导读:本文发现与等轴组织相比,具有“托马斯纤维”型片状马氏体形态的DP钢具有更大的抗裂性。薄板的开裂涉及到裂纹尖端颈缩和材料断裂所需的复杂工作,较好的抗裂性是由于晶片在变形时的排列和其较小的尺寸导致其具有显著的抗损伤形核能力。这一发现为在不影响强度或改变化学成分的情况下优化DP钢的断裂韧性提供了一条新途径。
长期以来,双相(DP)钢因其优异的机械性能而一直用于汽车行业。韧性和延展性之间的良好结合源于延性铁素体(α)和硬质马氏体(α‘)的适当组合。然而,许多DP钢的断裂韧性有限,需要更高的抗裂性以改善可成形性并进一步改善某些关键DP组件的结构性能。因此,开发具有增强抗裂性但又保持高强度-延性平衡的DP钢是很有意义的。
最近,对纤维状DP钢(也称为“ Thomas纤维” DP钢)进行了重新研究,证实了其优异的强度和延展率,但与传统的DP钢相比,其抗裂性也令人瞩目。
在此,比利时鲁汶大学Thomas Pardoen教授研究了以薄板形式存在的“托马斯纤维”DP钢的抗裂性,并与等轴DP钢以及一些厚板的结果进行比较。阐明了“托马斯纤维”与等轴DP钢之间的关系。发现片状组织的微观结构显示出比相应的等轴晶大50%的抗断裂能力。抗开裂性能取决于板材厚度和马氏体体积分数。对于薄板,很大一部分断裂能是由裂纹尖端缩颈引起的。相关研究成果以题“Outstanding cracking resistance of fibrous dual phase steels”发表在金属顶刊Acta Materialia上
论文链接:
https://www.sciencedirect.com/science/article/abs/pii/S135964542100080X
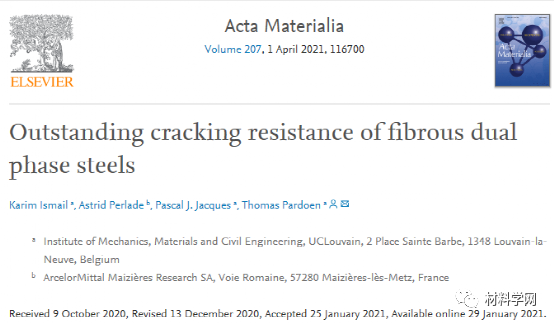
较高的断裂韧性可以与片状组织的较大断裂应变直接相关。实际上,断裂应力与断裂应变成比例,并且对于不同的微结构而言,关于特征空隙间距没有发现显着差异。

图1. 等轴(a)和“托马斯纤维”(c)微观结构,并进行相应的热处理(b)和(d)
图3. 基于2D SEM显微照片的3D重建“ Thomas纤维”微结构中存在的马氏体形态。
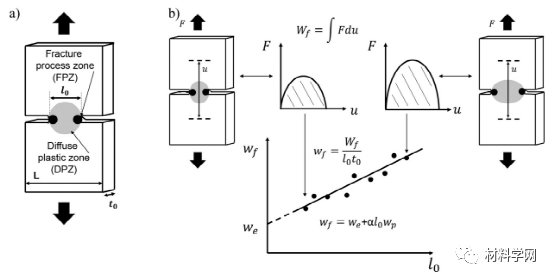
图4. DENT样品的示意图,其中有扩散性塑料区(DPZ)和断裂过程区(FPZ)的图示(a)EWF方法的图示(b)(由参考文献[27]启发而来)。
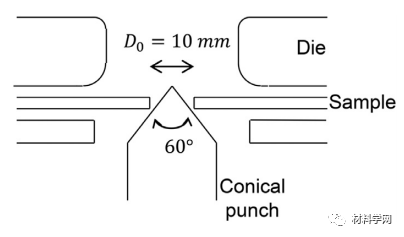
图5.扩孔测试配置。

图6. 破碎的单轴拉伸和DENT试样中的损伤表征程序示意图。
片状组织的较大断裂应变主要源自空隙的成核推迟和空隙生长减少,从而导致较小的空隙体积分数。马氏体薄片具有良好的抗断裂能力,这可能是由于其尺寸较小,并且在大变形时马氏体颗粒沿主加载方向排列。更好的抗裂性导致通过孔膨胀试验测量的拉伸翻边性得到改善,证明了片状DP钢对成形操作的作用。

