摘要
针对化工领域,阐述了Si-Fe涂层的制备工艺现状,并对其抗氧化机制及工业化应用发展进行了说明;对于高温防护领域,重点综述了Si-Mo、Si-Zr两种高温防护涂层的研究现状,并介绍了不同元素对涂层抗氧化性能的合金化改善效果及其抗氧化机制。相对于单层涂层,双层或多层复合硅化物涂层具有极佳的可设计性,并能够兼顾耐热性能与结合强度的要求,避免涂层与基体间热膨胀失配、元素扩散等缺陷的产生,举例说明了其设计理念及性能优势。展望了难熔金属硅化物涂层的发展方向,为其工程应用提供理论支持。
关键词: 硅化物 ; 抗氧化性能 ; 合金化 ; 复合涂层
随着空天装备、核能工业、船舶工业等特殊领域的发展,对高温结构材料的性能要求变得极为苛刻,如航空发动机、燃气轮机等动力装备,不仅要求材料具备良好的高温力学性能,还要求其具备极佳的高温抗氧化性能和抗热腐蚀性能[1,2]。目前,改善材料高温性能的主要途径分为两种:合金化技术和表面涂层保护技术[3,4]。合金化技术虽能有效提高高温合金的高温抗氧化性能,但其往往会导致合金的力学性能降低。此外,由于大多数金属元素与C之间易形成碳化物或导致碳基体石墨化[5,6],严重损伤了碳基体的性能,故难以很好地应用于碳基新型高温材料。表面涂层保护技术不仅适用于目前所有的高温结构材料,且可在兼顾基体力学性能的同时,使其获得更为优良的高温力学性能和抗氧化性能,是有效改善高温结构材料抗氧化性能与抗热腐蚀性能的最常用手段[3,4]。目前,常用高温涂层主要分为以下几种:(1) 耐热合金涂层[1],主要包括Ni、Co、Cr、Al等元素,使用温度一般低于900 ℃;(2) 贵金属涂层[7],主要以Ru、Ir、Rh等铂族金属为主,其造价极其昂贵,难以大规模应用;(3) 铝化物涂层[1,8],抗氧化性能良好,但高温力学性能较差;(4) 硅化物涂层[4],抗高温腐蚀与氧化性能优异、高温化学稳定性较好、高温力学性能良好。较前3种高温涂层,硅化物涂层拥有较长的工程应用历史。早在20世纪60~70年代,硅化物涂层已在航空航天领域展开商业化生产及应用,如航天器的热盾隔热瓦、涡轮发动机叶片和尾喷管等部件表面均涂覆了不同性能的硅化物涂层。
在众多Si化物涂层中,Si-Fe化合物制备工艺简单,并能够抵抗沸腾硫酸的侵蚀,在化工领域应用潜力巨大;Si-Mo系化合物不仅在电热材料 (作为发热元件) 领域应用十分广泛,而且高温力学性能优异,在空天装备领域更是受到研究人员的重点关注;鉴于良好的物理性能和高温性能,Si-Zr系化合物在核工业领域应用前景十分广阔。结合不同工业领域的发展,总结相关文献,本文重点论述了上述3种硅化物涂层以及双层或多层复合硅化物涂层的发展历程与现状,并展望了未来硅化物涂层材料的重点研究发展方向。
1 Si-Fe系抗氧化涂层
Si-Fe系金属间化合物因其优异的物理性能在功能材料方面具有广阔的商业应用[9,10],近年来受到研究人员的广泛关注。更值得关注的是,Si-Fe化合物中Fe3Si相因其独特的DO3型结构,具有硬度高、耐磨性好、抗氧化等优良特性[11-13],在高温防护涂层方面具有较大的应用潜力。目前,Fe3Si涂层制备方法主要有以下几种:(1) 化学气相沉积法,早在1993年日本NKK便成功开发了CVD连续渗硅生产线,其制备速率高、覆盖能力强、涂层质量好,但工艺及设备比较复杂,且易产生HCl等腐蚀性很强的气体副产物;(2) 粉末包埋法,在上世纪90年代,麻启承等[14,15]通过固态包埋法在45钢表面制备了硬度为HRV 530~550的多孔Fe3Si涂层,并实现了涂层孔隙率的可控化。虽然多孔型涂层可通过孔隙贮油来提高涂层的耐磨性,但其高温抗氧化性能大大降低。王金兰等[16,17]以Si-Fe合金为主渗剂,采用粉末包埋法实现了无孔Fe3Si涂层的制备,但涂层在900 ℃保温60 h便出现剪切裂纹,导致其抗氧化防护作用丧失。此外,固态包埋法制备温度高达1050~1150 ℃,保温时间长,成本高、效率低,难以实现大规模工业化应用;(3) 熔盐法,此工艺比粉末包埋法保温温度低,且涂层生长效率高[4]。笔者曾对熔盐法制备硅化物涂层的工艺进行了研究,相关结果[18]显示,900 ℃下保温3 h即在AISI 304不锈钢表面成功制备了厚约250 μm的涂层;文献[16,17,19]采用粉末包埋法在≥1000 ℃保温4 h仅在基体表面获得了不足100 μm的涂层。此外,激光熔覆法、等离子喷涂法、磁控溅射法等也能制备质量较好的涂层,但设备昂贵,且适用范围较窄,仅适用于平板及块状等规则形状的部件,本文不再详述。
Tatemoto等[20]采用熔盐法在Mo、Nb、Cr等难熔金属表面成功制备了致密无孔、与基体结合良好的渗Si层,且制备温度仅为700~900 ℃,明显低于固态包埋法。受此启发,笔者曾以NaCl-KCl-NaF (摩尔比为2∶2∶1) 低熔点盐体系为载体,以Na2SiF6-Si (摩尔比为8∶2) 作渗硅剂,在AISI 304不锈钢表面成功制备了与基体结合牢固且致密的Fe3Si涂层,其涂层硬度高达700 HV,且渗硅修饰后试样的名义屈服应力明显提高[21,22]。同时,还对渗Si过程和机理进行了分析,如图1所示。熔融盐中,Si粉在NaF和Na2SiF6作用下与Si4+反应形成Si2+,Si2+与不锈钢基体反应形成Fe3Si涂层,且可通过改变渗Si剂成分,控制涂层中Si的含量[23]。在上述基础上,进一步对Fe3Si涂层的高温抗氧化性能 (900 ℃下循环氧化100 h) 进行了研究,其氧化膜截面形貌及成分分布如图2所示,可见氧化膜明显分为两层,内层 (区域B) 氧化产物以SiO2和Cr2O3为主,外层以Fe2O3为主。经分析可知:900 ℃下,Si发生上坡扩散在涂层表面形成了SiO2保护膜,一方面阻止了O的深度扩散,另一方面阻止了基体中Cr的扩散,使渗硅后的AISI 304不锈钢在900 ℃下仍表现出良好的抗氧化性能[24,25]。
图1 渗硅层的形成机理[17]
图2 Fe3Si渗层900 ℃氧化100 h后氧化膜截面SEM像及元素线分布[25]
为进一步提高Fe3Si涂层的高温性能,研究人员开始尝试对其进行合金化处理。研究[26]表明,适量Al的引入能够很好地改善Fe3Si相的高温抗氧化性能,这主要是因为在涂层表面优先形成Al2O3阻止了Si、Fe扩散,从而有效抑制了短程扩散通道的产生。需要说明的是,Ni、Co、Cr等难熔金属元素的引入虽能提高Fe3Si相熔点,但对其热稳定性的改善效果不佳[27]。此外,随着陶瓷等高温材料的制备技术日趋成熟,近年来对Fe3Si相高温性能改善的研究逐渐减少。
2 Si-Mo系抗氧化涂层
