复合材料因其减重和卓越的综合性能和制造工艺优势,已经在飞机领域得到广泛应用,特别是在新型飞机设计研发中,复合材料装机用量已成为飞机先进性的重要标志和提升市场竞争力的技术筹码。例如,波音787 飞机复合材料用量达到结构重量的50%。但一旦复合材料内部出现损伤时,可能会影响其力学性能和结构安全性。因此,一直以来,有不少的业内专家和学者在研究损伤对复合材料性能的影响。在众多的复合材料损伤中,雷击损伤是业内高度关注的一种损伤形式。一方面,由于复合材料自身不良的导电性,容易产生雷击损伤;另一方面,飞机在飞行过程中,经常会遇到雷雨天气,不可避免地会受到雷电袭击,从而造成雷击损伤,严重时会影响到飞机的飞行安全。因此,复合材料雷击损伤的无损检测受到业内高度关注,先后有不少学者开展了复合材料雷击损伤的无损检测技术研究。
图1注:雷击冲击
针对碳纤维增强树脂基复合材料层压结构,设计制备了不同的复合材料层压结构试样,通过雷击模拟,对复合材料试样进行雷击冲击,然后,基于超声反射原理,利用高分辨率脉冲超声自动扫描成像检测方法,揭示复合材料受到雷击后在复合材料试样中引起的损伤及行为特征。
试样制备与试验方法
1 试样制备
针对目前飞机上已经普遍采用的碳纤维增强树脂基复合材料,设计制备了典型的复合材料层压结构试样,试样增强体为T700 纤维,基体为BA9916 环氧树脂,试样大小约150mm×100mm,厚度约3mm,试样为多向铺层结构,采用热压罐成型工艺制造而成,试样表面未加任何雷击防护涂层。对设计制备好的复合材料试样进行闪电冲击试验,主要利用闪电冲击模拟雷击,将闪电设备的放电端子置于复合材料试样的中心位置上方,进行雷击放电模拟。闪电电压U 和电流I 通过闪电设备设置,其雷击模拟原理是,通过闪电设备中的高压单元对电容进行充电,形成放电高压,然后,控制高压电容快速放电,通过放电端子在试样上方产生一个瞬时高压放电脉冲,对试样进行闪电冲击,形成雷击作用,雷击电压约为50kV,放电电流约为27kA。
图2注:超声成像检测方法
向长度(即y 方向投影长度),用L sy 表示闪电在复合材料试样内部引起的雷击损伤在y 方向的取向长度,y 方向亦为复合材料试样的宽度方向。在同样的条件下,L sx 或L ix 越大,表示闪电在复合材料试样表面或者内部引起的雷击损伤在x 方向取向越明显,沿x 方向扩展越大;L sy 或Liy越大,表示闪电在复合材料试样表面或者内部引起的雷击损伤在y 方向取向越明显,沿y 方向扩展越明显。
2 结果与分析
图4是经过雷击后,在复合材料试样表面形成的目视损伤检测结果,
图3注:损伤表征方法
图4注:雷击损伤目视检测结果
从图4中可以清晰地看出:(1)在试样中心位置,损伤最严重,且试样表面纤维出现了非常明显的“起毛”和烧伤情况,如图中白色箭头标示的损伤,这主要是由于在试样中心位置,是放电端子作用位置,也是雷击脉冲主瓣作用区域,因而放电电流最大,造成的损失最明显;(2)雷击损失在试样45°方向有一个明显的取向分布特征,这可能与试样中铺层纤维的取向有关;(3)在试样表面雷击损伤区还可以清晰地看出许多呈现随机分布的“鼓包”损伤,其大小不一,如图中白色箭头所标示的区域,这主要是由于雷击过程,不同能量放电脉冲“火花”与试样表面相互作用产生的雷击损伤;(4)雷击在试样表面形成的损伤具有明显的面积分布特点和取向特征,其中,雷击损伤在X 方向的最大投影长度L sx ≈ 83mm、在Y 方向的最大投影长度L sy ≈ 112mm。不过,从图4中的目视检测结果难以得到雷击在试样内部产生的损伤情况,这可以通过超声检测方法来揭示雷击在试样内部产生的损伤情况。
图5注:雷击损伤超声C-扫描检测结果
