碱性锌酸盐镀锌工艺,其镀层外观光亮,具有良好的结合力、低脆性和耐蚀性。它消除了氰化镀锌的毒性,克服了氯化物镀锌对耐腐蚀差和钝化膜在湿热空气中易变色的缺陷。以下对12种最常见故障进行全面分析讲解,希望能给大家带来点帮助:
1.低电流密度区出现黑色或灰色镀层
2.铸铁零件较难沉积上镀锌层
3.镀层呈海绵状
4.镀层结合力差的原因及解决方法
5.沉积速度慢的原因及解决方法
6.镀液中锌含量过快积累和阳极钝化的原因及解决方法
7.镀锌层出现粗糙或粗糙发暗的原因及解决方法
8.镀层钝化膜质量故障(发花、变色、变暗等)
9.锌酸盐镀锌层起泡故障的分析与处理实例
10.镀层有条纹和气流状
11.锌酸盐滚镀锌,滚筒突然发生爆炸
12.锌酸盐镀锌液中锌浓度快速下降
一、低电流密度区出现黑色或灰色镀层
1.原因分析
铅离子污染:当镀锌液中铅离子的含量超过15m9/L时,镀液的分散能力下降,镀层经稀硝酸出光后会出现黑色或灰色条纹。铅离子主要是由劣质锌阳极带人的,为防止铅的污染,锌阳极需用0#锌或l#锌。
铁离子污染:镀液中铁离子含量高达50m9/L,如铁离子含量进一步提高,镀液就会出现胶体絮状物,镀层钝化后会出现紫蓝色,而且镀层容易出现气泡。铁离子主要是由劣质氢氧化钠或工件带人。因此,要选用白色片碱,带赤色的氢氧化钠绝对不可用,工件进入镀槽前应彻底清洗。为调解阴、阳极面积比例,应当使用镍板或镀镍铁板作为阳极。
铜离子污染:镀液中铜离子含量高达20m9/L时,得到的镀锌层粗糙,光亮度降低,且光亮电流密度范围随铜离子含量的增加而逐渐缩小。铜离子主要是由挂勾和洗刷导电铜杠时带入的。
2.解决方法
硫化钠处理:取0.19/L~0.59/L化学纯硫化钠,溶于20倍以上的冷水中,在剧烈搅拌下,缓慢加入到镀液中,加完后继续搅拌20min,使之与镀液中的重金属离子充分反应,生成硫化物沉淀去除。
锌粉处理:取l9/L~39/L锌粉,在剧烈搅拌下缓慢加入镀液中,使之与重金属离子发生置换反应,加完后继续搅拌20min,静止2h后进行过滤,静置时间不宜过长,否则失去处理意义。
低电流电解处理:取镀镍铁板数块作阴极(面积宜大些),以0.1A/dm2~0.2A/dm2的电流密度进行电解处理,处理时间视试镀后情况而定。使用过的镀镍铁板表面的黑色镀层必须在酸中退除,然后方可作阳极使用。该方法的优点是:操作简便,不损耗镀液。
二、铸铁零件较难沉积上镀锌层
1.原因分析
铸铁是含碳量高达2%(质量分数)以上的铁碳合金,材料中的碳只有少量与铁形成固溶体,大多以石墨或渗碳体的形式存在,由于石墨会降低氢的析出电位,从而阻碍了锌的沉积,另一方面铸铁件表面粗糙,含大量缩孔、气孔和砂眼,孔隙率也高,有些工件表面未经加工,覆盖有氧化皮,或经过酸洗而造成过腐蚀,则导致析氢更严重,从而造成锌离子的阴极还原沉积更困难。
2.解决方法
利用喷砂代替强腐蚀:喷砂可以阻止酸洗液渗入疏松内孔中,并可避免发生过腐蚀。
采用闪镀先镀上薄层锌:镀件入槽后用高于正常电流5倍~l0倍的电流密度进行闪镀,使其表面先镀上一薄层锌(此锌层可以提高氢的过电位),然后再用3倍~5倍的电流密度继续加厚。实践证明,以上二种方法同时使用效果会更好。