作为难熔金属的一种,金属Mo具有熔点高、高温强度高、线膨胀系数小等特点[28]。通过热压烧结、自蔓延合成、机械合金化等制备方法,在不同工艺条件下Mo与Si可合成MoSi2、Mo5Si3、Mo3Si等多种高熔点化合物。其中,MoSi2同时兼备金属和陶瓷的双重特性,即模量高、高温抗氧化性能和抗热冲击性能好,是一种非常理想的高温涂层材料[29]。但值得注意的是,MoSi2本身缺陷使其使用范围大大受限。在低温 (450~550 ℃) 工况下,MoSi2表面难以形成完整的玻璃态SiO2膜,MoO3大量挥发,致使其出现“Pesting”效应而发生失效;高温下 (>1200 ℃) 次表面的Mo5Si3贫化和鳞石英SiO2向方石英SiO2的转变使得MoO3的扩散及蒸发速率明显升高,导致其在高温结构材料方面的预期服役温度仅为1200 ℃[30]。为此,向Si-Mo涂层中添加Al、B、Cr等元素使其合金化,可有效改善涂层的抗氧化性能。目前,Si-Mo涂层较为常用制备方法以热喷涂法为主,其主要包括等离子喷涂、激光熔覆、电热热源喷涂、气体燃料火焰喷涂等几种[31]。但对于三元或多元Si-Mo-X(-X) 涂层的制备,目前多采用热喷涂-包埋法等复合工艺。目前,以Al、B合金化效应研究较多,并取得了诸多成果。
2.1 Si-Mo-Al涂层
轻金属Al性质活泼,在常温下便可与O反应形成厚约0.1 nm的致密、连续Al2O3薄膜,且高温 (>1200 ℃) 下Al2O3结构稳定,故Al的添加有望抑制Si-Mo涂层的“Pesting”效应并提高其高温抗氧化性能。Hou等[32]以镍基高温合金为基体,采用电热爆炸超高速喷涂技术在其表面分别制备了Mo-Si涂层和Mo-Si-Al涂层,并分析比较了二者不同温度下的抗氧化性能,涂层质量变化曲线如图3所示。研究表明,500 ℃热暴露840 h后Mo-Si-Al涂层失重仅为0.5 mg/cm2,与Mo-Si涂层相比,失重率降低了70%左右,“pesting”现象明显被抑制。其原因主要有以下两个方面:首先,Al2O3吉布斯自由能低于SiO2,中低温 (500~900 ℃) 条件下涂层表面率先形成Al2O3薄膜,有效降低了MoO3的挥发速率;其次,Al2O3形成时体积膨胀率小于SiO2[33],减小了晶界处的残余应力,一定程度上避免了引起“pesting”效应的裂纹的萌生与扩展。此外,Hou等[34]进一步研究了Al含量 (摩尔分数分别为0%,15.3%,22%,29.3%) 对Mo-Si-Al涂层组织结构和高温抗氧化性能的影响,结果发现,随着Al含量的升高,涂层晶粒尺寸由0.5 μm逐渐增大2 μm,Al含量为15.3%的涂层在1100 ℃下抗氧化性能最优。Liu等[35]则通过爆炸喷涂-包埋法制备了多相Mo-Si-Al涂层,即:外层为Mo(Si,Al)2相,中间主要为Mo5(Si,Al)3和Al8Mo3两相结构,而内层为AlMo3相;1250 ℃氧化条件下,多相Mo-Si-Al涂层发生以下反应:
图3 不同温度下Si-Mo与Si-Mo-Al涂层氧化质量变化[32]
但由于Al2O3标准生成能仅为-792.191 KJ/mol O2,故多相涂层首先消耗Al原子在其表面形成Al2O3薄膜并形成孔洞缺陷,如图4所示,经30 h氧化后其次表面形成Mo5(Si,Al)3相及孔洞。此外,1200~1500 ℃条件下Mo-Si-Al涂层表面Al2O3薄膜厚度可达30 μm,明显大于厚约10 μm的SiO2薄膜[30],可防止产生因鳞石英SiO2相变而贯穿氧化层的裂纹,从而提高了涂层的抗氧化性能[32,36]。
图4 1250 ℃不同氧化时间下Mo-Si-Al涂层截面BSE形貌[35]
2.2 Mo-Si-B涂层
Mo-Si-B合金因其优异的高温抗氧化性能和力学性能,在高温材料应用领域占有重要的地位。同样,在高温涂层开发及应用方面也具有极大的应用潜力[37,38]。Pang等[39,40]通过爆炸喷涂-包埋复合工艺在Nb-Si合金表面制备了由多相组成的复相涂层,涂层组织及成分如图5a所示,由内向外依次为Mo、MoB、MoSi2相,且各相之间呈冶金结合,无明显孔隙缺陷。在1250 ℃下氧化100 h后,MoB相高温下分解并与O形成B2O3相,B2O3相则降低了高温下SiO2的粘度,从而使SiO2薄膜自愈合速率提高,如图5b和c所示,氧化层内层出现了致密且连续的B2O3-SiO2涂层,故Mo-Si-B涂层表现出良好的高温抗氧化性能。此外,通过对Mo-Si-B涂层的热稳定性研究[41]可知,其高温抗氧化性能与Si含量及B/Si比紧密相关,即Si含量高于25% (原子分数),B/Si比不低于0.25,Mo含量在50%~60% (原子分数),涂层表现出最佳的高温抗氧化性能。Perepezko[42]研究表明,适当成分的Mo-Si-B涂层不仅具备良好的高温自修复性,而且拥有极佳的抗高温湿氧化能力。Deng等[43]则研究了Mo-Si-B涂层微观结构与其抗氧化性能二者之间的关系:与Mo3Si/Mo5SiB2共晶相比较,Mo5SiB2枝晶相具有更好的高温抗氧化性能。
图5 Mo-Si-B涂层及1250 ℃氧化100 h后截面形貌[40]
由前述内容可知,Al和B的引入均能有效改善Mo-Si系涂层的高温抗氧化性能。在此基础上,Kiryukhantsev-Korneev等[44]进一步对比了Mo-Si-B和Mo-Al-Si-B涂层在不同温度的抗氧化效果。其结果表明:在1200 ℃下,Mo-Si-B涂层表面SiO2薄膜生长速率明显高于Mo-Al-Si-B涂层;氧化温度为1200~1700 ℃时,Mo-Al-Si-B涂层表面生成Al2O3-SiO2双相薄膜,但Al的扩散导致涂层孔隙率增加,抗氧化性能降低;1700 ℃下涂层完全氧化失效,而Mo-Si-B涂层仍具有相当长的抗氧化服役寿命。可见,Al、B二者之间并不存在积极的协同作用,故目前暂未见有关于Mo-Al-Si-B涂层实际工程应用的报道。
3 Si-Zr系抗氧化涂层
作为一种高熔点难熔金属,Zr的硅化物ZrSi2和氧化物ZrO2熔点分别高达1925和2700 ℃[45],有望满足新一代高超音速飞行器的高温性能要求。Yeom等[46]采用磁控溅射法在Zr合金表面成功制备了Zr-Si涂层并对其抗氧化性能进行了研究,可知在高温下 (1200 ℃) Zr-Si涂层表面形成了致密连续的SiO2和ZrO2多相薄膜,有效地阻止了氧的扩散,同时Zr-Si涂层在热冲击作用下无球化结晶、裂纹等缺陷的产生。
为进一步提高Zr-Si涂层的热稳定性与抗氧化性能,学者们多通过Ta、Al、C、Ti等元素的微合金来实现。目前,Zr-Si-X多元涂层的制备多通过复合涂层制备系统来完成,其制备过程如图6所示[47],分别以Zr、Si为靶材,并向设备中通入既定比例的N2-Ar混合气体,起到保护、反应的双重作用;中间基体按照一定速率旋转,保证涂层的组织与成分均匀。该方法具有使用范围广,基体形状不受限制,生产效率高等优点。
图6 AIP-溅射复合镀膜系统原理图[47]
3.1 Si-Zr-C涂层
殷小玮等[48]采用气相沉积法制备了Zr-Si-C复合涂层,涂层呈多相结构:由表面至基体依次为ZrC1-x、Zr2Si-ZrC1-x、ZrC等相。Xu等[49]对蒸镀-原位反应法在碳材料表面制备ZrC-SiC复相涂层的过程进行了探究,涂层生成过程如下式[50]:
蒸镀温度高于1410 ℃时,Si蒸汽与C基体反应形成SiC薄膜,随着温度升高涂层厚度增加;当蒸镀温度超过1800 ℃时,ZrC比SiC的生成自由能更低,一旦Zr蒸汽出现 (≥2100 ℃),SiC与Zr反应形成ZrC。此外,从其烧蚀实验可知,ZrC骨架主要起到抵抗热侵蚀的作用,而SiC氧化形成SiO2薄膜弥补涂层微观裂纹。Huo等[51]则通过原位合成法在C/C材料表面进一步制备了SiC-ZrC-Al2O3复相涂层,在2.4 MW/m2的热负荷工况下涂层有效寿命达60 s以上,是ZrC单相涂层[52]的两倍。
