引言
轴承是承受载荷、传递运动的关键机器零件。现代设备制造业不断增加功率密度带来的挑战,对轴承的承载能力和可靠性提出了更高的要求。
现今,轴承滚动接触疲劳造成的轴承失效一般很少发生,并且滚动轴承最终实现的使用寿命通常远远超出计算的额定寿命。然而,在特定应用中的轴承会过早失效,其使用寿命只占计算的额定寿命的5%至10%。轴承过早失效发生的时间间隔通常很短,即与正常滚动接触疲劳相比,其呈现高斜率威布尔分布 (图1)。
图1 威布尔轴承失效分布,红色斜线:典型的早期失效情况;蓝色斜线:正常接触疲劳测试的斜率
许多早期失效的轴承都有一个典型的特征——出现带“白蚀形貌”的大面积表面下裂纹网络的存在,这通常被称为白蚀裂纹(WEC)(图2)。这种裂纹通常会扩散至表面,导致滚道剥落,该现象常见于风力发电机齿轮箱、汽车传动系统、交流发电机与周边辅助设备、造纸厂和船舶推进系统等应用领域的返回产品中。一些典型的例子如图3所示。15年来,业内对这种失效的根本原因进行了广泛的讨论,基于从不同角度进行的检查提出了各种假设。对各种假设进行的综合评估和分析列在中。过去数十年,人们从不同的角度研究轴承过早失效的问题,因此对该问题的特定方面有了更多的了解。然而,在轴承失效分析方面,主要参与者依然对根本原因和失效机制缺乏共识。
图2 典型的大范围白蚀裂纹网络;大型球面滚子轴承。
图3: 来自以下应用领域的几个轴承过早失效的典型实例(a)造纸机、(b)压缩机、(c)风力发电机齿轮箱的低速段和(d)风力发电机齿轮箱的高速段。
过去四年间(本文发表于2018年),SKF更深入地调查和研究白蚀裂纹现象,旨在理清白蚀裂纹在轴承滚动接触疲劳和加速疲劳(轴承过早剥落)过程中发挥的作用。虽然材料科学界仍在讨论这个问题,但SKF的研究发现表明:白蚀裂纹发生在失效链的末端,是过早失效轴承的裂纹网络产生的自然结果。SKF认为,白蚀裂纹是疲劳失效的一种征兆,而非根源。本文阐述了SKF专家对过早失效和白蚀裂纹的多数共识看法。此外,还提出了白蚀裂纹的定义,讨论了其成因,并提出了导致白蚀裂纹的所有失效原因机制。
白蚀裂纹的定义
白蚀裂纹是轴承钢的微观结构中的裂纹,它们被白蚀区所点缀。白蚀是指抛光和浸蚀钢样时发现其微观结构已经发生改变,呈现白色外观。受影响的区域由超细的纳米重结晶无碳化物铁素体或具有非常细微的碳化物颗粒分布的铁素体组成。
白蚀区是由裂纹面在重复滚动中因摩擦造成的无定形化而形成的。由于这些区域对腐蚀反应不敏感,因此在光学显微镜下呈现白色。裂纹周围的白蚀区比附近未受影响的微观结构硬10%到50%。
形成原因
3.1滚动接触疲劳中的白蚀裂纹
众所周知,小型、重载的长期运转轴承在失效(非常高的循环疲劳)之前会经历几个疲劳阶段。
第一阶段是振动硬化阶段,会导致微塑性变形、加工硬化,并最终积累残余应力。在振动硬化状态,轴承表面也可能发生一些微塑性变形,变形部位的粗糙表面会变平。
在振动硬化后,开始进入影响轴承寿命的主要环节,其特征是微观结构逐渐改变。在此阶段,碳化物分布由于微塑性变形而发生变化。此外,残余的奥氏体也可能逐渐减少,所有微观结构变化都伴随着残余应力的积累。
在轴承滚动接触疲劳的末期阶段,发现有暗蚀区(DER)且伴有白蚀、低角度带(LAB)和高角度带(HAB)(图4左)。虽然高角度带和低角度带也都是白蚀,但相比轴承早期失效中形成的不规则白蚀裂纹,它们有不同的外观。由此可以得出结论:不规则白蚀裂纹的形成不是滚动接触疲劳一部分。不过,这些白蚀区的微观结构在晶体结构上与过早失效中观察到的白蚀区并无很大区别。
