近年来,随着我国石油工业的快速发展,海底油气管道内壁的腐蚀问题受到了广泛的关注。当油气管道与外部环境存在较大的温差时,水蒸气会在温度较低的管道顶部凝结,导致严重的顶部腐蚀(TLC)。1959年在法国LACQ酸性气田第一次发现了顶部腐蚀问题,之后在加拿大、印尼、美国等国家也相继发生了严重的顶部腐蚀案例。顶部腐蚀的出现会严重影响管道的安全性能。
物理法与电化学法是两种研究腐蚀问题的常用分析手段。顶部腐蚀的腐蚀环境是体积微小的冷凝液滴,液滴出现的位置具有一定的随机性,难以布置有效的对电极与参比电极来构造三电极体系,因此用常规的电化学方法研究顶部腐蚀是无效的,国内外学者大多采用物理法来研究顶部腐蚀。
有研究发现影响顶部腐蚀的主要因素有CO2分压、温度、气体流速、水冷凝率以及CH3COOH含量等。也有研究人员通过布置在挂片下方的温度传感器测液滴的滴落周期,提出液滴在试片表面的滞留时间(DRT)对顶部腐蚀有重要的影响。但是,由于失重法无法对顶部腐蚀进行连续性监测,为了得到更为详细的腐蚀发展状态,需频繁取出试片称量,该方法操作复杂且会带来一定的误差。此外,冷凝液滴分布的随机性决定了顶部腐蚀是一种局部腐蚀现象,通过失重法得到的是平均腐蚀速率,无法得到准确的局部腐蚀信息。因此,设计一种新的顶部腐蚀监测方法是十分必要的。
新型传感器的设计加工
新型传感器为3×3阵列电极传感器,由9个试片按3×3阵列排列,如图1所示。其中,8个试片为X65管线钢,1个试片为304不锈钢,试片尺寸均为10mm×10mm×2mm,工作面的表面积为1cm2,背面焊接铜导线。304不锈钢试片居中(标注为0号试片),X65管线钢试片环绕其四周(标注为1~8号试片),相邻试片的间距为1mm。
(a) 正视图
(b) 横剖面图
图1 传感器试片布置和尺寸示意图
除工作面外,其余面用环氧树脂密封。传感器总厚度为4mm,以保证传感器具有良好的传热性能。封装完成后,用400号至1200号水磨砂纸逐级打磨工作面,并依次用无水乙醇和去离子水冲洗后烘干。在打磨过程中要确保工作面平整,防止表面倾斜影响冷凝液滴的形成。工作表面封装完成后,将传感器放置于干燥箱中备用。
顶部腐蚀试验装置
图2 顶部腐蚀试验装置示意
如图2所示,通过泵机向冷却水箱中循环注入温度为10℃的冷却水,使装置顶部环境保持恒定低温。将传感器紧贴于冷却水箱下表面,确保冷却水可以起到良好的冷却作用。试验溶液为去离子水,装置内部与空气连通。将试验装置的玻璃容器部分置于水浴恒温箱中,水浴温度维持在70℃,使装置底部保持恒定的高温。由此,传感器下表面与气体环境之间形成温度梯度,冷凝液滴会在传感器下表面形成。腐蚀性气体溶解在冷凝液滴中,形成顶部腐蚀环境。为了观察液滴的形成和试片的腐蚀过程,在传感器下方安装了数码摄像头,进行观察记录。
顶部腐蚀试验方法
采用CST508多通道腐蚀监测仪测量工作电极之间的电偶电流以及它们相对于参比电极的耦合电位。其中,1~8号试片为工作电极,0号试片为参比电极。
当传感器置于空气中时,各个试片之间没有电解质连通,无法测得其电偶电流与耦合电位。而在顶部腐蚀环境中,试片工作面与气体环境的温差使水蒸气在试片表面冷凝,形成冷凝液滴。试验中未引入挥发性介质,因此试片表面的冷凝水同样为去离子水。当空气中的O2与CO2等可溶性气体溶于冷凝水中时,形成腐蚀环境。
由于液滴的附着位置具有随机性,为了方便讨论,假定一种液滴的附着情况,如图3所示。图中1?2?4?0号试片被同一滴液滴覆盖。液滴长时间附着于试片表面,液滴内部溶入Fe2+?H+?CO32-?HCO3- ?OH-等离子,形成电解质环境。此时,1?2?4?0号试片被液滴导通,可以测量出1?2?4号试片之间的电偶电流,以及它们相对于0号试片的耦合电位;1?2?4号试片之间测得的电流数据具有对应关系,理论上同一时刻其电流和为0。同理,3?5号试片与6?7号试片之间同样存在电偶电流,且分别具有对应关系。由于腐蚀过程的不确定性,被不同液滴覆盖的区域(如1?3?5号试片)所对应的电流数据之间不存在对应关系。由此,通过电偶电流数据,可以推断出液滴分布位置。当液滴自试片表面滴落时,试片表面状态会发生剧烈改变,导致试片之间的电偶电流发生突变。因此,可以通过电流数据的变化得出液滴滞留时间。