3.2 Si-Zr-N涂层
对于Si-Zr涂层的改性,除了C外,N的引入同样倍受研究人员的关注。Si-Zr-N涂层显微硬度可达36 GPa[53],且具有良好的热稳定性,700 ℃下仍能保持其室温显微硬度和组织结构[54]。目前,关于Si-Zr-N涂层组织与性能的研究已取得诸多成果。相关研究表明[55],Si-Zr-N涂层的高温抗氧化性能与其相组成密切相关,如图7所示,即:当涂层中含有56%~57% (体积分数) Si3N4相时,1300 ℃下涂层无明显质量变化。这主要有以下两方面原因:一方面Si3N4、ZrN等高温稳定相未完全晶化,仅存在少量被SiO2及SiOxNy等相填充的晶界,有效抑制了O的扩散;另一方面高温稳定相1300 ℃下与O2反应形成厚约115 nm的ZrO2-ZrSiO4-SiO2多相致密氧化层,阻止了氧化过程的继续,抗氧化性能明显优于Mo-Si-N涂层[56]。但值得注意的是,ZrN相与Si3N4相润湿性较差,Si-Zr-N涂层力学性能反而低于ZrN单相涂层[57]。为进一步改善Si-Zr-N涂层的性能,科研人员探讨了Si含量对涂层组织与性能的影响。Choi等[47,58]采用阴极电弧沉积技术制备了不同Si含量的Si-Zr-N涂层,并对其室温组织结构与性能进行研究,结果表明:随着Si含量的升高,Si-Zr-N涂层逐渐由晶态结构转变为纳米非晶态,Si原子分数为5.8%时涂层Young's模量和硬度达到最大值,摩擦系数则降至最低。但是,涂层力学性能因制备工艺的不同而存在明显差异。Wu等[59,60]利用磁控溅射技术在Si晶片表面制备了0~20.9% (原子分数) Si含量的Si-Zr-N涂层,其结果表明:Si含量达1.8%~1.9%时Si-Zr-N涂层模量和硬度最大;且随着Si含量的升高,涂层结构逐渐由柱状晶转变为等轴晶。另外,更为值得关注的是,Si-Zr-N涂层组织结构对其高温抗氧化性能和高温耐磨性能起着决定性的作用,500 ℃柱状晶结构涂层的磨损率仅为1×10-4 mm3/Nm,远远低于非晶态涂层[61],但非晶态涂层的抗氧化性能明显优于柱状晶结构涂层[62]。值得一提的是,1300 ℃氧化气氛下Si-Zr-N涂层的抗氧化性能明显优于Si-Zr-W涂层,且氧化层厚度仅为Si-N-Ta涂层的1/4,与Si-Mo-N相比也表现出更为优异的高温抗氧化性能[54,56]。
图7 1300 ℃空气中退火Zr-Si-N涂层的热重曲线[55]
4 双层或多层复合Si化物涂层
尽管上述多种Si化物涂层均具有良好的高温性能,但涂层与基体之间往往存在模量匹配度差、热膨胀系数差异大、元素互扩散等问题,热循环工况下涂层易发生开裂、剥离等失效。对此,学者们受复合材料可设计特性的启发,希望通过双层或多层复合涂层体系的构建解决上述问题。
近年来,相关学者针对不同结构的双层或多层复合涂层的制备及其性能进行了大量研究。Riedl等[63]采用阴极电弧/溅射沉积技术制备了厚约0.35 μm的Ti-Al-N/Mo-Si-B复合涂层,通过对其高温性能研究发现:Ti-Al-N/Mo-Si-B复合涂层周期为37 nm (Ti-Al-N和Mo-Si-B单层分别厚31和6 nm),其抗氧化性能明显优于其他周期涂层,且Ti-Al-N涂层在1000 ℃下仍具备良好的力学性能。此外,涂层结构对其残余热应力的大小也起着决定性作用[64],即:随着双层循环厚度的逐渐减小,残余热应力由-5.4 GPa下降至-2.75 GPa,双层厚度≤130 nm时涂层与基体结合良好,无开裂、剥离等失效现象出现。黎海旭等[65]采用电弧离子镀膜技术在硬质合金表面制备了厚约2.8 μm的TiSiN/AlCrN涂层,内层AlCrN相与基体形成扩散-冶金结合[66],结合力达到了83 N;外层TiSiN相不仅具有良好的高温稳定性,且其高温摩擦系数与室温摩擦系数基本相同。
针对C/C复合材料的抗氧化防护,Savage[67]提出了一种由内至外分别为过渡层、阻挡层、密封层、耐烧蚀层的四层涂层设计理念。根据此理念,郭海明等[68]通过化学气相沉积法-料浆涂刷法复合工艺在C/C复合材料表面制备了TiC/SiC/ZrO2-MoSi2复合涂层,其中TiC为粘接层,保证涂层与基体结合良好并阻止二者间元素互扩散[69];SiC为氧阻挡层,有效阻止O原子的侵入;ZrO2-MoSi2为外耐烧蚀层,有效封填SiC层裂纹并防止液态SiO2的挥发。虽然TiC/SiC/ZrO2-MoSi2涂层在1300 ℃表现出良好的抗氧化性能,但与单涂层相比[70,71],没有太大的工艺或性能优势。因此,科研人员开始摒弃固定的四层设计理念,开始重视双层或多层涂层高温性能的提升。鉴于SiC、ZrC与C/C材料热膨胀系数较为接近且阻隔性优良,目前多以二者为中间过渡层[72-76],在此基础上制备双层或多层高温涂层。Huo等[51]采用原位合成技术在C/C复合材料表面制备了SiC/Si-Zr-Al双层涂层,内层SiC涂层不仅解决了SiC-Zr-Al涂层与基体二者间的热膨胀系数失配现象,增强了界面结合力,同时还有效阻止二者间元素互扩散的发生。Feng等[77]则采用两步包埋法在C/C复合材料表面制备了厚约200 μm的ZrB2-CrSi2-Si/SiC复合涂层,中间层SiC相有效改善了涂层与基体间的热力学相容性,而外层ZrB2-CrSi2-Si复相高温下形成Zr-Cr-Si-O复合玻璃相,有效阻止了O原子的扩散和孔洞的产生,2300 ℃下涂层有效防护时间长达90 s。
5 总结与展望
Si-Fe涂层中不仅低温抗氧化性能优良、工艺成本低,且能很好地适用于高温合金、不锈钢等多种金属材料的高温防护,在石油化工领域具有极大的应用潜力,商业化价值较高;Si-Mo化合物不仅在热电材料领域应用广泛,且在高温防护领域占有重要位置,Al、B等的引入不仅能有效改善系涂层的低温“pesting”效应,同时提高了涂层的高温抗氧化性能,极大地拓展了Si-Mo系涂层的应用范围;作为新一代高温防护材料,Si-Zr系涂层在宇航科技领域应用潜力极大,且可通过C、N元素的添加进一步提高其高温性能,甚至有望替代Ta等贵金属并实现工程化应用。双层或多层复合涂层在很好地解决涂层与基体间相容性差问题的同时,保证了涂层性能更为充分地发挥。但复合涂层制备工艺复杂,生产成本高,如何经济、合理地构建涂层结构体系是复合涂层制备技术的核心。此外,在航空航天等特种领域的2200~3000 ℃超高温环境下,无论是单层Si化物涂层还是多层复合Si化物涂层,其防护类型均为瞬时寿命,大大限制了飞行器性能的提高。因此,如何提高涂层超高温条件下的防护能力成为目前Si化物涂层的重点研究方向。
参考文献
1 Committee on Coatings, National Material Advisory Board, Translated by Jin S. High Temperature Oxidation Resistant Coatings [M]. Beijing: Science China Press, 1980: 9