对于大中型轴承来说,上面列出的影响出现的方式,并不一定与小型重载轴承相同。与其他机械部件一样,这些轴承典型的失效原因在于其最薄弱的环节受损(例如,夹杂物和孔隙等材料结构中预先存在的缺陷)。如ISO/TR 1281-2:2008所述,当轴承的平均直径大于100毫米时,其疲劳极限会下降。此外,若比较接触应力对较小轴承和较大轴承的影响,受影响的应力体积在较大轴承中会增加,正如薄弱环节所产生的负面影响。其中一个例子是夹杂物,它们在所有轴承钢中天然存在。另外一个发挥作用的因素是接触应力本身;在图4中给出的例子中,在低角度带和高角度带产生的地方,接触应力相对较高 (>3.2 GPa)。在许多大中型轴承中,施加的接触应力远低于3GPa,这意味着疲劳载荷处于另一种状态,这导致全局损伤较少,更多的是非金属夹杂物附近的局部损伤。
早在20世纪60年代,就有报告指出,在滚动接触疲劳轴承中有出现白蚀裂纹和暗蚀图案。到了80年代,SKF内部也报告了这一点。对于过早失效的大中型轴承的后期研究(通过高加速寿命测试或标准耐久测试)已经证实,大范围的不规则白蚀裂纹网络的出现是轴承滚动接触疲劳的自然附带产生的结果(图4右)。
图4:左:深沟球轴承中的暗蚀区、低角度带和高角度带;右:大型圆锥滚子轴承耐久测试中出现的白蚀裂纹。
3.2加速疲劳中的白蚀裂纹(过早剥落)
可以通过在剥落开始之前发生不同事件所需的时间,来区分过早剥落(行业里通常被解释为白蚀裂纹失效)和正常的滚动接触疲劳(图5)。此外,与耐久性测试或正常滚动接触疲劳相比,轴承失效分析显示:过早失效通常和几个位置/区域的裂纹起始点有关。
图5 引起白蚀裂纹发展的简化事件链。
轴承钢出现裂纹的原因可能不同,在环境原因造成应力较高或强度降低的情况下,裂纹会加速发展(图6)。轴承所受的应力可能高于预期。这种情况的例子如下:
意想不到的动态的或温度的影响可能引起短期重载,导致结构变形的大预紧力、边缘载荷等。
轴承材料中的结构应力(例如,由形状偏差、不对中或其他因素引起)会增加材料中的应力。
恶劣的摩擦学接触条件(例如油膜厚度太薄和/或滑动条件),加上特定的润滑剂,也可能导致滚道上的应力增加。
一些可能产生氢的环境因素会对轴承的材料强度造成不利影响。这些可能包括:水污染、腐蚀和杂散电流。在这些情况下,正常载荷条件就可能导致过早失效。
SKF通过专门的轴承测试,验证了加速疲劳的成因,它们都与应力较高和材料强度较低有关。
图6 滚动轴承中白蚀裂纹的出现(简化)。
一旦裂纹形核(有时伴随着暗蚀区的出现),裂纹面[18-22]上的摩擦过程会导致材料从裂纹的一侧转移到另一侧。这将导致曲折裂纹的出现,并在裂纹的接收侧积累白蚀显微组织。
白蚀区的发展也取决于次表面裂纹的走向,这可能与起作用的内力和形变模式有关。这就是为什么在水平方向的裂纹(平行于滚道)中白蚀区更加常见,而垂直方向的裂纹部分常常较少出现白蚀区迹象(图7)。另外,白蚀区的产生还取决于裂纹面之间的间隙和应力循环的数量,以及材料中的内部应力状态。
图7 SKF内部测试轴承(渗氢轴承测试)的表面下裂纹中的白蚀图案。
3.3由于应力增加导致白蚀裂纹出现的例子
图8、9和10显示了与应力相关的白蚀裂纹开始出现的两个例子。图8和图9所示的结果是与某个轴承测试台有关,它被设计成通过波纹人为地将结构应力或结构变形引入轴承座,从而让轴承内圈出现局部拉伸应力。该测试采用某圆柱滚子轴承,其内圈(内径为220毫米)以正常配合安装在五叶波纹套管上,该套管以过盈配合安装在轴上。通过硬车制成的波纹套管,将在内圈的轨道表面附近产生五个拉伸应力约为205MPa的区域。测试轴承是一种改进的双列圆柱滚子轴承,在内圈的中心部分配备有一排8个滚子,而不是两排24个滚子,以适应测试台的测试能力,从而实现所需的接触应力(图8)。轴承材料为SAE 52100(100Cr6)钢,轴承的金相组织为回火马氏体,且残余奥氏体含量多达7%(体积分数),硬度为62 HRC。
