0引言
齿轮是机械装置中传递动力的重要零部件,日本机械学会曾对各行业的齿轮传动失效实例进行过系统调查研究,约74%的齿轮传动副失效因齿轮表面疲劳失效而引起,这充分说明,齿轮的强度和使用寿命与机械装置优劣紧密相关。近年来,随着现代汽车和新能源汽车、军用车辆、舰艇、航空航天器、高速铁路设施等技术的进步发展,其动力传动机构进一步要求齿轮具有高强度化、高速度化、高效率、高寿命、轻量化和小型化(四高一轻小)等特点。这不仅对齿轮的设计提出了新的课题,也为开发新材料和创新型材料加工技术带来新的研发任务。其中表面强化技术是保证齿轮实现四高一轻小的关键。目前,我国在高强度齿轮设计与制造技术方面与欧、美、日等国家相比还存在相当差距,特别是表现在高档汽车和机械产品的零部件与国外产品的强度和使用寿命等方面的差距尤为突出,制约了我国汽车自动变速器及其他高端机电装备的发展,因此全面提升高端齿轮的高强度化成为势在必行的重要课题。众所周知,根据研究实践表明,提高齿轮的疲劳强度寿命极限,既需要改善优化材料的合金成分、渗碳、碳氮共渗热处理技术,还必须与齿轮的表面强化处理技术的研究开发结合起来,即实现综合的齿轮表面完整性得到更佳的齿轮抗疲劳性能,才能实现对高强度齿轮接触疲劳极限、弯曲疲劳极限、疲劳耐久寿命、最佳摩擦因数的高性能要求。
近年来,各汽车公司为了开发新的市场都在不断地提高汽车保证行驶里程,许多国际上著名的汽车公司都已经把保证行驶里程提升至34万公里以上。为了达到这个性能指标,美国、日本、欧洲等汽车公司都提出了更严格的市场规范要求,加大了对提高齿轮疲劳强度寿命的研究力度,并从多要素综合指标的角度深入开展研究开发。这主要包括齿轮合金材料的分析优化、齿轮最优热处理技术、齿轮表面强化技术,如磷酸锰转化涂层化学处理、齿面复合喷丸、二硫化钼加微粒喷丸齿面喷涂等齿轮表面强化技术的研究,并在轿车自动及手动变速器的应用中取得了良好的实践效果。
1汽车齿轮材料技术及研究现状
1.1国内外汽车齿轮材料及齿轮工艺参数
模数是齿轮重要的参数,选取汽车齿轮模数通常要考虑强度、噪声、轻量化及加工工艺等因素。表1为乘用车和商用车齿轮常用模数及直径工艺参数范围。
表 1 车用齿轮模数与简要工艺参数
汽车齿轮在传递扭矩和改变速度过程中,通常处于高速、高载荷、交变冲击载荷等工作环境中。汽车齿轮材料不仅需要良好的机械加工性能和热处理渗碳淬火性能,还必须满足合理的成本需求。为保证齿面和齿顶端淬火深度的稳定性,通常选用碳质量分数为0.2%左右,单独或复合添加Ni、Cr、Mn、Mo等合金元素的渗碳合金钢。日本、德国在汽车高强度齿轮低碳合金钢材料领域进行了长期的研究开发,表2为常用汽车齿轮材料的成分组成,目前国内外汽车齿轮用钢主要为20CrMnTi(国内)、20MnCrS(德系)、20CrMoH(日系),表中钢种A、B、C为高疲劳用钢。
表 2 国内外汽车常用合金钢齿轮材料的成分组成
1.2齿轮失效形式及机理
汽车齿轮处于连续负荷工作的状态,齿轮的啮合面之间既有滚动,又有滑动,同时齿根部还受脉冲与交变弯曲应力作用。齿轮通常有4种不同破坏形式:①轮齿折断;②宏观点蚀与微观点蚀;③磨损;④齿面胶合。图1所示为齿轮的损伤位置模型。
上述齿轮的失效多数源自于齿面或齿根的表面,由此看出齿轮的表面非常重要,齿轮表面完整性是指无损伤或强化后的表面状态及由其决定的性能,齿轮表面完整性包括表面残余应力、显微硬度、表面粗糙度、微观结构等,对于齿轮表面涂层改性还需考虑厚度和结合强度等因素。无论表面化学热处理,还是喷丸形变强化处理,均对齿轮的表面完整性的表面粗糙度、形态特征、组织结构、硬度、残余应力等产生影响,而齿轮的表面完整性与其弯曲疲劳抗力及接触疲劳抗力之间有密切的关系。
