从 20 世纪 80 年代,随着深海油气资源开发技术的逐渐成熟,大量深海石油平台、管道和 FPSO 等海洋工程装备投入使用。深海腐蚀环境特征与表层海水显著不同,服役深海环境的工程装备结构安全以及腐蚀控制技术受到了格外的重视。
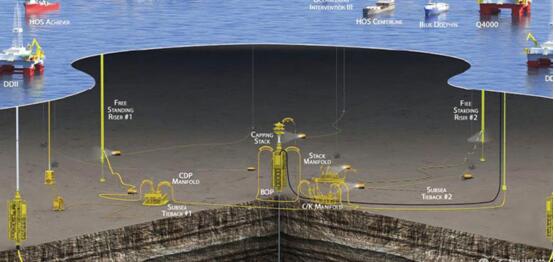
阴极保护技术是海洋工程装备最常用、最有效的腐蚀防护技术,该技术可单独用于海洋工程装备的腐蚀防护,也可与涂层配套应用,不仅可以防止均匀腐蚀,也可有效防止孔蚀、缝隙腐蚀、应力腐蚀、电偶腐蚀等。针对深海环境腐蚀新特征与腐蚀防护新挑战,国内外在深海阴极保护设计、牺牲阳极材料、阴极保护应用技术研究等方面开展了卓有成效的研究。
一、深海阴极保护参数
阴极保护效果与阴极保护设计参数直接相关,包括保护电位、电流密度、阳极材料与数量等,其中保护电位和电流密度是两个最重要的阴极保护设计参量。阴极保护电位范围由材料特性决定,而阴极保护电流密度选取由保护电位范围控制,二者间的函数关系与材料特性(极化特性、表面状态)、环境参数(温度、溶解氧、流速、盐度)等有关。
1、深海条件阴极保护电位判据
为保证深海工程装备结构强度,普遍采用高强度合金制造,材料强度越高,氢脆敏感性也越高。阴极保护过程中,高强钢表面发生吸氧或析氢反应,或二者同时发生。阴极保护电位越负,越容易发生析氢反应,材料发生氢脆断裂的风险越高。因此,对高强钢阴极保护电位范围应进行严格控制。目前,国内外尚无高强钢在深海条件下的阴极保护电位判据标准,但相关研究表明,当阴极保护电位负于一定值后,材料伸长率、断裂时间均随阴极保护电位负移而减小。对于屈服强度为 500 ~ 900MPa 的高强钢,最佳保护电位范围为 -0.790 ~ -0.870V(vs Ag/AgCl/ 海水,下同)。对于强度超过 900MPa 的高强钢,最佳保护电位范围为 -0.79 ~ -0.81V.不同材料最佳阴极保护范围为:钢-0.8~-1.00 V,铜-0.45~-0.60 V, 铝-0.9~-1.15 V,高强钢(500~900 MPa)-0.79~-0.89V,高强钢(>900 MPa)-0.79~-0.81V.
2、深海条件阴极保护电流密度
(1)压力对阴极保护电流密度影响。阴极保护过程中,氧还原反应产生 OH - ,OH - 与海水中的 Mg 2+ ,HCO 3 - ,Ca 2+ 反 应, 生 成 保 护 性 的 CaCO 3 ,Mg(OH) 2 等沉积物附着在被保护结构表面,可减小阴极保护电流密度。压力越大,碳酸钙溶解度越大(500m 深海条件下碳酸钙溶解度为表层海水的 5 倍),越不容易在被保护对象表面形成钙镁沉积层。在高压力深海条件下,沉积物主要为 Mg(OH) 2 .同时压力越大氧气活度越大,所需阴极保护电流密度越大。因此,阴极保护电流密度随着压力增加而增加。在海水流速为 0,表层海水与3000m 深海条件下,钢质材料所需阴极保护电流密度对比见表 1.
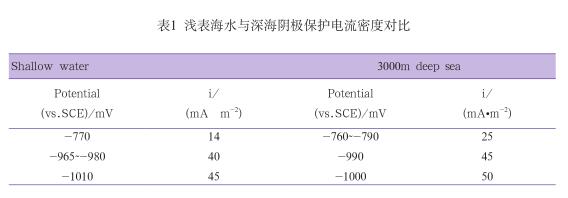
(2)流速对阴极保护电流密度影响。流速对阴极保护电流密度影响显著,流速越大,氧气扩散越快,氧气还原速度越大,所需阴极保护电流密度也越大。3000m深海条件下, 当海水流速从0m/s增加至10m/s, 若要达到-850mV的阴极保护电位,阴极保护电流密度需从 30mA/m 2 增加至 250mA/m 2 .