1 Committee on Coatings, National Material Advisory Board著, 金石译. 高温抗氧化涂层 [M]. 北京: 科学出版社, 1980: 9
2 Kolometsev Π Τ, Translated by Ma Z C. Heat Resistant Diffusion Coating [M]. Beijing: National Defense Industry Press, 1988: 119
2 Kolometsev Π Τ著, 马志春译. 耐热扩散涂层 [M]. 北京: 国防工业出版社, 1988: 119
3 Liu F L, Li J G, Luo G X. The features and main progress of modern aeronautical surface protective technology [J]. Aviat. Eng. Maint., 1999, (5): 37
3 刘凤岭, 李金桂, 骆更新. 现代航空表面防护技术的特点及其主要进展 [J]. 航空工程与维修, 1999, (5): 37
4 Yi D Q, Liu H Q, Wang B. Metal Silicide [M]. Beijing: Metallurgical Industry Press, 2012: 378
4 易丹青, 刘会群, 王斌. 金属硅化物 [M]. 北京: 冶金工业出版社, 2012: 378
5 Galyshev S, Gomzin A, Musin F. Aluminum matrix composite reinforced by carbon fibers [J]. MaterialsToday Proc., 2019, 11: 281
6 Shirvanimoghaddam K, Hamim S U, Akbari M K, et al. Carbon fiber reinforced metal matrix composites: Fabrication processes and properties [J]. Composites, 2017, 92A: 70
7 Wei Y, Chen J L, Hu C Y, et al. Research development of precious metals for ultra-high temperature applications [J]. Prec. Met., 2013, 34(): 122
7 魏燕, 陈家林, 胡昌义等. 贵金属高温材料的研究及应用进展 [J]. 贵金属, 2013, 34(): 122
8 Zhang G Y, Zhang H, Zhang H A, et al. Progress in preparation and application of corrosive resistance coating for aerospace superalloys [J]. Mater. Rev., 2006, 20(5): 59
8 张光业, 张华, 张厚安等. 航空用高温合金防护涂层的研制及其应用的新进展 [J]. 材料导报, 2006, 20(5): 59
9 Hua A, Pan D S, Li Y, et al. Fe3Si-core/amorphous-C-shell nanocapsules with enhanced microwave absorption [J]. J. Magn. Magn. Mater., 2019, 471: 561
10 Zhang M, Li Z J, Wang T, et al. Preparation and electromagnetic wave absorption performance of Fe3Si/SiC@SiO2 nanocomposites [J]. Chem. Eng. J., 2019, 362: 619
11 Zhou Q, Jia J G, Zhao H S, et al. Oxidation resistance at high temperature of Fe3Si intermetallic [J]. J. Aeronaut. Mater., 2011, 31(2): 72
11 周琦, 贾建刚, 赵红顺等. Fe3Si金属间化合物高温抗氧化性能研究 [J]. 航空材料学报, 2011, 31(2): 72
12 Jia J G, Lv J J, Ma Q. Tribological properties of Fe3 Si under dry friction and water lubrication [J]. Tribology, 2008, 28: 299
12 贾建刚, 吕晋军, 马勤. Fe3Si金属间化合物在干摩擦及水润滑条件下的摩擦学性能研究 [J]. 摩擦学学报, 2008, 28: 299
13 Murakami T, Hibi Y, Mano H, et al. Friction and wear properties of Fe-Si intermetallic compounds in ethyl alcohol [J]. Intermetallics, 2012, 20: 68
14 Ma Q C, Li C S, Wu S Q, et al. Study on the wear-resisting character of porous siliconizing coatings on carbon steel [J]. J. East China Univ. Sci. Technol., 1992, 18: 323
14 麻启承, 李春树, 吴圣清等. 碳钢多孔渗硅层耐磨性的研究 [J]. 华东化工学院学报, 1992, 18: 323
15 Ma L P, Ma Y X, Ma Q C. Study on the pore formation in the siliconized layer of carbon steel [J]. Shanghai Met., 1999, 21(2): 54
15 麻莉萍, 麻云新, 麻启承. 碳钢渗硅层组织中孔隙的形成原因研究 [J]. 上海金属, 1999, 21(2): 54
16 Wang J L, Luo X M, Chen K M, et al. Study on fine structure of pack cementation siliconizing layer on surface of Cr18Ni9 austenitic stainless steel [J]. Hot Work. Technol., 2008, 37(2): 57
16 王金兰, 罗新民, 陈康敏等. Cr18Ni9奥氏体不锈钢表面粉末渗硅层精细结构研究 [J]. 热加工工艺, 2008, 37(2): 57
17 Wang J L. Research on siliconized layer and high temperature corrosion capability of austenitic stainless steel [D]. Zhenjiang: Jiangsu University, 2008