1.2.1齿轮弯曲疲劳破损机理及材料研究
齿轮强度主要是齿轮的弯曲疲劳强度和齿面接触疲劳强度。图2为齿轮的弯曲折断破损,主要原因是齿轮根部受到反复的集中应力作用下产生裂纹并逐步扩大致失效,弯曲疲劳裂纹从齿轮表层部的晶界氧化层产生,沿着表层下方的奥氏体晶界扩展至硬化层深处,进而引起结晶粒界破坏。
材料表层部的晶界氧化层主要由Si、Mn、Cr等可提高淬火性能的合金元素组成,其晶界边缘易产生局部不完全淬火领域,形成由屈氏体和贝氏体构成的不完全渗碳异常层。图3所示为20CrMoH试料渗碳淬火后的晶界氧化组织,由表面向内部延伸的黑色须状成分为Si、Mn、Cr的氧化物。
提高齿轮弯曲疲劳强度通常采用加大齿根R角,高压力角设计,热处理采用渗碳淬火或碳氮共渗热处理及喷丸强化等表面处理技术。例如,改善不完全渗碳异常层的方法一般可采用提高淬火速度,但要注意避免产生较大的齿面变形;或是采用降低Si、Mn、Cr等元素含量的同时增加Ni,Mo等利于提高淬火性能的合金元素。
1.2.2齿面接触疲劳机理及材料研究
齿面疲劳破损是齿轮对在齿面接触应力和齿面啮合相对滑动速度不同时所产生的拉伸应力的反复作用下造成的。破损形式以表面破坏点蚀和剥落为主,图4为齿轮点蚀破损实例。
齿面疲劳点蚀寿命与齿轮啮合时的表面温度、齿面粗糙度、摩擦因数呈正比,与润滑油动黏度成反比。通常提高材料高温状态硬度和回火软化抵抗可有效地增加齿轮的齿面疲劳寿命,试验表明,将齿面的碳质量分数由0.8%~1.0%提高到2.0%~3.0%可抑制材料表层的高温软化,但高浓度渗碳时由于微小碳化物大量析出,渗碳时间和扩散时间需要严格控制。图5为高浓度渗碳和普通渗碳的硬度与表面距离及表面温度的关系。
另一种方法是材料中适当提高Si、Cr等合金元素的含量并实施碳氮共渗热处理方法可使齿面接触疲劳寿命大幅提高,如图6所示为不同合金成分组成的齿轮钢在动力循环试验台上的点蚀疲劳实验结果对比(CQT:渗碳,CNQT:碳氮共渗)。
2热处理技术
2.1齿轮材料热处理基础研究
通过齿轮材料的基因分析和基础性能实验掌握材料基本参数与强度特性对热处理数值模拟,预测热处理变形和强度至关重要。由于热处理中渗碳渗氮的扩散过程,温度变化、相变生成、应力应变是多场耦合行为的动态过程,掌握多场耦合的动态过程是获得齿轮最优热处理工艺的关键。例如,齿轮钢在热处理过程中会产生相变塑性,其行为将直接影响齿轮在热处理后的变形和残余应力。因此,进行齿轮的热处理模拟时,若不考虑相变塑性往往很难预测并控制齿轮的热处理变形,无法确定热处理前机械加工余量。图7为齿轮钢在热处理中相变塑性试验概况。
作者之一根据连续体热力学理论和相变热力学理论,开发了热处理数值模拟C O S M A P(Computer simulation of manufacturing process)软件,可以对齿轮淬火、渗碳、渗氮以及局部加热或冷却等热处理过程进行数值模拟。图8为通过模拟得到SCM420H试样测定点在不同拉应力载荷下的应变-温度曲线,图9为根据相变塑性理论和实验获得的相变塑性系数。
2.2热处理
齿轮热处理强化技术应当注重表面完整性的控制,即控制表面硬化层的组织结构、硬化层深度、心部硬度、残余应力等。齿轮热处理控制不当易导致表层出现过度晶界氧化层组织、脱碳、微观裂纹等缺陷。
2.2.1氮碳共渗
氮碳共渗(软氮化)与渗碳相比,处理温度低,一般在460~600℃进行,因此齿轮变形小。渗氮可以提高齿轮表面硬度、耐磨性、疲劳强度及抗蚀能力。日本汽车公司对部分疲劳寿命极限要求不高,热处理后不做齿面精加工的汽车齿轮,在热处理时采用氮碳共渗工艺,通常以提高齿轮表面的耐磨性为主要目的。