图3 一种假定的试验情况示意图
综上,理论上新型传感器可以有效监测顶部腐蚀液滴覆盖区域的具体位置以及液滴滞留时间等关键信息,弥补了传统传感器的不足。
试验过程中,耦合电位与电偶电流的测量时间间隔为3s,试验共进行2天。试验结束后,将试片取出,用酸洗液清除表面腐蚀产物,随后用去离子水冲洗干净,置于光学显微镜下观察其腐蚀表面形貌。
顶部腐蚀试验结果
01 宏观形貌
(a) 2min (b) 5min
(c) 15min (d) 30min
(e) 1h (f) 3h
(g) 12h (h) 48h
图4 顶部腐蚀不同时间后试片表面的宏观形貌
在试验开始阶段,水蒸气在试片表面大量形核,生成微小的液滴,如图4a,b所示。随着时间的推移,水蒸气的凝结量不断增加,小液滴不断生长,逐渐与相邻的液滴融合,形成近乎于覆盖所有试片的薄液膜,如图4c~e所示。在这一过程中,X65管线钢试片开始出现点蚀,点蚀坑出现的位置与液滴的形核、聚集过程有关。随后,液膜下的腐蚀逐渐加剧,X65管线钢试片的表面不再光亮,而作为参比电极的304不锈钢试片在这种环境中没有发生腐蚀,表面依旧光洁。
随着水蒸气的进一步冷凝,液膜厚度逐渐增加,由于重力以及表面张力作用,冷凝水聚集形成较大的冷凝液滴。试验中,液滴主要形成在8号试片表面,同时覆盖了部分5?7号试片,其余X65管线钢试片表面没有液滴,如图4(f)所示。此时,304不锈钢试片与X65管线钢试片表面的冷凝水不再连通。此后,液滴位置不会发生改变,液滴覆盖区域下的试片腐蚀加剧,而其他试片表面的腐蚀无明显变化。
液滴的形成、滴落与液滴在试片表面的吸附力有关,计算公式为:Fσ = πr2(2σ/r)(Fσ为水在试片表面的吸附力;r为液滴半径;σ为表面张力)。
水表面张力大小与其在试片表面的接触角有关,而接触角受试片表面粗糙度的影响。试验初期和中期,X65管线钢试片与304不锈钢试片表面粗糙度相同,冷凝过程相仿,试片表面间液膜连通。随着时间的推移,X65管线钢试片表面逐渐形成腐蚀产物,而304不锈钢试片表面保持光洁。此时,两种试片的表面粗糙度发生改变,水分子在两种试片表面的吸附力随之改变,冷凝过程也相应产生差异,液膜不再相连。图4d~f中液膜的变化过程很好证实了这一现象。
试验结束后,取出试片,清除其表面残留冷凝水,其表面腐蚀产物形貌如图5所示,可见试片表面的腐蚀产物呈棕黄色,为铁的氧化物及氢氧化物的混合物。
图5 顶部腐蚀试验结束后试片表面腐蚀产物的形貌
根据液滴的分布情况,可将8个X65试片分成3类。第一类为完全没有液滴覆盖的试片,包括1?2?3?4?6号试片;第二类为部分被液滴覆盖的试片,包括5?7号试片;第三类为完全被液滴覆盖的试片,为8号试片。
从上述3类试片中分别选取2?5?8号试片,置于100倍光学显微镜下观察,其腐蚀表面形貌如图6a所示。结果表明:1号试片表面除点蚀坑外,其余部分仍可见金属光泽,腐蚀产物较少;5号试片上半部分表面状况与1号试片的相仿,然而在其下部有液滴附着的区域,腐蚀产物显著增多,几乎无金属光泽;8号试片表面的腐蚀产物较厚,近乎覆盖整个试片表面,有明显的黑色与褐色腐蚀产物,分别是铁的二价与三价氧化物。
(a) 试验结束未清除腐蚀产物
(b) 试验结束清除腐蚀产物
(c) 试验时间为60min时
图6 不同状态2,5,8号试片的表面腐蚀形貌(100×)
将上述三个试片用酸洗液清除表面腐蚀产物后,置于100倍光学显微镜下观察,得到试片的表面形貌如图6b所示,可见2号试片与5号试片的上半区域,即没有液滴覆盖的区域,点蚀坑极其微小,可清晰地观察到试片表面的打磨痕迹,表明该区域腐蚀速率较小;而8号试片与5号试片的下半部分,即被液滴覆盖的区域,存在面积与深度均较大的点蚀坑,且8号试片表面已无法观测到打磨痕迹,表明该区域腐蚀速率较大。选取试验时间为60min时2?5?8号试片的影像,观察试片的腐蚀情况,如图6c所示。通过对比发现,在试验中期3个试片表面的蚀坑数量、位置与试验结束后几乎没有变化。由此说明顶部腐蚀过程中点蚀坑出现只与初始时小液滴的形核、聚集过程有关,但当试片表面形成大液滴,并不断重复稳定的生长和滴落过程,点蚀只会在已有的蚀坑处发展,不会形成新的蚀坑。
