MTBE/1-丁烯装置腐蚀原因分析及防腐建议某8万吨/年MTBE与4万吨/年1-丁烯装置主要由MTBE单元、甲醇回收单元、1-丁烯精制单元组成。MTBE生产装置是利用混合C4和甲醇为原料,在强酸性阳离子交换树脂催化作用下,混合C4中的异丁烯和甲醇反应生成MTBE,反应产物中的过剩甲醇用水萃取、精馏进行回收。如果继续生产1-丁烯产品,则相应有脱异丁烷系统和1-丁烯精制系统。
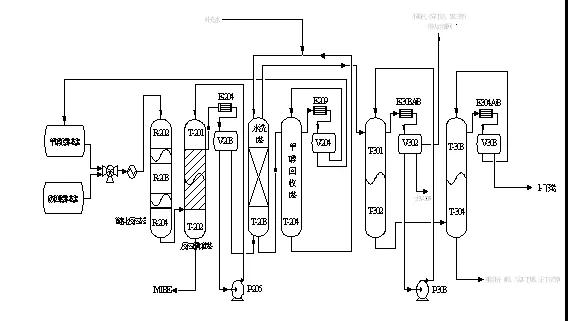
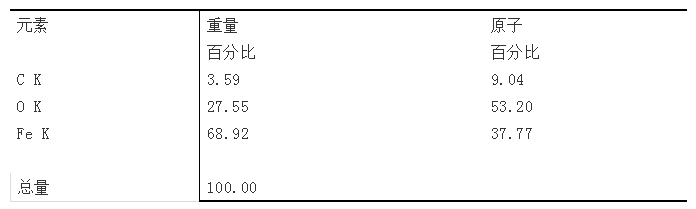
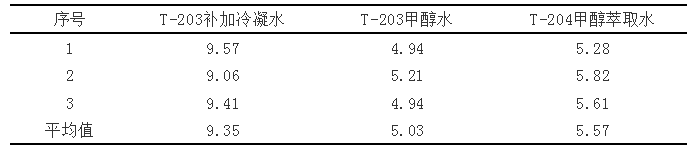
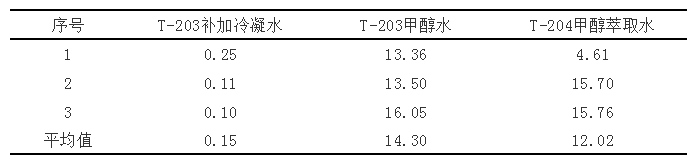
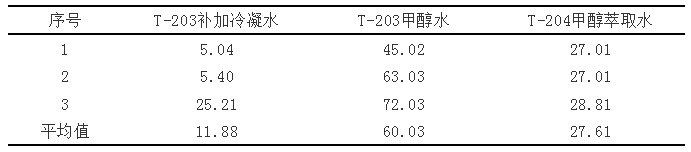
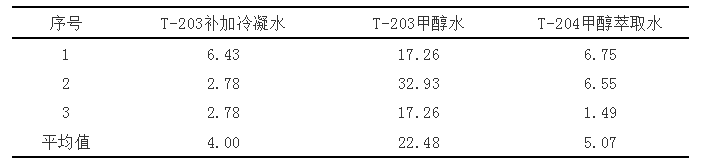
表2为装置工艺水的pH值,表2~表5分别为装置工艺水Fe2+、Cl-、S2-浓度。由表2~表5可知,三种工艺水中都发现存在Fe2+、Cl-、S2-,说明存在腐蚀。其中T-203甲醇水的pH值最低酸性最强,三次采样的平均值为5.03,并且其Fe2+、Cl-、S2-含量也最高,三次采样的平均值分别为14.30mg/L、60.03mg/L、22.48 mg/L,说明塔T-203的腐蚀较严重。T-203补加冷凝水的pH值最高,Fe2+、Cl-、S2-含量也最低。由此可知T-203的甲醇水对设备的腐蚀影响最大,其次是T-204的甲醇萃取水,次之是T-203的补加冷凝水。
03腐蚀原因分析
根据参考文献、装置工艺条件、实验数据,分析设备腐蚀有以下原因:
(1)工艺水pH值较低,呈现较弱的酸性。当酸性物质与水充分接触后,有较强的腐蚀性,当物料温度升高时,这些酸性物质对设备的腐蚀作用也增强。其腐蚀反应式为:
阳极:Fe→Fe2++2e 阴极:2H++2e→H2
这些酸性物质来源于运行过程中脱落的磺酸基、新催化剂微孔中吸附的残余硫酸和原料甲醇中可能含有的微量甲酸,但其主要来源于MTBE装置所使用的大孔径S型强酸性阳离子树脂催化剂中脱落的磺酸基。
醚化反应催化剂是由苯乙烯和二乙苯按摩尔比1:1在特殊制孔剂作用下经悬浮聚合共聚生成球珠体,经98%浓度的硫酸磺化、水洗后,最终得到的具有大孔径网状、并带有磺酸根基团的高分子聚合体。据相关资料表明,磺酸根中对位的磺酸根比较坚固,邻位的次之,乙烯基团加入的磺酸根最不稳定。实际生产过程中,导致磺酸基的脱落的主要原因是由于反应温度过高以及大量明水的存在,其反应式为:
高温磺酸基脱落:RHSO3→RSO3+H+
水浸泡磺酸基脱落:RHSO3→R+H2SO4
原料抽余碳四中的异丁烯与甲醇在催化剂作用下发生醚化反应生成MTBE,该反应为可逆的放热反应(△H=-37 KJ/mol),反应温度不易控制,容易产生“飞温”。明水的来源有三个方面:含水量为48-52%的S型强酸性阳离子树脂;
副反应CH3OH + CH3OH → CH3OCH3 + H2O产生的水;
甲醇回收塔塔顶回收甲醇含有少量的水分。此外,当工艺水中存在溶解氧时,发生吸氧腐蚀,其阴极反应式也可能为:O2+H2O+4e→4OH-
塔T-203的补加冷凝水为脱盐水,脱盐水中含有溶解氧,同时原料甲醇罐中也可能溶有微量氧气。对于T-203塔而言,由于系统中存在着活性氧,当物料经换热器换热后,氧的活性将随着温度升高而增加,不仅会发生析氢腐蚀,而且还存在吸氧腐蚀,产生了氧化铁,此时以吸氧腐蚀占主导地位。氧化铁的胶状物随循环萃取水返回萃取塔,经过塔盘分离时氧化铁对塔壁又产生了氧化还原腐蚀,其反应式为:
2Fe3++Fe→3Fe2+
这就可以解释萃取塔的萃取段腐蚀较重而沉降段腐蚀较轻的现象,萃取段的腐蚀呈现不均匀的斑驳状也说明了这一点。