2.2.2表面淬火
表面淬火主要包括感应淬火、激光淬火等。与渗碳淬火相比,表面淬火变形小。汽车齿轮表面淬火主要采用感应淬火。据齿轮模数的不同,采取不同方式的感应淬火,如齿轮模数为3~5 mm,采用高频感应淬火;当模数增大到5~8 mm,一般选中频感应淬火。高频加热淬火能得到沿齿轮廓均匀分布的淬硬层,应用高频淬火热处理对汽车转向小齿轮进行强化,试件疲劳强度得到大幅提高。高频热处理具有CO2排放少,齿轮疲劳强度和耐磨性能高,畸变较小的突出优点。激光淬火具有淬火区晶粒细小且均匀、齿轮变形小等优点,为大模数、高精度的齿轮提供了一种有效的齿面强化途径,但其成本较高。
2.2.3渗碳
渗碳是汽车齿轮表面处理中普遍应用的化学热处理方法之一。经渗碳处理可使齿轮具有很好的综合力学性能,有效防止轮齿折断。
目前渗碳的方法有气体渗碳、真空渗碳以及等离子渗碳。气体渗碳是低碳合金钢齿轮广泛采用的表面强化工艺,可使齿轮表面获得较高硬度,提高其耐磨性,而心部仍为原始的板条状马氏体组织,以保持良好的韧性。
高温渗碳将齿轮渗碳温度从900℃提高到1 050℃,可显著缩短渗碳时间约50%以上,可有效提高生产效率。但是高温渗碳容易导致奥氏体晶粒粗大化,降低齿轮疲劳性能,且变形大。为克服高温渗碳时晶粒长大问题,国内外学者发现微合金化是抑制齿轮钢的奥氏体晶粒长大的有效手段。日本的研究表明可以通过在热处理过程中主动控制渗碳深度和表面硬度,可获得最佳渗碳层深度和最小的变形。通过调整添加Nb、Ti和B等合金元素,有效控制了经高温渗碳产生的奥氏体晶粒粗大化,较好的解决了上述问题。真空渗碳与等离子渗碳具有不产生晶界氧化,表面力学性能高,CO2排放较少,热处理过程时间短节省能源消耗的优点,但成本较高。
2.2.4碳氮共渗
碳氮共渗热处理,通过有效掌握氮浓度和加氮的时间节点就能较好提高齿轮强度和耐磨性,采用碳氮共渗热处理法,有利于残余奥氏体含量的调整抑制初期疲劳裂纹向深处发展。传统的渗碳淬火钢(20CrMoH)的渗碳异常层厚度约为15~20μm左右,采用碳氮共渗处理法的渗碳异常层厚度只有其1/2。
碳氮共渗能有效提高渗层深度、细化奥氏体晶粒、减小齿轮变形、提高齿轮强度和耐磨性能。汽车用自动变速器渗碳齿轮啮合的齿面工作实际瞬间温度约达250~270℃,高于常用回火温度范围150~200℃,较高啮合温度将导致齿面硬度下降,易产生疲劳点蚀现象。采用碳氮共渗工艺,通过调整渗氮量,提高抗回火性能,抗回火温度达到300℃左右。图10所示为应用碳氮共渗工艺研究了氮含量对SCR420H钢和钢种C在170℃与300℃时齿面硬度的影响。
3抗齿轮弯曲疲劳表面强化技术
3.1齿轮基础实验
日本、德国在齿轮的基础研究领域做了大量研究。钢辊(Steel roller)试验是国外大学与研究机构齿轮基础实验研究普遍采用的方法,取得了大量的实验数据和研究成果。例如,日本应用钢辊试验进行齿轮粗糙度和模拟加工缺陷对接触疲劳寿命影响的研究。
表3所示为几种不同钢材的钢辊表面粗糙度(表中A:JIS S48C,锻造材料;B:JIS S48C,延压材料;C:JIS S50C,延压材料)。
表 3 钢辊表面粗糙度
图11所示为钢辊试件的形状和尺寸示意图。
图12所示为不同表面粗糙度齿轮材料钢辊试件的最大赫兹接触应力与疲劳循环次数关系。研究表明表面粗糙度最低的C钢辊具有较高的接触疲劳寿命极限,有模拟加工直径0.1 mm小孔的表面缺陷的C′钢辊接触疲劳寿命最低。
3.2齿轮喷丸强化