DNV-RP-B401 推荐的不同深度不同温度裸钢初始、后期以及平均阴极保护电流密度见表 2.根据 S.Chen 等人在墨西哥湾开展的 900m 实海阴极保护参数研究结果,施加 0.1A/m 2 平均保护电流密度,钢试样表面电位约为 -0.9 ~ -1.0V,容易造成高强钢发生氢脆断裂。深海装备阴极保护工程公司采用 21.5mA/m 2 电流密度标准设计钢质结构阴极保护系统,远小于表 2 建议的阴极保护电流密度。
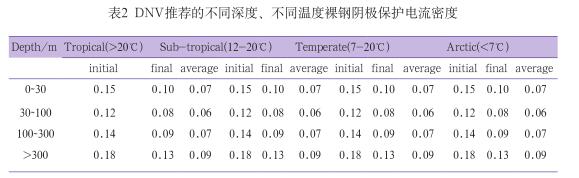
综上,阴极保护电流密度受海水压力、流速等多因素影响,因此,在进行阴极保护设计时,要针对工程装备服役环境特点,确定阴极保护设计参数,切不可以盲目照搬。
二、深海环境对牺牲阳极性能影响
1、温度影响。温度对牺牲阳极性能影响显著,一方面深海海水温度显著低于表层海水温度,温度降低,牺牲阳极活性降低,开路电位和工作电位轻微正移,阳极溶解形貌变差,溶解形式由均匀溶解变为局部溶解。另一方面,对于输送高温介质的管道,牺牲阳极工作在高温条件,随着温度升高,常用的 Al-Zn-In 系牺牲阳极电容量显著降低。
2、压力影响。深海压力作用下,材料处于弹性变形状态,根据 E.M.Gutman 机械电化学理论,压力增加牺牲阳极开路电位负移,腐蚀速率增加。研究表明,在海水压力作用下,压力加剧 Al-Zn-In 牺牲阳极晶间腐蚀诱发的应力腐蚀开裂,导致电流效率降低。
3、溶解氧影响。与表层海水相比,深海海水溶解氧含量降低,其对 Al-Zn-In系牺牲阳极主要有两方面影响 : 一方面, 溶解氧含量减少, Al 2 O 3 氧化膜生产速度降低,有利于阳极活性溶解;另一方面,又导致 In,Zn 等合金元素“溶解 - 再沉积”困难,造成牺牲阳极活性溶解能力下降,其中对 In,Zn 等合金元素“溶解 - 再沉积”.影响程度大于对 Al 2 O 3 氧化膜生产速度影响。因此,溶解氧含量降低,牺牲阳极活性降低,电流效率降低。
4、压力交变影响。压力交变环境,牺牲阳极溶解产生的阳离子 (Al 3+ ,Zn 2+ ) 与氧气还原产生的 OH- 离子反应生成的沉积物 (Al(OH) 3 ,Zn(OH) 2 ) 容易附着在阳极表面,导致阳极工作电位正移,活性降低。
三、深海牺牲阳极材料研究
1、深海牺牲阳极研究。为解决深海环境牺牲阳极材料性能下降问题,美国开发了深海铝合金牺牲阳极,阳极成分(质量分数)为:Fe ≤ 0.07%,Zn4.75% ~ 5.25%,Cu ≤ 0.005%,Si≤ 0.10%,In 0.015% ~ 0.025%,Cd≤ 0.002%,Al 余量。国内中国船舶重工集团公司第七二五研究所也开发了专用于深海环境的铝合金牺牲阳极材料,在浅海和模拟 600m 深海环境,电容量均达到 2650Ah/kg 以上。深海牺牲阳极工作电位约为 -1.1V,主要用于保护屈服强度不高的钢质结构以及铝合金等。
2、低电位牺牲阳极研究。牺牲阳极工作电位过负,易导致高强钢氢脆断裂,为解决阳极工作电位与高强钢阴极保护电位范围要求不匹配问题,开发了基于 Ga 活化的低电位牺牲阳极,其工作电位范围为 -0.78 ~ -0.88V.