17 王金兰. 奥氏体不锈钢渗硅及其抗高温腐蚀性能应用研究 [D]. 镇江: 江苏大学, 2008
18 An L. Preparation and characterization of Fe3Si based transition-metal silicide layer and nanocomposite powders [D]. Lanzhou: Lanzhou University of Technology, 2011
18 安亮. Fe3Si基过渡金属硅化物渗层及纳米复合粉体的制备与表征 [D]. 兰州: 兰州理工大学, 2011
19 Cai H. Microstructure and high temperature oxidation resistance properties of packing Al and Al-Si cementation on TA15 alloy [D]. Harbin: Harbin Institute of Technology, 2017
19 蔡槐. 钛合金包埋渗铝及硅铝共渗层组织结构与高温抗氧化性能 [D]. 哈尔滨: 哈尔滨工业大学, 2017
20 Tatemoto K, Ono Y, Suzuki R O. Silicide coating on refractory metals in molten salt [J]. J. Phys. Chem. Solids, 2005, 66: 526
21 An L, Ma Q, Jia J G, et al. Preparation of Fe3Si type transition-metal silicide layer deposited on AISI 304 stainless and its mechanical property [J]. Hot Work. Technol., 2011, 40(22): 134
21 安亮, 马勤, 贾建刚等. AISI 304不锈钢表面Fe3Si型硅化物渗层制备及其力学性能 [J]. 热加工工艺, 2011, 40(22): 134
22 An L, Jia J G, You S J, et al. Microstructure and properties of silicide layer deposited on 0Cr18Ni9 stainless steel by siliconizing in molten salt [J]. Trans. Mater. Heat Treat., 2011, 32(3): 144
22 安亮, 贾建刚, 尤少君等. 0Cr18Ni9钢表面熔盐法渗硅层的组织与性能 [J]. 材料热处理学报, 2011, 32(3): 144
23 An L, Jia J G, Ma Q, et al. Preparation and siliconizing mechanism of Fe3Si type silicide layer deposited on AISI 304 stainless steel [J]. Chin. J. Nonferrous Met., 2011, 21: 3064
23 安亮, 贾建刚, 马勤等. AISI 304不锈钢表面Fe3Si型硅化物渗层的制备及渗硅机理 [J]. 中国有色金属学报, 2011, 21: 3064
24 An L, Jia J G, Ma Q, et al. Preparation of silicide layer on AISI 304 stainless steel and oxidation resistance [J]. Trans. Mater. Heat Treat., 2011, 32(7): 151
24 安亮, 贾建刚, 马勤等. AISI 304不锈钢表面硅化物渗层的制备与抗氧化性能 [J]. 材料热处理学报, 2011, 32(7): 151
25 An L, Ma Q, Jia J G, et al. Preparation of silicide layer deposited on AISI 304 surface and its cyclic oxidation behavior at 900 ℃ [J]. Hot Work. Technol., 2011, 40(20): 137
25 安亮, 马勤, 贾建刚等. AISI 304表面硅化物渗层的制备及其900 ℃循环氧化性能研究 [J]. 热加工工艺, 2011, 40(20): 137
26 Zhou Q, Zhang X M, Jia J G, et al. Effects of Al on the oxidation behavior of Fe3Si based ordered alloys at 800 ℃ [J]. J. Huazhong Univ. Sci. Technol. (Nat. Sci. Ed.), 2011, 39(3): 10
26 周琦, 章新民, 贾建刚等. Al对Fe3Si基有序合金800 ℃氧化行为的影响 [J]. 华中科技大学学报(自然科学版), 2011, 39(3): 10
27 Ma R, Xie Q, Huang J. Influence of alloying effects on structural stability and elastic properties of Fe3Si [J]. Rare Met. Mater. Eng., 2014, 43: 665
27 马瑞, 谢泉, 黄晋. 合金化效应对Fe3Si结构稳定性和力学性能的影响 [J]. 稀有金属材料与工程, 2014, 43: 665
28 China Nonferrous Metals Industry Association. China Molybdenum [M]. Beijing: Metallurgical Industry Press, 2013: 4
28 中国有色金属工业协会. 中国钼业 [M]. 北京: 冶金工业出版业, 2013: 4
29 Cheng L F, Zhang L T, Han J T. Preparation of Si-Mo oxidation protection coating for carbon-carbon composites [J]. High Technol. Lett., 1996, 6(4): 17
29 成来飞, 张立同, 韩金探. 液相法制备碳-碳Si-Mo防氧化涂层 [J]. 高技术通讯, 1996, 6(4): 17
30 Ingemarsson L, K.Hellström, Canovic S, et al. Oxidation behavior of a Mo(Si,Al)2 composite at 900-1600 ℃ in dry air [J]. J. Mater. Sci., 2013, 48: 1511
31 Dai D H, Liu M, Yu Z M, et al. Films and Coatings: Modern Surface Technology [M]. Changsha: Central South University Press, 2008: 105