喷丸强化通过机械手段在齿轮表面产生压缩变形,使表面产生形变改性层,从而使表面强度提高,是齿轮提高齿轮疲劳强度广泛应用的方法。喷丸处理使齿面强化层内产生很大的塑性变形,齿面表层残余奥氏体向马氏体转变,诱发转变成的马氏体有方向性,并沿滑移线平行成束排列,原始马氏体的位错密度增加,结构得到细化,喷丸使得齿轮的表面显微硬度和齿面数十微米下的残余压应力提高,可大幅度提高汽车齿轮的弯曲疲劳强度极限和使用寿命。喷丸处理使得齿轮表面完整性发生下列主要变化,即①引入残余压应力场;②形变细化组织结构;③表面硬度的变化;④表面粗糙度改变;其中①②③前4种表层变化,均可改善齿轮的疲劳寿命,而喷丸带来的表面粗糙度增加则可能降低材料疲劳性能,对齿轮的噪声产生恶化,不利于汽车的振动噪声特性。通过控制喷丸强度、丸粒直径等工艺参数、采取复合喷丸来改善喷丸对齿轮表面完整性的影响。齿轮喷丸强化表面完整性的控制关键则主要体现在对齿面残余应力分布状态与表面粗糙度的控制,避免出现“欠喷”和“过喷”两种不当的喷丸强化。
3.2.1强力喷丸
日本在汽车齿轮抗弯曲疲劳强度表面强化技术研究方面,研究开发了多种形式的齿轮表面喷丸强化处理技术。如图13所示,为齿轮表面喷丸强化示意图。
日本马自达汽车公司首先研究开发了高压喷嘴形齿轮表面强力喷丸处理技术。该处理技术在室温条件下,用可控性极好的喷嘴形喷丸机使高硬度铸造钢丸(Φ0.4~0.6 mm)在高压下高速碰撞齿轮表面,使齿面在受到反复加热和急冷瞬间得到强化,齿轮表层附近的残留压缩应力显著提高,从而抑制疲劳裂纹的进展。图1 4所示为采用Φ0.6 mm钢丸在不同压力条件表面喷丸强化处理后齿面表层附近的残余压缩应力分布,其齿面硬度也发生一定的加工硬化。
图15所示,为低碳合金钢齿轮采用强力喷丸后与在未喷丸之前表层残余奥氏体含量随深度的变化曲线对比。未喷丸之前表层奥氏体质量分数为20%~25%左右,在喷丸过程中奥氏体转变为马氏体,表层0~50μm的奥氏体质量分数为0.3%~12%。通常在其他条件相同的情况下,喷丸强度越大,残余奥氏体转变为马氏体的深度越深,同时,残余奥氏体转变为马氏体的量也越多;即喷丸强度与马氏体的转变深度和转变量均成正比。
3.2.2微粒喷丸
强力喷丸可大幅度提高齿轮表层附近的残余压缩应力,促使残余奥氏体转变为马氏体,提高了齿轮的弯曲疲劳强度,然而也使得齿轮表面的粗糙度增加。微粒喷丸(≤Φ0.1 mm)技术既可提高齿轮表层附近的残余压缩应力,又能有效降低喷丸对齿轮表面的粗糙度的影响,满足了齿轮对表面粗糙度的要求。
3.2.3复合喷丸
日产汽车自动变速器研发中心采用高压强力复合喷丸强化技术对变速器齿轮进行了表面改性强化研究,较大幅度的提高了齿轮的疲劳寿命。即首先采用高硬度较大丸粒(Φ0.6~1.0 mm)在高压、高速条件下喷丸,然后再用直径较小的高硬丸粒(Φ0.1~0.2 mm)进行喷丸,在齿轮表面形成复合残余压缩应力,减轻表面加工硬化,改善表面粗糙度,提高表面硬度,齿面附近的残余压缩应力得到显著提高,进而抑制齿轮疲劳裂纹的展开。既保证了齿轮齿根附近有较大的残余压应力又不使齿面粗糙度有大的变化。具体的强力喷丸强度大小,一般采用试片进行喷丸強度的测量。
图16所示,不同类型的表面喷丸强化处理后齿轮表面附近的残余压缩应力分布,其中复合喷丸比微粒喷丸和强力喷丸的强化效果更为明显,表面最大残余压缩应力可达到1 300 MPa。
图17所示,通过采用回转弯曲疲劳试验做出多种喷丸强化处理方法的弯曲疲劳强度极限,喷丸强化处理后齿轮弯曲疲劳极限大幅提高。齿轮渗碳淬火后采用表面复合喷丸强化可使齿轮的弯曲疲劳极限提高两倍以上。
3.2.4其他喷丸新技术研究
