摘要
采用超音速火焰喷涂技术在T91钢表面制备了45CT、NiCr/Cr3C2和NiCrAlY 3种涂层。在T91钢和3种涂层表面涂覆37.5%Na2SO4+37.5%K2SO4+15%Fe2O3+10%SiO2的合成煤灰后通入模拟烟气在750 ℃下进行腐蚀,获得腐蚀动力学曲线,腐蚀200 h后观察涂层腐蚀前后厚度变化。采用XRD、SEM、EDS对高温腐蚀产物成分、结构、形貌进行分析。结果表明,T91钢腐蚀非常严重,腐蚀产物大量剥落。3种涂层在腐蚀前期均表现为增重,而在腐蚀后期均存在失重现象。经过200 h腐蚀后,45CT、NiCr/Cr3C2和NiCrAlY涂层分别减薄25、112.7和93.1 μm。T91钢腐蚀后表面残留的腐蚀产物主要为Fe2O3。45CT涂层表面主要的腐蚀产物相为Cr2O3,而NiCr/Cr3C2和NiCrAlY的腐蚀产物为Cr2O3和NiCr2O4。所有样品表层腐蚀产物中不同程度均嵌入了煤灰粒子。腐蚀介质会通过涂层扩散到涂层/基体界面导致基体一侧发生腐蚀。45CT、NiCr/Cr3C2涂层样品基体处腐蚀严重导致涂层/基体开裂,而NiCrAlY涂层由于孔隙率较低,以及稀土效应,界面的基体侧腐蚀轻微,未出现裂纹。
关键词: 45CT ; NiCr/Cr3C2 ; NiCrAlY ; 热喷涂涂层 ; 热腐蚀
Abstract
Three coatings of 45CT, NiCr/Cr3C2 and NiCrAlY were prepared on the surface of T91 steel by high velocity oxygen fuel spray. The hot corrosion behavior of the coated steel was examined in a simulated flue gas at 750 ℃ for the prepared samples enveloped with a layer of synthetic coal ash of 37.5%Na2SO4+37.5%K2SO4+15%Fe2O3+10%SiO2. The sample was weighed at a certain interval to obtain the corrosion kinetic curve. The thickness changes of the coatings before and after 200 h corrosion were measured. The composition, structure and morphology of high temperature corrosion products were characterized by means of XRD, SEM and EDS. The results show that the bare T91 steel suffered from serious corrosion with corrosion products peeled off in large quantities. Mass gain in the early corrosion stage and then mass loss in the late corrosion stage was observed for the three coatings. After 200 h corrosion, the thinning amount of the three coatings 45CT, NiCr/Cr3C2 and NiCrAlY was about 25, 112.7 and 93.1 μm, respectively. The corrosion products remaining on the surface of T91 steel after corrosion were identified as mainly Fe2O3. The main corrosion products on the surface of 45CT coating was Cr2O3. However, the corrosion products of NiCr/Cr3C2 and NiCrAlY were Cr2O3 and NiCr2O4. Some coal ash particles were embedded in the corrosion products. For three coatings, corrosion media would diffuse through the coating to the coating/substrate interface during the test, which would lead to substrate corrosion. The substrate of beneath coatings of 45CT and NiCr/Cr3C2 suffered from serious corrosion, which led to cracks formation at the interface of coating and substrate. However, the substrate of beneath NiCrAlY coating showed slight corrosion, which may be ascribed to the low porosity and reactive element effect of rare earth of the coating.
Keywords: 45CT ; NiCr/Cr3C2 ; NiCrAlY ; thermal spraying coating ; hot corrosion

免责声明:本网站所转载的文字、图片与视频资料版权归原创作者所有,如果涉及侵权,请第一时间联系本网删除。
-
标签: 45CT, NiCr/Cr3C2, NiCrAlY, 热喷涂涂层, 热腐蚀
相关文章
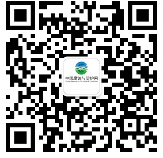
官方微信
《中国腐蚀与防护网电子期刊》征订启事
- 投稿联系:编辑部
- 电话:010-62316606-806
- 邮箱:fsfhzy666@163.com
- 中国腐蚀与防护网官方QQ群:140808414
点击排行
PPT新闻
“海洋金属”——钛合金在舰船的
点击数:7130
腐蚀与“海上丝绸之路”
点击数:5741