31 戴达煌, 刘敏, 余志明等. 薄膜与涂层现代表面技术 [M]. 长沙: 中南大学出版社, 2008: 105
32 Hou S L, Liu Z D, Liu D Y, et al. Microstructure and oxidation resistance of Mo-Si and Mo-Si-Al alloy coatings prepared by electro-thermal explosion ultrahigh speed spraying [J]. Mater. Sci. Eng., 2009, A518: 108
33 Kuchino J, Shibayama T, Takahashi H, et al. Effect of microstructure on oxidation resistance of MoSi2 fabricated by spark plasma sintering [J]. Vacuum, 2004, 73: 623
34 Hou S X, Liu Z D, Liu D Y, et al. Effect of alloying with al on oxidation behavior of MoSi2 coatings at 1100 °C [J]. Surf. Coat. Technol., 2012, 206: 4466
35 Liu Y, Shao W, Wang C L, et al. Microstructure and oxidation behavior of Mo-Si-Al coating on Nb-Based alloy [J]. J. Alloy. Compd., 2018, 735: 2247
36 Hellström K, Persson P, Ström E. Oxidation behaviors and microstructural alterations of a Mo(Si,Al)2-based composite after heating at 1580 ℃ either in a furnace (Ex-Situ) or via alternating current (In-Situ) [J]. J. Eur. Ceram. Soc., 2015, 35: 513
37 Wang H, Liu Z G. A new method for preparation of compactness Mo-Si-B alloy [J]. Chin. J. Rare Met., 2011, 35: 679
37 王海, 刘志国. 致密Mo-Si-B合金制备的新方法 [J]. 稀有金属, 2011, 35: 679
38 Pan K M, Zhang L Q, Wang J, et al. Preparation and room temperature mechanical properties of T2 alloy in the Mo-Si-B system [J]. Rare Met. Mater. Eng., 2013, 42: 1080
38 潘昆明, 张来启, 王珏等. Mo-Si-B三元系中T2相合金制备及其室温力学性能 [J]. 稀有金属材料与工程, 2013, 42: 1080
39 Pi J L, Shao W, Zhou C G. Microstructural evolution and interdiffusion behavior of Mo-Si-B coating on Nb-Si based alloy [J]. Intermetallics, 2018, 95: 150
40 Pang J, Wang W, Zhou C G. Microstructure evolution and oxidation behavior of B modified MoSi2 coating on Nb-Si based alloys [J]. Corros. Sci., 2016, 105: 1
41 Riedl H, Vieweg A, Limbeck A, et al. Thermal stability and mechanical properties of boron enhanced Mo-Si coatings [J]. Surf. Coat. Technol., 2015, 280: 282
42 Perepezko J H. High temperature environmental resistant Mo-Si-B based coatings [J]. Int. J. Refract. Met. Hard Mater., 2018, 71: 246
43 Deng X K, Zhang G J, Wang T, et al. Microstructure and oxidation resistance of a multiphase Mo-Si-B ceramic coating on Mo substrates deposited by a plasma transferred arc process [J]. Ceram. Int., 2019, 45: 415
44 Kiryukhantsev-Korneev P V, Iatsyuk I V, Shvindina N V, et al. Comparative investigation of structure, mechanical properties, and oxidation resistance of Mo-Si-B and Mo-Al-Si-B coatings [J]. Corros. Sci., 2017, 123: 319
45 Nagasaki S, Hirabayashi M. Translated by Liu A S. Binary Alloy Phase-Diagrams [M]. Beijing: Metallurgical Industry Press, 2004: 275
45 长崎诚三, 平林真著, 刘安生译. 二元合金状态图集 [M]. 北京: 冶金工业出版社, 2004: 275
46 Yeom H, Maier B, Mariani R, et al. Magnetron sputter deposition of Zirconium-silicide coating for mitigating high temperature oxidation of Zirconium-alloy [J]. Surf. Coat. Technol., 2017, 316: 30
47 Choi H, Jang J, Zhang T F, et al. Effect of Si addition on the microstructure, mechanical properties and tribological properties of Zr-Si-N nanocomposite coatings deposited by a hybrid coating system [J]. Surf. Coat. Technol., 2014, 259: 707