随着科技的发展,作为导入残余压缩应力、改变表层材料组织结构、增强疲劳寿命的一项重要技术,新型新技术不断被开发应用,例如,空化水喷丸、激光空穴喷丸、超声波喷丸等。图示18为空化水喷丸原理,该工艺利用微小空化气泡溃灭时产生的冲击波压力和高速微射流打击齿轮表面,使齿轮表面层内发生高密度位错积累从而形成残余压缩应力层,来达到强化金属表面的目的。
激光空穴喷丸可以通过激光聚焦点处的微小空化气泡溃灭产生的冲击波对狭小的空间进行喷丸,参数可精确控制,残余压缩应力更大。超声波喷丸中,弹丸从各方向以超声频撞击已被固定的材料表面,由于其引入材料内部的能量较大,可用于实现材料表面的纳米化,降低氮化温度等方面。
3.2.5影响喷丸效果的主要因素
喷丸强化处理的最佳效果受到不同条件的相互影响,其主要工艺参数如下表4所示。
表4齿轮喷丸强化工艺影响因素
4抗齿面接触疲劳表面强化技术
图19为德国慕尼黑工业大学教授Nieman做出的齿轮传动的失效区示意图,图中的点线所示齿轮的抗弯曲折损强度低于齿面抗点蚀强度。
但近年来由于齿轮表面喷丸强化处理技术的研究开发成果,使得齿轮弯曲疲劳强度寿命极限得到大幅度提高,齿轮抗弯曲疲劳强度极限超过了齿面接触抗点蚀疲劳强度极限,如何进一步提高齿面接触疲劳强度极限已成为高强度齿轮技术的最重要研究课题。
齿轮对在齿面高接触应力和齿面啮合快速相对滑动产生的拉应力反复作用下会产生齿面疲劳损伤。为了防止这类损伤的产生,采用齿面改性涂层技术,可有效改善齿轮副的表面完整性和抗齿面疲劳性能。
4.1磷酸锰转化涂层
磷酸锰转化涂层工艺在提高传动部件表面强度的应用最早出现在轴承滚子的疲劳寿命改善方面。齿轮表面磷化处理后获得的磷酸锰转化涂层可以有效降低摩擦副表面的摩擦系数,具有良好的抗咬合或擦伤性能。在日本,笔者在高强度齿轮研究实践中首次将磷酸锰转化涂层技术应用于汽车自动变速器齿轮上。重庆大学石万凯与笔者在20Cr齿轮表面制备了超微细磷酸锰转化涂层,研究了磷化晶粒尺寸与涂层表面孔隙的储油特性的关系,结果表明在表面浸油润滑条件下,钢表面的超微细磷酸锰转化涂层具有明显的减摩与耐磨效果。Wang等对磷化膜后处理与润滑状况对其摩擦学特性的影响规律进行了研究。
磷酸锰转化涂层的制造工艺主要包括采用脱脂剂在温度70~95℃脱脂槽内对齿轮表面进行前处理,水清洗,然后在处理温度40~80℃条件下进行表面调整,磷化处理的温度条件80~100℃,酸比控制在5.6~6.2,处理时间10~15 min。
工艺流程如图20所示,涂层的形成通过如下化学反应来实现:
磷酸锰转化涂层处理后,齿轮表面产生数微米的软质层,填平了齿轮表面大部分凹凸切削波纹,降低了齿面的局部最大啮合接触应力和金属表面摩擦因数,改善了齿轮啮合时的油膜状况和润滑状况。通过控制磷酸锰转化涂层的工艺参数来影响涂层的密度和晶粒尺寸,可以获得超微细磷酸锰转化涂层,处理后齿面产生3~5μm的软质层,生成的涂层密度约为2.2 g/m2,处理后通过SEM观察表面形貌如图21所示。普通磷酸锰涂层处理和超微细磷酸锰涂层处理的选取需要结合齿轮加工工艺和实际工作条件来判定。
图22为圆柱辊子对油膜的形成状况,用分离电压抵抗测定法观察圆柱辊子油膜形成状况,0 V为完全接触,0.1 V为完全分离,磷酸锰涂层处理后的圆柱辊子分离电压在30 min后开始上升,其油膜形成能力明显优于无处理圆柱辊子。
通过摩擦磨损性能试验,评价涂层在一定工作条件下的摩擦学性能。如图23所示,按照齿轮的工作载荷及润滑条件,进行磷酸锰涂层试件的摩擦磨损试验,超微细磷酸锰转化涂层在低载荷与高载荷工况均具有良好持续减摩耐磨特性。