三、镀层呈海绵状
1.原因分析
当锌酸盐镀锌液中添加剂含量不足时,有可能造成镀锌层结晶粗糙,因为锌酸盐镀锌的添加剂多属表面活性剂,在电沉积过程中,添加剂在很宽的电位范围内吸附,从而减缓镀液中锌离子的放电步骤,提高了阴极极化,使镀锌层结晶细致、光亮。
2.解决方法
镀液中添加剂含量目前尚未见有适用的准确的分析方法,一般是根据生产过程中镀层的质量,凭经验或者霍耳槽试验添加。添加剂不宜过量加入,否则会出现镀层发花,钝化膜发雾,镀层起泡,脆性增大,镀层易变色,结合力降低等故障。
四、镀层结合力差的原因及解决方法
1.原因分析
出现镀层结合力差的原因可能有很多,而且可能是一种情况影响的结果,也可能是多种情况交互在一起引起的。
添加剂添加过量:一般情况下锌酸盐镀锌层的光亮度稍逊于氯化钾镀锌层,有时为了获得更光亮的镀层,就靠多加光亮剂来弥补,结果镀层不但达不到预想的光亮度。而且造成镀层的结合力受到严重影响。
工件镀前在镀槽中停留时间过长:有人认为锌酸盐镀锌溶液是碱性的,把经过前处理的工件挂在镀槽中,待聚够一槽后再送电施镀,这样工件易产生表面钝化,从而影响到镀层的结合力。
镀层过厚:对于镀锌来说,镀层过厚,镀层的内应力和脆性增大,工件边缘部位的镀层出现气泡,脱皮。所以一般镀层厚度宜控制在20μm以内。
镀液表面浮有油污:工件入槽后被镀液表面的油污和光亮剂分解物组成的污物所包围。从而引起镀层脱皮。
工件除油不彻底:有人认为锌酸盐镀锌是碱性的,必定有除油能力,前处理可以马虎一点。镀液虽是碱性的,但当有油污的工件入槽后,在其与碱性物质起作用之前,锌离子即抢先放电析出,锌层沉积在薄层油膜上,结合力降低。
2.解决方法
针对上述原因分析,对于镀层结合力的故障就可以采取相应措施,例如控制镀液中添加剂、光亮剂含量;控制工件在镀槽中不能停留过久;加强零件的镀前处理,保持清洁干净的零件表面;同时注意镀液表面的洁净,随时用厚层手纸吸除镀液表面的油污等。
五、沉积速度慢的原因及解决方法
1.原因分析
出现镀锌层沉积速度慢的原因也有很多,在前面也做过一些分析,如果考虑到实际操作上的各种因素,其原因可能有:前处理不彻底,工件表面覆盖有氧化膜,影响了锌离子的正常沉积;零件导电不良,电流在导线上有消耗,分配到工件表面的电流过小;高碳钢、铸铁等零件表面含碳量高,降低氢的析出电位,使得工件表面析氢加速,造成电流效率降低;零件绑扎过密,镀锌时工件局部遭到屏蔽而导致镀层过薄;镀液的温度偏低,不允许使用正常的电流密度,影响了沉积速度;镀液中氢氧化钠含量偏高,电流效率相应降低;镀液中添加剂含量偏低,影响了镀液的分散能力,造成零件表面镀层局部显得过薄;电流密度偏低影响沉积速度等。
2.解决方法
解决上述故障的方法,就是针对性的采取一些措施,如加强镀前处理,保证零件表面的氧化皮去除干净;注意电镀挂具的导电和槽内分布,保证零件的电流线的分布均匀;保持镀液成分、温度和电流密度处于规范和标准范围内。这样就达到镀锌层沉积的正常速度。
六、镀液中锌含量过快积累和阳极钝化的原因及解决方法
1.故障原因