48 Yin X W, Gutmanas E, Cheng L F, et al. Preparation of Zr-Si-C coating by chemical vapor reaction method [J]. J. Chin. Ceram. Soc., 2007, 35: 1419
48 殷小玮, Gutmanas E, 成来飞等. 化学气相反应法制备Zr-Si-C涂层 [J]. 硅酸盐学报, 2007, 35: 1419
49 Xu Y L, Sun W, Xiong X, et al. Microstructure and properties of ZrC-SiC multi-phase coatings prepared by thermal evaporation deposition and an In-Situ reaction method [J]. Surf. Coat. Technol., 2018, 349: 797
50 Wang D K, Dong S M, Zhou H J, et al. Fabrication and microstructure of 3D Cf/ZrC-SiC composites: Through RMI method with ZrO2 powders as pore-making agent [J]. Ceram. Int., 2016, 42: 6720
51 Huo C X, Guo L J, Wang C C, et al. Microstructure and ablation mechanism of SiC-ZrC-Al2O3 coating for SiC coated C/C composites under oxyacetylene torch test [J]. J. Alloy. Compd., 2018, 735: 914
52 Liu Y, Fu Q G, Guan Y W, et al. Ablation behavior of sharp-shape C/C-SiC-ZrB2 composites under oxyacetylene flame [J]. J. Alloy. Compd., 2017, 713: 19
53 Martin P J, Bendavid A, Cairney J M, et al. Nanocomposite Ti-Si-N, Zr-Si-N, Ti-Al-Si-N, Ti-Al-V-Si-N thin film coatings deposited by vacuum arc deposition [J]. Surf. Coat. Technol., 2005, 200: 2228
54 Daniel R, Musil J, Zeman P, et al. Thermal stability of magnetron sputtered Zr-Si-N films [J]. Surf. Coat. Technol., 2006, 201: 3368
55 Zeman P, Musil J. Difference in high-temperature oxidation resistance of amorphous Zr-Si-N and W-Si-N Films with a high Si content [J]. Appl. Surf. Sci., 2005, 252: 8319
56 Musil J, Dohnal P, Zeman P. Physical properties and high-temperature oxidation resistance of sputtered Si3N4/MoNx nanocomposite coatings [J]. J. Vacuum Sci. Technol., 2005, 23: 1568
57 Dong Y S, Zhao W J, Li Y R, et al. Influence of silicon on the microstructure and mechanical properties of Zr-Si-N composite films [J]. Appl. Surf. Sci., 2006, 252: 5057
58 Neto P C S, Freitas F G R, Fernandez D A R, et al. Investigation of microstructure and properties of magnetron sputtered Zr-Si-N thin films with different Si content [J]. Surf. Coat. Technol., 2018, 353: 355
59 Yalamanchili K, Forsén R, Jiménez-Piqué E, et al. Structure, deformation and fracture of arc evaporated Zr-Si-N hard films [J]. Surf. Coat. Technol., 2014, 258: 1100
60 Wu Z T, Qi Z B, Wei B B, et al. Understanding hardness evolution of Zr-Si-N nanocomposite coatings via investigating their deformation behaviors [J]. J. Eur. Ceram. Soc., 2016, 36: 3329
61 Yalamanchili K, Jiménez-Piqué E, Pelcastre L, et al. Influence of microstructure and mechanical properties on the tribological behavior of reactive arc deposited Zr-Si-N coatings at room and high temperature [J]. Surf. Coat. Technol., 2016, 304: 393
62 Chen Y I, Chang S C, Chang L C. Oxidation resistance and mechanical properties of Zr-Si-N coatings with cyclic gradient concentration [J]. Surf. Coat. Technol., 2017, 320: 168
63 Riedl H, Aschauer E, Koller C M, et al. Ti-Al-N/Mo-Si-B multilayers: an architectural arrangement for high temperature oxidation resistant hard coatings [J]. Surf. Coat. Technol., 2017, 328: 80