图24所示为日本JATCO自动变速器公司向大众汽车提供的自动变速器按照耐久试验要求,相同试验条件下两组AT齿轮对试验后的表面形貌点蚀情况。两组齿轮对均经过相同的加工工艺,B组齿轮对进行了磷酸锰转化涂层处理,而A组齿轮对未作处理。
如图25所示,在齿面接触点最大压力Pmax为2 000 MPa和齿根最大滑动速度为7.8 m/s的条件下进行实验,横轴表示啮合循环次数,纵轴显示每次循环下的点蚀面积率。A组齿轮在3×106 rev循环下出现点蚀破损,而B组齿轮在1.1×107 rev循环后仍未出现点蚀。试验表明,磷酸锰转化涂层使变速器齿轮的抗点蚀疲劳寿命提高了3到4倍。
4.2二硫化钼(MoS2)镀膜技术
二硫化钼(MoS2)作为一种优质的固体润滑材料,具有良好的减摩、抗磨和承载能力。二硫化钼(MoS2)膜具有层状的结构,组成沉积膜层的粒子本身具有较低的硬度和较高的稳定性。
通过采用MoS2来提高齿轮表面承载能力成为当前的一个研究热点,国内外学者做了大量研究。R.I.Amaro等采用磁控溅射在花键齿轮上获得MoS2润滑膜,在高转速下有效的降低摩擦,提高了疲劳寿命极限。K.H o l m b e r g等采用MoS2/Ti复合涂层技术能够进一步降低摩擦因数,室温下摩擦因数可低至0.07,有效减轻摩擦副运行中的摩擦和磨损。R.C.Martins等对二硫化钼复合涂层涂镀的齿轮进行了F Z G台架试验,MoS2涂镀的齿轮在5级载荷3 000 r/min的条件下运转的齿轮箱温度和摩擦因数明显下降。日本日产汽车和马自达汽车公司研究在变速器齿轮的开发实践中应用了表面二硫化钼镀膜处理技术。其主要原理是镀MoS2膜后,在齿表面产生2~3μm的软质涂层,可降低齿面局部最大啮合接触应力和表面摩擦系数,提高齿轮啮合时的润滑状况。
图26为不同材料的齿轮和齿面经二硫化钼(MoS2)表面镀膜的齿轮疲劳寿命比较,图中钢种A(1Cr-0.4Mo)为常用齿轮钢、钢种B为钒添加齿轮钢、钢种C为Mn、Mo增量齿轮钢。试验结果表明表面二硫化钼镀膜处理后,齿轮初期啮合运转后齿面平滑性明显提高,疲劳寿命提高了3倍以上。
4.3超微细复合材料喷涂技术
近年来,日本和台湾的公司研究应用了含有MoS2和超微细金属粒子复合材料的喷涂技术,其作为压力喷涂领域的一种新工法,在高强度齿轮表面强化领域得到了很好的实践效果,其工艺过程如图27所示。
主要是利用高压惰性气体推动球状研磨滚珠及固态润滑剂(MoS2)复合材料在高温高压的条件下撞击齿轮表面,并渗透进齿面1~20μm深度,使金属表面20μm深度的相组织发生改变,齿面因球形颗粒冲击而形成多处微小孔洞,使其表面组织被细微压缩而造成外应力减少,表面硬度显著提高,并通过固态润滑剂附着在表面,进而提高齿面的自润性。降低齿面粗糙度,提高齿轮啮合质量,降低啮合噪声。图28所示,某变速器齿轮滚针轴承內缘经复合材料喷涂处理后表面压痕平整度获得较大改善,同时表面形成的无数细微凹坑,利于油膜的形成,进而提高摩擦表面的油膜附着性,增强疲劳极限。
4.4齿轮表面复合强化技术
随着齿轮要求的不断提高和齿轮表面加工工程技术不断发展,将两种或多种表面强化技术对齿轮进行复合处理,提高齿轮的表面完整性以满足齿轮更加苛刻的使用要求,成为现如今齿轮领域的一种重要手段,如:QPQ(Quench polishquench)盐浴复合处理技术、热喷涂与喷丸结合的复合涂层技术、涂层与喷丸复合技术等。QPQ盐浴复合处理技术是低温盐浴氮碳共渗加盐浴氧化的一种高抗蚀性和耐磨性的金属表面改性技术。通用汽车利用该技术提高了内燃机缸套的耐磨性。大众汽车的凸轮轴与中国重汽的重型汽车减速器的内齿轮也采用了QPQ技术。热喷涂与喷丸相结合的复合强化技术使齿轮既有高抗弯曲疲劳性能,也有良好的抗接触疲劳性能,并增加了齿轮的减摩润滑性能。