图7.(a)直至断裂点的薄板情况下不同组织的实验真实应力-真实应变曲线;(b)可放大至缩颈的薄板,以及(c)厚板(数据来自[13])。在(a)中,粗实线表示1毫米厚的纸张,虚线表示2毫米厚的纸张。
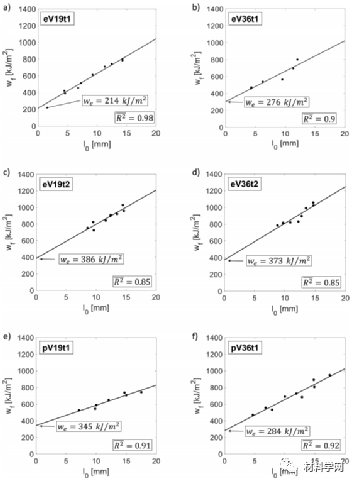
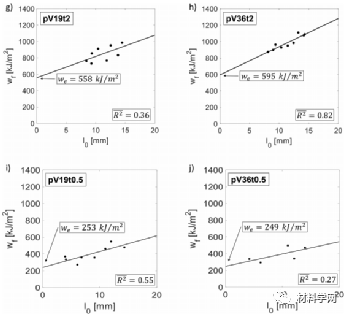
图8. wf作为l0的函数的变化,以及we和线性回归的质量(由图片量化) a)eV19t1,b)eV36t1,c)eV19t2,d)eV36t2,e)pV19t1,f )pV36t1,g)pV19t2,h)pV36t2,i)pV19t0.5,j)pV36t0.5。
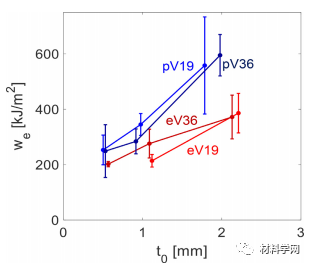
图9. 断裂的基本功we,作初始薄板厚度t0的函数。
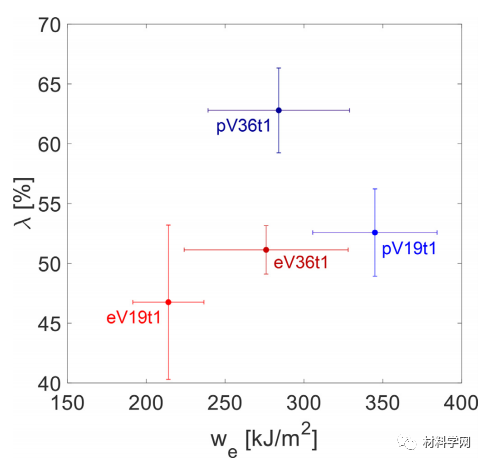
图10. 扩孔率值λ,作为eV19t1,eV36t1,pV19t1和pV36t1微结构的基本断裂功的函数。

图11. 八个薄片微结构的单轴拉伸试样断裂表面的SEM显微照片。
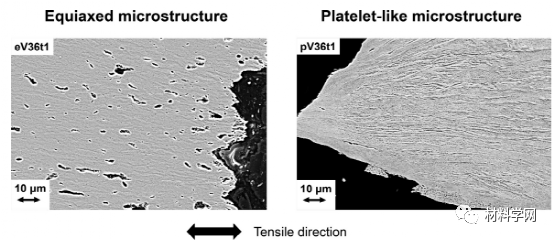
图12. 等轴微结构(eV36t1)和薄片状微结构(pV36t1)的单轴拉伸试样的横截面的SEM显微照片。

图13. (a)断裂的拉伸试样的示意图,指示(b),(c)和(d)的SEM显微照片位于何处。

图14. 对于给定的马氏体体积分数和片材,片状微结构和等轴微结构中的基本断裂功比与DENT试样中平均等效断裂应变的相应比的平方的平方函数厚度。
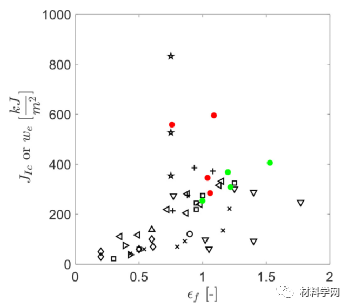
图15.对于各种钢以及其他金属,初始断裂韧度JIc或断裂的基本功,我们作为断裂应变εf的函数。一些片状DP钢(红色和绿色的粗体点)与最坚硬的钢对比。
本研究表明,通过微结构工程,在不影响成分和不损害成本优势的情况下,仍有改善DP钢力学性能的空间。精制的结构可能会在增加强度的同时进一步延迟损伤的发生。
免责声明:本网站所转载的文字、图片与视频资料版权归原创作者所有,如果涉及侵权,请第一时间联系本网删除。
相关文章
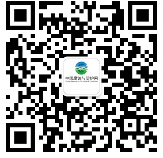
官方微信
《中国腐蚀与防护网电子期刊》征订启事
- 投稿联系:编辑部
- 电话:010-62316606-806
- 邮箱:fsfhzy666@163.com
- 中国腐蚀与防护网官方QQ群:140808414
点击排行
PPT新闻
“海洋金属”——钛合金在舰船的
点击数:7130
腐蚀与“海上丝绸之路”
点击数:5741