这些轴承在最大赫兹接触压力1.8 GPa、kappa值约为2的条件下进行了测试。轴承测试直至失效为止。
图8 过早失效的轴承,内圈滚道有轴向裂纹。
一个轴承在五叶波纹套管上经过1150小时(对应于6.35×108个应力循环)后失效,滚道上出现一个可见的轴向裂纹。第二个轴承在1570小时(对应于8.67×108个应力循环)后失效,出现两个可见的轴向裂纹。轴向裂纹的位置在圆周方向上与其中一个波峰处重合,波峰处存在拉伸应力区。
应该注意的是,先前已在相同的条件下使用标准轴配合(没有人为引入的波纹)测试了四个同样的轴承,测试大约进行了2,200小时(对应于1.21×109次应力循环)后暂停,在此之前这四个轴承没有一个失效。在后期分析过程中未发现表面裂纹和次表面白蚀裂纹。
后期分析包括使用超声波测试(UST)和渗透法测试的无损检测(NDT)、套圈圆度测量、断口分析和显微镜下金相检查。
如图9所示,在打开裂纹的样品上制备横截面。在腐蚀后可以观察到,主裂纹的一部分在光学显微镜下显现白色,而在表面下方约500微米深度处裂纹分叉。分叉裂纹也是沿着与滚道平行的方向扩散的白蚀裂纹,与主裂纹相距约400微米。分叉裂纹的放大图(图9b、c和d)证实了裂纹相互连接、在表面下形成网状白蚀裂纹的理论。在与波纹套管轴波峰处相对应的另外两个圆周位置,也制备横截面。虽然在表面上没有观察到表面裂纹,但在这些区域的表面下发现多个白蚀裂纹,这些区域在测试期间存在由波纹引起的拉伸应力。
图9 在光镜下显示的轴向裂纹的平行截面的白蚀裂纹,以及三个指示区域的放大图像。主裂纹的一部分和分叉裂纹伴随有白蚀区。(b)、(c)和(d)中的照片分别是(a)中由数字1-3表示的放大区域。
图10所示是23024球面滚子轴承在短期重载测试下的结果。
图10:由短期重载引起的23024轴承外圈中的表面下大范围白蚀裂纹网络。
在短期重载期间,轴承在良好的润滑条件下(kappa约为3.5)承受3GPa以上的接触应力达15分钟左右。
将已经承受短期重载的轴承安装在径向测试台上。然后,在接触应力1.7GPa和Kappa值约为2的润滑条件下测试。在该条件下,轴承在大约3.3×107次循环后停止承重或者在此之前失效。图10显示了外圈的周向切开和进行金相腐蚀的结果。由于外圈承载区剥落,相关轴承在1.9×107次循环后失效。
3.4由于材料强度较低而产生白蚀裂纹的例子
图7已给出了渗氢轴承的表面下白蚀裂纹的例子。对渗氢和非渗氢的角接触球轴承以及深沟球轴承的详细事后分析可参见文献22。
3.5在摩擦与润滑剂共同影响下产生白蚀裂纹的例子
在使用FE8测试台进行润滑油评估测试时,发现失效的81212圆柱滚子推力轴承中有白蚀裂纹[23]。迄今为止,在混合摩擦和高的运动滑动(不代表径向滚子轴承)混合测试条件下未得到结论性的结果。到目前为止,FE8测试中的白蚀裂纹主要是由来自表面的疲劳(其中,润滑剂也起到重要作用)造成的,还是由于氢进入,亦或是二者共同的结果,无法给出最终结论。
图11 81212轴承滚子的典型失效外观(左)和垫圈内出现的白蚀裂纹(滚道下84um处的横截面)(右)