4.5滚筒抛光研磨法和磨料流加工技术
滚筒研磨石抛光研磨处理(Barrelling)在一定条件下,可较好地改善齿面粗糙度和齿轮疲劳寿命且成本低。图29所示为滚筒抛光研磨法的处理概要,其处理过程采用不同种类材料数毫米直径的研磨石和研磨粉的混合体与研磨处理槽朝着同一方向回转(100 m/min),被加工齿轮的回转方向与其相反,同时进行上下平移运动,处理时间约为15~30 min。日本佐贺大学穗屋下教授同笔者和日本住友重工公司共同研究了齿轮喷丸强化处理后的滚筒抛光研磨法,取得了较好的实验效果,引起了美国和日本有关专家的关注。
磨料流加工(Abrasive flow machining),一种用具有流动性的聚合物载体和磨料组成的弹性材料对工件进行表面抛光和去毛刺的新工艺技术。Xu等对斜齿轮进行了磨料流处理,通过仿真与试验研究证明了AFM可以有效地提高斜齿轮的表面粗糙度质量。滚筒研磨抛光和磨料流技术中磨料介质的选择及配比对加工的效果十分重要,继续开展磨料对齿面粗糙度、疲劳强度的仿真与实验研究,以及多种磨料介质的最优选取与配比研究十分重要。
4.6油品对齿轮疲劳强度寿命和磨损的影响
汽车自动变速器润滑油(ATF)除要满足齿轮和轴承的润滑外还承担着液压控制油和离合器等部件的润滑和冷却作用以及动作平稳性的控制作用,对油品的动摩擦因数和静摩擦因数及其氧化耐久性都有非常苛刻的要求。近年来由于汽车自动变速器对控制系统精度和滑动性要求的提高,油品对齿轮系统的润滑面临很大的挑战。表5是汽车自动变速器两种不同油品代表性状。
表 5 试验ATF的代表性状
用于试验的斜齿齿轮对分别做了复合喷丸和磷酸锰化学处理,图30所示是动力循环式齿轮疲劳实验台。
ATF在变速器中常用的工作温度通常选择在80~110℃之间,试验在工作油温80℃条件下测得在齿轮接触应力为1 730 MPa时的齿轮疲劳点蚀率,结果如图31所示,齿轮对A的疲劳点蚀面积率小于齿轮对B。
图32显示齿轮底部的磨损量,齿轮对A的主动小齿轮远大于齿轮对B的主动小齿轮。实验表明齿轮磨损量与点蚀率成反比关系。
5齿轮表面强化的科学问题与发展
5.1齿轮表面强化的数值模拟研究与科学问题
在科学研究和工程技术领域,数值模拟是理论分析和实验测试并重的基础研究方法。数值模拟技术的发展为齿轮表面强化技术的优化设计研究提供了平台。
在齿轮喷丸强化过程的力学数值模拟研究领域,国内外学者做了一定的研究应用,包括采用弹塑性模型的一维解析法对由喷丸残余应力的预测,考虑喷丸强度因素进行二维喷射过程的模拟,运用有限元三维模型进行喷丸对微裂纹扩展、齿轮表面形貌的数值模拟研究等大量工作。然而对于喷丸强化材料纳米尺度力学性能研究,喷丸参数与齿轮性能提高的定量关系,以及不同材质、直径的弹丸多次连续撞击情况的模拟仍然需要进一步深入研究。
基于表面结构优化来改善齿轮副表面的摩擦磨损润滑性能,该领域的研究一直是学术界和工程界长期关注的热点。不同的加工及表面强化处理对齿面几何形貌、粗糙度的影响直接关系到齿轮的润滑状态。因此,研究齿轮不同齿面形貌混合弹流润滑特性,求解齿面弹性变形、表面温升及接触闪温,分析不同涂层表面润滑状态下的热解以及表面形貌与齿轮摩擦磨损的定量规律,对齿面失效机理研究与齿轮强度优化设计十分必要。
由于齿轮传动的内外部激励和非线性因素丰富,工作环境复杂多变,使其动力学分析十分复杂,制造、加工、误差、磨损、润滑和运行环境等因素将导致齿轮系统激励参数具有不确定性,多个不确定性因素同时存在,导致了齿轮系统问题的高维性,这使得齿轮失效机理与强化机理研究变得困难。因此,研究齿轮系统动力学,需要考虑不确定性优化设计方法与灵敏度分析方法。