这种故障产生的原因主要是阳极的问题,而造成阳极快速溶解的原因有:镀液中氢氧化钠含量偏高时,锌阳极化学溶解速度加快,造成镀液中锌离子增加很多,因为锌酸盐镀锌的阴极电流效率是比较低的,锌的实际消耗少于锌阳极的溶解;实际上是锌阳极这种自然溶解而破坏了镀液中氢氧化钠和锌含量的正常比例。
在有些情况下,锌阳极表面出现了阳极钝化现象,虽然锌阳极钝化能增加阴极极化,提高分散能力,但阳极钝化影响了锌离子的溶解,使得镀液中的锌离子得不到补充,电镀沉积速度受到了严重影响。
引起锌阳极钝化的原因有:镀液中氢氧化物浓度过低,阳极面积过小,阳极面积与阴极面积之比应不小于1.5:1否则较易发生钝化。
2.解决方法
分析镀液成分,调整镀液中氢氧化钠的浓度到正常;另外通过控制锌阳极和不溶性镍阳极的比例;在停镀时将锌阳极从槽中取出等措施消除镀液中锌离子增加的问题。同时也能解决锌阳极的钝化问题。
七、镀锌层出现粗糙或粗糙发暗的原因及解决方法
1.原因分析
按正常情况下氧化锌与氢氧化钠的比例为l:(10~12),过高或过低即会出现上述故障。即镀锌层粗糙是氧化锌比例偏低而氢氧化钠比例偏高造成的,这种比例失调还会出现电镀沉积速度缓慢、允许电流密度上限降低、工件表面析氢加重等故障。反过来,氧化锌比例偏高而氢氧化钠比例偏低也会造成镀锌层的粗糙与发暗,这时还会出现工件边缘部位有气泡,沉积速度缓慢,分散能力和深镀能力降低,电流升不上去,镀层结合力差等问题。
2.解决方法
调整上述两种情况的故障,一般在日常维护中既要控制好氧化锌与氢氧化钠的比例,又要考虑到氧化锌与氢氧化钠的实际含量,即使氧化锌的比例偏低,也不直接添加氧化锌,而是调节锌阳极的面积,暂停使用不溶性阳极,溶液中锌含量就会很快上去。当氧化锌含量高了,可以以镀镍铁板代替锌阳极板,添加氢氧化钠至l209/L,这一故障即能很快获得解决。
八、镀层钝化膜质量故障(发花、变色、变暗等)
目前镀锌进行钝化处理的工艺主要低铬彩色钝化和三价铬钝化,在钝化后有时放置一夜或几天时间,钝化膜的表面就会出现雨点状白点,大小不一,钝化膜也变暗变淡,光亮度下降。
1.原因分析
实际上发生这种故障的原因更复杂,可能有镀液的问题;前处理不良的问题;基材有麻点,镀后出光等清洗不良的问题;钝化液成分比例失调的问题;钝化膜老化时间不够的问题;环境的问题,空气中水蒸气、酸雾严重使得钝化膜色泽变化和腐蚀等。
2.解决方法
针对上述可能的原因,逐条采取措施。调整镀液成分到工艺规范,并且对镀液进行锌粉、硫化钠处理,再进行电解处理;加强除油、活化等前处理工序;加强镀后清洗和出光工序;严格控制钝化溶液成分和钝化工艺参数,控制好钝化膜的色彩;加强钝化后老化工艺的控制;改善工作环境,镀后零件尽快入库等。尤其要注意的是钝化后的老化问题,因为热水槽老化温度过高(>70℃),就会使得钝化膜中的六价铬溶解,形成耐蚀性很差的多孔钝化膜。就容易出现镀锌层钝化膜表面的雨点状白点,钝化膜变暗变淡,光亮度下降的故障。严格控制钝化老化工序(60℃),这种故障就可以消除,生产恢复到正常。