64 Aschauer E, Bartosik M, Bolvardi H, et al. Strain and stress analyses on thermally annealed Ti-Al-N/Mo-Si-B multilayer coatings by synchrotron X-Ray diffraction [J]. Surf. Coat. Technol., 2019, 361: 364
65 Li H X, Tang P, Wu Z T, et al. High-temperature thermal stability and tribological property of TiSiN/AlCrN nano-multilayer coatings [J]. J. Mechan. Eng., 2018, 54(6): 32
65 黎海旭, 唐鹏, 吴正涛等. TiSiN/AlCrN纳米多层涂层高温热稳定性及摩擦学特性研究 [J]. 机械工程学报, 2018, 54(6): 32
66 Wang X Y, Pang S Q. Wear mechanism analysis and endurance test of AlCrN coated carbide tools in cutting high-temperature alloy [J]. Trans. Beijing Inst. Technol., 2012, 32: 450
66 王新永, 庞思勤. AlCrN涂层硬质合金切削高温合金耐用度对比实验 [J]. 北京理工大学学报, 2012, 32: 450
67 Savage G. Carbon-Carbon Composites [M]. London: Publisher of Chapman & Hall, 1993
68 Guo H M, Shu W B, Qiao S R, et al. Preparation and properties of the multilayer oxidation protection coating for carbon-carbon composites [J]. Aerosp. Mater. Technol., 1998, (5): 37
68 郭海明, 舒武炳, 乔生儒等. C/C复合材料防氧化复合涂层的制备及其性能 [J]. 宇航材料工艺, 1998, (5): 37
69 Shu W B, Guo H M, Qiao S R, et al. Phase composition and surface morphology of TiC coating by chemical vapor deposition [J]. J. Northwest. Polytechn. Univ., 2000, 18: 229
69 舒武炳, 郭海明, 乔生儒等. 化学气相沉积法制备TiC涂层的相组成和表面形貌 [J]. 西北工业大学学报, 2000, 18: 229
70 Wang Y J, Zhang M Y, Su Z A, et al. Effect of pre-oxidation treatment time on C/C composites and its SiC anti-oxidation coating [J]. Mater. Sci. Eng. Powder Metall., 2018, 23: 591
70 王宇杰, 张明瑜, 苏哲安等. 预氧化处理时间对C/C复合材料及其SiC抗氧化涂层的影响 [J]. 粉末冶金材料科学与工程, 2018, 23: 591
71 Zhang X, Chen Z K, Xiong X. Preparation and high-temperature sintering mechanism of ZrB2 ceramic composite coatings for C/C-SiC composites [J]. J. Mater. Eng., 2015, 43(3): 1
71 张响, 陈招科, 熊翔. C/C-SiC复合材料表面ZrB2基陶瓷涂层的制备及高温烧结机理 [J]. 材料工程, 2015, 43(3): 1
72 Wang P P, Tong M D, Wang H H, et al. Gradient HfB2-SiC multilayer oxidation resistant coating for C/C composites [J]. Ceram. Int., 2018, 44: 20968
73 Jiang Y, Liu T Y, Ru H Q, et al. Oxidation and ablation protection of double layer HfB2-SiC-Si/SiC-Si coating for graphite materials [J]. J. Alloy. Compd., 2019, 782: 761
74 Xin J, Jia Y J, Zhao Z G, et al. A ZrC-SiC/SiC multilayer anti-ablation coating for ZrC modified C/C composites [J]. Vacuum, 2018, 157: 324
75 Gu S Y, Zhang S Y, Liu F, et al. Microstructure and thermal shock performance of Y2Hf2O7 coating deposited on SiC coated C/C composite [J]. Appl. Surf. Sci., 2018, 455: 849
76 Wang T Y, Luo R Y. Oxidation protection and mechanism of the HfB2-SiC-Si/SiC coatings modified by in-situ strengthening of SiC whiskers for C/C composites [J]. Ceram. Int., 2018, 44: 12370
77 Feng T, Li H J, Hu M H, et al. Oxidation and ablation resistance of the ZrB2-CrSi2-Si/SiC coating for C/C composites at high temperature [J]. J. Alloy. Compd., 2016, 662: 302
免责声明:本网站所转载的文字、图片与视频资料版权归原创作者所有,如果涉及侵权,请第一时间联系本网删除。
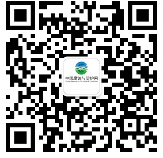
官方微信
《中国腐蚀与防护网电子期刊》征订启事
- 投稿联系:编辑部
- 电话:010-62316606-806
- 邮箱:fsfhzy666@163.com
- 中国腐蚀与防护网官方QQ群:140808414