5.2齿轮表面强化技术的发展
各种复杂工况下的齿轮传动系统使齿轮表面强化技术不断出现新的课题。例如,汽车传动系统轻量化及新能源汽车变速器高转速、高扭矩的工作状况对汽车齿轮强度提出更高的要求,新能源电动汽车变速器工况由传统汽车发动机的最高转速6 500 r/min升至14 000 r/min,转矩提高约30%,齿轮的疲劳寿命提高40%以上。单一的表面强化技术难以满足综合性能要求高的齿轮使用要求,多种复合表面强化技术进行复合处理的表面强化技术将在高强度齿轮领域得到研究应用。
表面强化技术的发展需要适应齿轮高强度、高精度、高疲劳寿命、低噪声的多目标要求。而各目标之间的非独立性和矛盾性使复合表面强化技术绝非是单一强化技术的叠加。齿轮复合表面强化技术应建立齿轮表面复合强化的多目标优化方法,运用多目标优化设计理论,对齿轮表面热处理、喷丸强化技术、表面转化涂层等工艺的强化机理与齿轮表面完整性的科学理论关系进行系统的基础研究。齿轮表面热处理未来的研究重点包括,通过齿轮材料基因分析和基础性能实验掌握材料基本参数与强度特性,预测齿轮热处理变形的数值模拟与控制技术研究、新型齿轮用钢以及新型热处理工艺的研发;齿轮喷丸强化技术的研究结合材料力学、现代力学,对喷丸参数与齿轮表面完整性(残余应力场、粗糙度、纳米尺度的力学性能等)关系;齿面各种涂层的摩擦学研究是齿轮研究的重要问题之一,基于齿轮实际工作状况、瞬态温度场和润滑条件,深入开展齿轮涂层表面完整性对接触疲劳寿命的影响规律研究。另一个重点是控制涂层组织中晶粒尺寸大小、分布以及晶界尺寸等,使涂层具有更高硬度与韧性,如何进一步实现对晶粒的控制成为研究的重要环节。
6总结
(1)表面强化技术是高强度汽车齿轮的重要技术之一,在汽车技术领域里占有重要的位置。目前,尚不能完全满足汽车自动变速器在轻量化,高转速、高扭矩、高耐久性的目标要求,应更加注重齿轮的材料与表面强化的基础与应用研究。
(2)齿轮表面热处理、喷丸强化、表面涂层等表面强化技术对汽车变速器齿轮的疲劳强度极限提升有良好的实践效果,在引进吸收国际技术的同时,进一步开展齿轮表面完整性与抗疲劳强化机理的研究是解决当前我国高强度齿轮技术问题重要任务之一。
(3)齿轮表面强化的数值模拟研究应结合热力学、相变热力学、材料力学、固体力学、摩擦学及齿轮动力学等交叉学科,建立齿轮表面强化参数与齿轮性能提高的定量关系将是该领域研究的重点。齿轮高抗接触疲劳、高抗弯曲疲劳的复合表面强化技术,应注重各表面强化处理的相互作用机理和基础研究,从多要素综合指标的角度,探索新型的齿轮复合表面强化方法,以实现齿轮发展的高强度化的目标要求。
更多关于材料方面、材料腐蚀控制、材料科普等方面的国内外最新动态,我们网站会不断更新。希望大家一直关注中国腐蚀与防护网http://www.ecorr.org
责任编辑:王元
投稿联系:编辑部
电话:010-62313558-806
中国腐蚀与防护网官方 QQ群:140808414
免责声明:本网站所转载的文字、图片与视频资料版权归原创作者所有,如果涉及侵权,请第一时间联系本网删除。
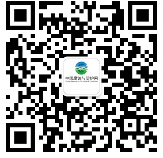
官方微信
《中国腐蚀与防护网电子期刊》征订启事
- 投稿联系:编辑部
- 电话:010-62316606-806
- 邮箱:fsfhzy666@163.com
- 中国腐蚀与防护网官方QQ群:140808414