其他环节也会出现钝化质量的故障的问题,如某厂碱性锌酸盐镀锌液,低铬钝化的滚镀锌工艺生产线,出现了钝化膜发花,表面有许多大块不规则灰黑色斑块的故障。经分析是由于镀锌后的清洗槽中白色絮状沉淀较多,出光槽溶液呈黄棕色,pH值接近4,这些都可能带来电镀故障,由于清洗不干净和出光液pH高,造成电镀零件表面碱性镀液的清洗不够,出光液的出光作用下降,导致钝化膜发花等故障。通过增加一道热水洗,将出光液pH调至l左右后,故障排除,生产恢复到正常。
九、锌酸盐镀锌层起泡故障的分析与处理实例
首先我们从零件的制备加工检查,没有发现出现起泡的可疑环节,所以重点考虑电镀各个工序的影响。
零件表面的油污,一般是经化学除油、电解除油清除干净。但若操作不当或者除油液成分失调,可能会有少量油珠残留在零件表面,这就可能引起镀锌层的起泡。
零件若酸洗除锈时间过长,可能由于过腐蚀也会引起镀层的起泡。
此外,镀前活化不充分,没有活化,零件表面形成了一层薄氧化膜,也会导致镀层结合力变差而起泡。
因此,碱性锌酸盐镀锌前处理要严格控制。
前处理流程为:化学除油→热水洗→冷水洗→酸洗除锈→2次流动水洗→电解除油→热水洗→流水洗→镀前活化→2次流动水洗→镀锌。
除油液要定期加料;酸洗液、镀前活化液要定期更换,而且要严防铜杂质的危害。
(1)电镀工序中引起镀层起泡的可能因素。
挂具选择不当会引起锌镀层起泡,这一点往往易被人们忽略。一般是用焊锡或铜将挂钩与杆子焊接在一起,再浸塑、浸漆,或用聚氯乙烯薄膜包扎。若包扎破损,焊接处易受电解质腐蚀,腐蚀产物附着在零件表面、零件自上而下便产生带状密集小泡,因此,应经常检查挂具焊接处是否破损以防止挂具腐蚀而引起镀层起泡。
镀液操作或维护不当导致锌镀层起泡。镀液中添加剂含量过高,易夹杂在镀层中使得内应力骤增,导致镀层起泡;镀液中重金属杂质,如铅、铜等含量过高,使锌层中夹杂过多的铅、铜等杂质,镀层与基体结合不良而起泡;光亮剂香草醛加入过多,镀层的光亮性虽好,但脆性增大,导致镀层起泡,此外,操作条件控制不当如温度太低,电流密度太大,也会导致镀层夹杂有机杂质,引起起泡。
镀后钝化工序的影响。镀后出光、钝化操作不当,清洗不彻底,出光液、钝化液残留在镀层内,烘烤老化也容易引起镀锌层起泡。
(2)采取措施,严格控制镀锌工序消除起泡故障。
①生产厂首先把好了原材料关,选用性能优良的锌酸盐镀锌原料和添加剂,并且在添加剂加入镀槽前,先进行霍耳槽实验。
②加强镀锌槽液的维护,严格控制添加剂及光亮剂的补充量,以“少加勤加”为原则,或者根据霍耳槽试验计量补加。
③将掉入镀槽内的零件及时捞出,铜挂钩一律不能浸入镀液中。
④检查锌阳极的纯度,采用0号锌或1号锌,不用2号锌。
⑤严格按锌酸盐电镀锌工艺规程,控制电流密度和温度,冬季适当加温至15℃以上,并尽可能减少添加剂及光亮剂的用量。
⑥严格控制零件镀锌层厚度,尤其是零件边角的厚度太厚,特别容易发生镀层起泡。
⑦定期对镀液中有机物和重金属杂质进行大处理(加人lmL/L过氧化氢,搅拌30min,将镀液加温至60℃~70℃,再加入专用活性炭59/L~l09/L,锌粉19/L~29/L,充分搅拌30min~60min,静置4h,过滤,调整镀液成分,即可试镀),保证镀锌溶液处在一个好的工作状态。