02 电偶电流与耦合电位数据
图7 试验测得8个X65管线钢试片的耦合电位随时间变化曲线
试验初期(试验开始至60min)
如图7所示,耦合电位表现为幅值较大的正弦信号。试验初期,X65管线钢试片表面布满微小的冷凝液滴,作为工作电极的8个X65管线钢试片与作为参比电极的304不锈钢试片之间没有介质连通,不构成闭合回路。因此,此时无法测得耦合电位,图中正弦信号其实是仪器固有的随机信号。
在试验初期与中期的过渡阶段
工作试片开始出现明显的点蚀坑,试片表面的小液滴不断生长融合形成不均匀的液膜,将工作试片与参比试片连通。因此,理论上可以测得8个工作试片的耦合电位。然而这一过程为液膜生成的初始过程,其厚度较薄,溶液电阻较大,导致测量误差较大。此时,耦合电位虽然仍表现为正弦信号,但与试验初期的正弦信号比,其均值和幅值均有所改变。耦合电位逐渐降低表明工作试片腐蚀不断加剧,此外电位的幅值变化可以反映出连接工作试片与参比试片的液膜厚度变化。
试验中期(试验进行至1~3h)
试片表面液膜厚度增加,导电性有所提升。此时,电位减小,得到的耦合电位较为准确。
试验后期(试验进行至3h后)
电位波动幅值又开始逐渐增大,直至回到试验的初始状态。这一阶段工作试片表面的液膜逐渐转变为大液滴,溶液覆盖区的面积减小。由于工作试片表面存在锈层,参比试片表面的液滴冷凝过程与工作试片表面的不再相似,二者之间不再有介质连通,因而无法测得耦合电位。电位波动幅值的逐渐增大可能代表连通二者的液膜面积逐渐减小。
图8 8个X65工作试片之间的电偶电流密度随时间变化曲线
试验初期(试验开始至60min)
如图8所示,8个工作试片相互独立,电偶电流均为0。
在试验初期与中期的过渡阶段
电偶电流会在相邻的两个试片之间产生小幅波动,如3号与5号试片,表明两个试片之间有小液滴融合。
试验中期(试验进行至1~3h)
8个工作试片的电偶电流密度均有显著增大。此时,液膜覆盖整个传感器表面,8个工作试片彼此连通,电偶电流密度的大小反映了试片表面液膜状态及腐蚀情况。这一阶段电偶电流密度大小剧烈波动,但在后半段电偶电流密度的变化开始呈现出一定的周期性。
试验后期(试验进行至3h后)
除5、7、8号试片外,其余试片的电偶电流密度减小为0,说明只有5、7、8号试片被液滴附着而连通。5号与7号试片电偶电流密度较小,为阴极电流,试片腐蚀缓慢;8号试片电偶电流密度较大,表现为阳极,试片腐蚀较为严重。同一时刻下,3个试片的电偶电流密度和为0,与理论分析相符。分析电偶电流密度数据得到的结果与宏观观测结果完全一致。
图9 8号试片电偶电流密度随时间变化曲线
试验后期,电偶电流密度存在着明显的周期性特征。将8号试片的电偶电流密度局部放大,得到如图9所示的电偶电流密度曲线,可见电偶电流密度存在周期性规律,即电流密度大小先迅速减小随后快速恢复,这一过程出现的周期为210s左右。通过观察摄影机的录像,发现此周期与液滴滴落周期相符,这反映了液滴周期性滴落对电流密度的影响。由此,可以准确得到影响顶部腐蚀问题的液滴滞留时间这一关键参数。
结论
1 新型传感器可以有效地监测到顶部腐蚀问题中液滴的具体位置,得到液滴在试片表面的滞留时间(DRT)。
2 液滴的冷凝过程受腐蚀产物的影响。试验后期304不锈钢与X65管线钢试片表面液滴的冷凝过程完全不同。
3 顶部腐蚀点蚀坑的形成与初始条件下液滴的形核和聚集过程有关。
免责声明:本网站所转载的文字、图片与视频资料版权归原创作者所有,如果涉及侵权,请第一时间联系本网删除。
相关文章
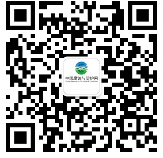
官方微信
《中国腐蚀与防护网电子期刊》征订启事
- 投稿联系:编辑部
- 电话:010-62316606-806
- 邮箱:fsfhzy666@163.com
- 中国腐蚀与防护网官方QQ群:140808414
点击排行
PPT新闻
“海洋金属”——钛合金在舰船的
点击数:7130
腐蚀与“海上丝绸之路”
点击数:5741