(2)Cl-腐蚀。虽然三次取样补加水中Cl-含量平均值为11.88 mg/L,但由于工艺水循环利用,使得装置中Cl-含量较高。Cl-的存在对金属的钝态起到直接的破坏作用,处于钝态的金属仍有一定的反应能力,即钝化膜的溶解和修复(再钝化)处于动平衡状态。当介质中含有活性阴离子——氯离子时,平衡便受到破坏,氯离子优先地有选择地吸附在钝化膜上,把氧原子排挤掉,然后和钝化膜中的阳离子结合成可溶性氯化物,结果在新露出的基底金属的特定点上生成小蚀坑。另外,氯离子开裂敏感性会随着温度的升高和氯离子浓度的增大而增大,导致发生氯离子应力腐蚀开裂。
(3) S2-腐蚀。由于上游装置脱硫不彻底,导致装置进料中含有少量硫化物。在酸性环境下,虽然能形成附着能力很强的FeS保护膜,并且对进一步的腐蚀反应有一定的阻滞作用,但是FeS保护膜易遭到破坏,当介质中存在其它物质(Cl-、CO2等)会增加溶液的腐蚀性,特别当氯离子存在时,H2S和HCl相互促进使腐蚀加剧,可能产生氢鼓包、氢致开裂、应力诱导氢致开裂、硫化物应力腐蚀开裂等四种类型的破坏,通常发生在焊接接头的热影响区及高应力集中区,如接管处、几何突变处、裂纹状缺陷处或应力腐蚀开裂处等。
(4)磨损腐蚀。当腐蚀性流体在弯头、三通、变径管等处突然改变方向,对金属及金属表面的钝化膜产生机械冲刷破坏作用,同时又对不断露出的金属表层发生激烈的电化学腐蚀,而造成腐蚀损伤。
3相关腐蚀建议
01严格操作,稳定工艺
日常操作过程中尽量避免工艺波动,尽可能控制在操作温度的下限,绝对要避免超过催化剂的完全失活温度(120℃)。对于反应精馏塔,最关键的是调整醇烯比、回流量和塔釜温度。
02严把原料质量关
加强对原料碳四的脱水;原料甲醇尽可能使用优质品,控制其中的甲酸和水含量,关键确保甲醇回收塔塔顶回收甲醇的质量,严格防止精馏塔顶甲醇带水。特别是装置的三个放水点(原料碳四、醚后碳四和脱异丁烷塔顶)要及时将游离出来的水脱除,在设备检修后要将设备内的水吹扫干净。
定期更换离子过滤器内的催化剂,保证降低原料碳四及甲醇中夹带的金属阳离子(Na+、Fe2+、Ca2+)、硫化物和碱性物质等。在更换新催化剂后,设备投用前对新催化剂进行醇洗。
03加强监检测工作
将甲醇萃取循环水pH值的测定作为日常监控项目,控制甲醇萃取循环水pH值在6.5~8.0,发现pH值降低时使用除盐水更换系统工艺水,由于循环利用,需加大力度控制补充脱盐水的溶解氧含量及Cl-含量。
对系统关键部位的pH值和原料碳四及甲醇中金属离子、硫化物、碱性物质等进行定期监测,以便了解分析装置的腐蚀情况。
04对系统进行工艺调查分析评估采取有效措施控制装置腐蚀
如:萃取塔进料前或萃取液出口加装阴离子交换床,交换出物料中所包含的酸根离子,氢离子和氢氧根离子结合生成水进入萃取系统;降低甲醇回收塔进料温度以降低氧活性的办法来减轻该换热器和出口管线的腐蚀;降低加热器出口温度以减少相变量,降低换热器出口物流速度、换热器前加装过滤器解决机械磨损问题;考虑采取扩大管径来降低管线内的物料流速或合理设计管线走向来降低物料对管线弯头部位的冲刷腐蚀;考虑采用加碱中和的方法控制甲醇萃取循环水pH值;甲醇回收系统中加装除氧设施,加装牺牲阳极以保护设备。
05其它
腐蚀严重部位使用工业缓蚀剂;关键腐蚀严重设备进行材质升级。
免责声明:本网站所转载的文字、图片与视频资料版权归原创作者所有,如果涉及侵权,请第一时间联系本网删除。
-
标签: MTBE/1-丁烯装置, 腐蚀原因分析, 防腐建议
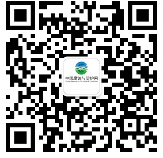
官方微信
《中国腐蚀与防护网电子期刊》征订启事
- 投稿联系:编辑部
- 电话:010-62313558-806
- 邮箱:fsfhzy666@163.com
- 中国腐蚀与防护网官方QQ群:140808414