⑧加强镀后处理工序,加强各道工序的漂洗,经常更换浸泡用热水,可大大减少因后处理不当而产生的起泡现象。
⑨严格控制老化温度,避免镀锌层与基体因热胀冷缩差异太大而起泡。
有些情况下,不一定是电镀工序过程出现了镀层起泡的现象,电镀生产的周围环境也可能引起电镀层的起泡。如某厂碱性锌酸盐镀锌每年4月份~5月份总是发生镀锌层严重起泡的故障,而且开始找不出原因,只得每年停产一个多月。后来通过观察分析发现,当镀液表面浮有一些微小的丝状物时,镀层起泡就严重,而当时的季节正是厂区周围梧桐树的开花期,其花瓣呈微小丝状的物质飘荡,或多或少落人的镀锌槽。当采取措施阻挡了花瓣微小丝状物的影响后,这种镀锌层起泡的故障就消除了。这说明出现电镀故障,有时候除了电镀工艺生产之外,还要从周围的环境可能的影响考虑。
十、镀层有条纹和气流状
1原因分析及处理方法
(1)阴极电流效率低
锌酸盐镀锌液,当阴极电流密度在1A/dm2、温度在20℃左右时,阴极电流效率约为85%左右;当阴极电流密度在2A/dm2时,同等温度下,阴极电流效率低于80%,若继续增大阴极电流密度,则阴极电流效率将进一步降低。由于阴极电流效率低,阴极大量析氢,致使镀层产生气流、条纹。若镀液的温度低,阴极电流效率会更低,该现象将更加明显处理方法:a.合理设定电流密度,参考值如下
温度阴极电流密度
20℃以下0.8A/dm2
20℃以上1.5A/dm2
30℃左右1.5~2A/dm2
b.控制镀液在15℃以上;
c.适量加入表面活性剂,加速氢气析出
十一、锌酸盐滚镀锌,滚筒突然发生爆炸
1.原因分析
(1)阴极大量析氢
锌酸盐滚镀锌的阴极电流效率较低,一般在70%~80%,电镀过程中产生许多氢气,而这些氢气又不能及时通过滚筒眼子排出,所以电镀一定时间后,滚筒内产生大量氢气聚积。如果滚筒不是全浸式的,则筒内同时有空气存在。此外,如果阳极面积小,阳极电流密度大,使阳极发生钝态,产生大量氧气。氢气、氧气和空气的混合,并成一定的体积比(爆炸极限),使滚筒爆炸具备了必要的条件。
锌酸盐镀锌液的溶液电阻较大,当滚镀时间一长,镀液温度升至40℃以上。温度高,在滚镀中摩擦易产生火花,火花是引起爆炸的必要条件。
如果上述两个条件同时具备,即发生爆炸。
2.解决方法:
a.采用全浸式的滚筒电镀;
b.若使用半浸式滚筒电镀,每隔30min停止电镀一会,让滚筒聚积的气体散发出去,然后再继续电镀。
十二、锌酸盐镀锌液中锌浓度快速下降是什么原因?如何处理?
1.原因分析:
①苛性碱含量不足,因而锌酸盐的水解作用加强,氢氧化锌沉淀;
②阳极钝化与阳极电流效率过低。
2.解决方法:
①向电解液中加苛性碱,并使氧化锌含量增加到配方中规定浓度;
②清理阳极并增大其面积。
免责声明:本网站所转载的文字、图片与视频资料版权归原创作者所有,如果涉及侵权,请第一时间联系本网删除。
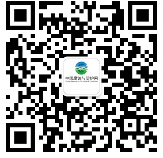
官方微信
《腐蚀与防护网电子期刊》征订启事
- 投稿联系:编辑部
- 电话:010-62316606-806
- 邮箱:fsfhzy666@163.com
- 腐蚀与防护网官方QQ群:140808414