3、高活化牺牲阳极研究。通过添加 Mg,Ga,Mn 等合金元素,提高 Al-Zn-In 牺牲阳极的活性,减少腐蚀产物在阳极表面的附着,解决压力交变与干湿交替环境牺牲阳极结壳导致性能下降问题,主要用于深潜器、ROV、海底挖沟机等。中国船舶重工集团公司第七二五研究所研制的 Al-Zn-In-Mg-Ga-Mn 高活化牺牲阳极已在海洋工程装备上安装应用,并取得了良好的效果。
四、阴极保护技术应用
深海工程装备的阴极保护方法有牺牲阳极阴极保护法和外加电流阴极保护法。由于牺牲阳极保护系统可靠性高,无需维护管理,大部分深海工程装备采用牺牲阳极保护法。外加电流阴极保护法主要用于牺牲阳极设计寿命到期后仍需要继续服役的工程装备,特别是石油平台的后期保护。
1、牺牲阳极保护法
(1)石油平台及管汇。全世界90% 以上的石油平台桩腿采用牺牲阳极保护,阳极形状一般为长条状,采用焊接方式安装在桩腿上。深海环境中,牺牲阳极用于保护采油树及管汇等。典型水下管汇主要由防沉板、结构框架、生产设备、保护架组成,阳极主要安装在结构框架和防沉板上。
(2)海底管道。海底管道特别是深海管道,主要采用涂层(3LPE/3LPP)联合牺牲阳极技术进行防护。牺牲阳极采用镯式 Al-Zn-In-Si 牺牲阳极。牺牲阳极达到设计寿命后,如管道仍需服役,需要对牺牲阳极保护系统进行更新。具体技术方案为:将一定数量的牺牲阳极固定在框架上, 组成框架式阳极系统 (雪橇式框架阳极、扩大式框架阳极、混凝土和框架共同固定的阳极等),然后通过水下机器人按设计间距将被保护管道与框架式阳极系统电连接。其中雪橇式框架阳极和扩大式框架阳极适用于沙地环境,混凝土和框架共同固定的铝阳极适用于任何环境管道保护。
2009 年,墨西哥湾 124 个海洋工程装备进行了牺牲阳极和外加电流的更换、翻新。
(3)深潜器。深潜器通常采用涂层联合牺牲阳极保护技术进行腐蚀防护。深潜器一般由耐压结构和非耐压结构组成,耐压结构材料强度高,通常采用 Al-Ga 低驱动电位牺牲阳极进行保护;而非耐压壳体处于压力交变、干湿交替的服役环境,采 a 用高活化牺牲阳极进行保护。
2、外加电流阴极保护法
与牺牲阳极阴极保护法相比,外加电流阴极保护法的最大优点是只需安装较少的辅助阳极即可满足工程装备的防护需求,且保护度可调,但技术难度更高,且需要外加电源,不适合大深度工程装备防腐。
主要用于石油平台和大型船舶阴极保护,此外还用于牺牲阳极消耗完采油平台的后期防护。
由于辅助阳极发出电流量大,为避免辅助阳极附近电位过负,通常采用远距离沉底布置辅助阳极的方式(保护对象与辅助阳极距离不小于 15m)对石油平台进行阴极保护,阳极输出电流越大,布放距离越远。 沉底式辅助阳极结构为:
辅助阳极安装在浮体上,浮体固定在基座上,浮体产生向上的浮力,保证辅助阳极与被保护对象平行。
外加电流阴极保护技术电位精确控制难度远大于牺牲阳极阴极保护技术。
因此,选用外加电流阴极保护技术对海洋工程装备,特别是由高强钢制造的深海工程装备实施阴极保护时,必须根据环境特点精确设计,并辅以阴极保护电位检测系统测量保护电位,评估装备氢脆失效风险。
展望
深海油气资源开发力度加大,大量深海工程装备投入使用,对海洋工程阴极保护技术的发展和应用提出了迫切需求,目前深海阴极保护技术还有如下几方面问题亟需解决:
1)明确深海工程装备阴极保护电位、电流密度判据,并通过阴极保护优化设计方法,精确设计阴极保护系统,优化防腐效果。
2)发展新型阴极保护材料,满足服役于不同深海环境的工程装备防腐需求。
3)发展智能化、便宜操作的阴极保护监检测新技术,监测阴极保护效果,评估海洋工程装备结构安全。
免责声明:本网站所转载的文字、图片与视频资料版权归原创作者所有,如果涉及侵权,请第一时间联系本网删除。
相关文章
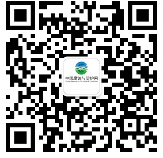
官方微信
《中国腐蚀与防护网电子期刊》征订启事
- 投稿联系:编辑部
- 电话:010-62316606-806
- 邮箱:fsfhzy666@163.com
- 中国腐蚀与防护网官方QQ群:140808414
点击排行
PPT新闻
“海洋金属”——钛合金在舰船的
点击数:8125
腐蚀与“海上丝绸之路”
点击数:6461