使用钢对钢测试系统对81212圆柱滚子推力轴承进行了轴承测试。轴承材料为SAE 52100标准轴承钢,马氏体硬化,残余奥氏体含量小于3%,硬度约为60HRC。这些轴承在中等载荷(最大接触应力约1.9GPa)和不充分润滑条件下进行了测试(kappa约为0.3)。
测试采用了不同的润滑油和混合油。典型失效外观如图11所示。
尽管此处没有详细说明,但在所有测试中,主要是滚子失效,很少有垫圈失效。测试一直持续到失效(剥落)或最终停止。对于因剥落而失效和发现白蚀裂纹的轴承,假设在任何剥落发生之前,已经产生点缀有白蚀的次表面裂纹。做出这一假设,因为有时在非剥落部件中也发现了次表面裂纹。详细信息,请参阅文献15。
讨论
上述研究发现解释了为什么所有类型的工业、所有类型的轴承和所有类型的热处理(整体淬硬和表面淬硬材料)中都能发现白蚀裂纹,这是因为白蚀裂纹出现在失效链的末端,并且是过早失效的轴承中的裂纹网络产生的自然结果。
要查明轴承过早失效的根本原因,其关键不仅在于研究白蚀裂纹,更要找出导致加速疲劳的相关弱化影响(与应力较高或材料强度较低有关)。
一般来说,任何机械部件的失效都是由于其最薄弱环节受损造成的。当局部应力超过局部强度时,就会发生这种情况。过早失效是最薄弱的环节显著弱化的结果。各种应用中使用的滚动轴承的可靠性符合最弱环节原则。弱点总是存在于材料内或工作接触面上。如果最弱的环节出现问题,那么轴承就会失效。当润滑条件不佳或表面粗糙时(例如颗粒压痕),最弱的环节就最有可能出现在表面上,那么表面损伤(例如表面疲劳或磨损)就会导致轴承失效。在良好润滑条件下,由于存在材料缺陷(例如,夹杂物和赫兹接触导致的高剪切应力、轴承失效由于材料预先存在的缺陷引起的裂纹萌生和扩展),那么最薄弱的环节可能就在表面下。
对于滚动轴承来说,最薄弱环节的强度可能与所谓“疲劳极限”的载荷或应力极限有关。如果超过疲劳极限,那么轴承就会失效。当疲劳极限显著降低时,换句话说,当最薄弱环节的强度显著降低时,就会发生轴承过早失效。造成早期裂纹产生并加速裂纹扩散,最终导致轴承过早失效的原因,是应力较高或材料强度降低引起的弱化,而不是白蚀裂纹。在不存在弱化现象的情况下,轴承也可能会失效,这是正常滚动接触疲劳单点剥落的结果,很少或不会产生白蚀裂纹,这是因为当材料寿命结束时,裂纹会迅速扩展[7]。换句话说,没有时间在裂纹系统内进行材料转变。随着弱化程度的增加,轴承可能会过早失效,表现为出现大范围的白蚀裂纹,因为裂纹系统中的材料有时间在局部从暗蚀区转变为白蚀区。随着严重程度提高,可能会出现较小范围的白蚀区点缀的轴向裂纹,甚至会出现没有白蚀区点缀的断裂,这是由于裂纹扩展过快所致
建议
每个轴承的过早失效都是独一无二的。再看图6,可以看出,过早剥落的原因可能大相径庭。不存在单一的根本原因,每个失效个案都需要根据相应的运行条件进行检查。
在将弱化驱动因素分类为“应力较高”和“材料强度较低”的基础上,可以给出如表1所示的通用建议。该表分别列出了针对应用本身的建议(轴承系统、设计过程)以及进一步提高轴承坚固性的可能性。哪个选项能够最有效地防止过早失效,取决于具体的应用环境。欲了解更多建议,请联系SKF应用工程服务部。
表1 避免过早剥落失效的建议
免责声明:本网站所转载的文字、图片与视频资料版权归原创作者所有,如果涉及侵权,请第一时间联系本网删除。
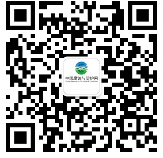
官方微信
《腐蚀与防护网电子期刊》征订启事
- 投稿联系:编辑部
- 电话:010-62316606-806
- 邮箱:fsfhzy666@163.com
- 腐蚀与防护网官方QQ群:140808414