁接触的铸件表面,则可能是冷铁表面有油污或冷铁表面未烘烤透造成的。冷铁挂砂前要经过吹砂处理,挂砂后要烘烤透,未烘烤透的冷铁表面挂砂发黄。对激冷面积过大的冷铁可在表面开通气槽,增强冷铁在浇注时的排气能力。
型砂透气性和铸型烘烤
控制原砂的含泥量,将原砂的粒度由70/140目调整为40/70目,提高型砂的透气性;对铸型进行两次烘烤,提高铸型的烘烤质量,这些措施可有效减轻铸件表面气孔的产生。
在实际生产中发现,在壳体的薄壁处,特别是当薄壁面积较大时,容易产生皮下气孔,在X光检查时呈黑色斑点,往往被误判为熔剂夹杂。通过在薄壁位置的泥芯上开设浅的排气槽,减轻了表面气孔缺陷。
选择合理的充型压力
铸件在浇注过程中常常出现卷气等缺陷,主要原因是由于充填过程中充填速度过快而造成的。同时由于舱体内部结构复杂,铸件突变壁厚也会引起液体流动瞬时速率不断变化,加大了卷气的可能性。降低充型速率可有效防止卷入性气孔的产生。
三 结束语
(1)在镁合金壳体低差压铸造中,对原材料、熔化工具、金属液质量、熔化过程和细化精炼等每个环节须进行严格控制,保证金属液合格,是生产出优质铸件的前提。
(2)合理的铸造工艺是解决镁合金壳体低差压铸造缺陷的关键,可有效降低生产成本。
迟秀梅,何凯,崔恩强,张娜,朱辉,王林
上海航天精密机械研究所
本文素材来自:《特种铸造及有色合金》杂志社2019年第39卷第02期
免责声明:本网站所转载的文字、图片与视频资料版权归原创作者所有,如果涉及侵权,请第一时间联系本网删除。
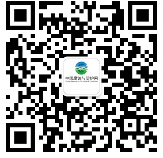
官方微信
《中国腐蚀与防护网电子期刊》征订启事
- 投稿联系:编辑部
- 电话:010-62313558-806
- 邮箱:fsfhzy666@163.com
- 中国腐蚀与防护网官方QQ群:140808414