图5是试样中雷击损伤的超声C- 扫描成像结果,从图中可以清晰地看出:(1)雷击在试样内部产生的损伤面积和区域,如图中白色虚线所标示的区域;(2)图5中显示的内部雷击损伤与图4中显示的表面目视雷击损伤所反映出的分布取向特征相一致;(3)图5中显示的内部雷击损伤几乎连成片,而在图4中则呈现了许多分散分布的小“鼓包”损伤,这是因为C- 扫描反映的是试样内部雷击损伤在厚度方向的投影叠加后的结果;(4)内部雷击损伤与表面雷击损伤存在一定的拓展联系,比较图4 和图5 中显示的雷击损伤区域分布形状,不难看出二者存在相一致的面积扩展趋势联系,如图4 和图5中虚线所标示的损伤区域所示,这主要是由于雷击脉冲能量从试样表面沿厚度方向向其内部扩展所致;(5)从图5中可以十分清晰地看出在非雷击作用区,其成像灰度分布非常均匀,表明试样内部这些区域没有出现雷击损伤;(6)从图中超声 C-扫描结果可以得出雷击损伤在X 方向的最大投影长度 Lix ≈ 172mm、在Y 方向的最大投影长度Liy ≈ 124mm,显然,比图4中显示的雷击损伤在X方向的最大投影长度约大41mm、在Y 方向的最大投影长度约大60mm,即,Lix / L sx ≈ Liy /L sy ≈ 1.5,由此可见,雷击在复合材料内部引起的损伤要比表面损伤大的多。为了揭示雷击损伤在试样厚度方向的分布与拓展情况,对雷击试样进一步开展了超声B- 扫描成像检测分析。
图6注:雷击损伤超声B-扫描检测结果
图6是对复合材料试样进行超声B- 扫描成像检测的结果,对应试样中心位置附近的其中一个断面位置,声波从试样雷击作用区的对侧入射,图中F和B分别对应试样的表面和底面(雷击作用区一侧)。从图6中可以非常清晰地看出:(1)试样断面轮廓,表明入射声波完全穿透了试样,并在试样底面和表面形成了清晰的声波反射,也表明入射声波能够有效传播到雷击损伤区;(2)从图6中灰度分布,可以清晰地看出试样内部铺层分布特征,即层压铺层拓展分布情况,如图6中沿水平方向呈现“ 波浪”状分布的白色灰度条带所示,这主要得益于采用高分辨率超声检测技术,采用图2所示的超声扫描成像试验系统,回波脉冲特性可以达到单个周期,此时,其检测分辨率和表面检测盲区可以稳定地达到单个复合材料铺层的厚度,约0.13mm;(3)从图6中可以非常清晰地看出,雷击损伤明显位于试样近表面,这表明闪电电压在50kV、电流在27kA 左右时,雷击在复合材料试样中产生的损伤主要位于复合材料层压结构表面和近表面,从图6中不难得出雷击损伤在试样厚度方向主要分布在约0~0.5mm 的深度范围,即此时,雷击主要是造成试样近表面几个纤维铺层的破坏;(4)从图6中还可以非常清晰地看出雷击损伤沿试样厚度方向分布特征,即雷击损伤区由若干个不同位置和深度的小损伤构成,如图白色箭头所标示的白色灰度区,这与图4中目视检测结果相一致;(5)从图6中超声B- 扫描结果,还可以看出,雷击损伤由试样表面向内部的增进和拓展特征,这主要是因为,在进行超声B- 扫描成像检测时,所采用的超声系统能够有效提取到来自位于不同深度铺层的损伤的声波信息,因而,在图6 中可以清晰地看出损伤的构成特征和沿试样深度方向的拓展细节。因此,从图6中的超声B-扫描结果,可以十分清晰地揭示出雷击损伤在试样断面深度位置和沿试样厚度方向的分布特征,与超声C-扫描结果相结合,即可得到雷击损伤在试样中的3D分布。
结 论
(1) 在雷击电压为50kV、电流为27kA 时,雷击在T700/BA9916 碳纤维复合材料层压结构中会产生明显的目视表面损伤和内部损伤,损伤深度分布主要位于0~0.5mm 范围内。
(2) 采用高分辨率脉冲超声反射法,通过超声C- 扫描成像方法,可以非常有效和清晰地揭示雷击在复合材料层压结构中产生的损伤区域、面积、沿铺层方向的取向等损伤行为特征。在超声C- 扫描成像中损伤分布特征与试样表面目视观察到得的损伤存在一致的关联特征,不过,利用超声C- 扫描成像检测方法,能够更加有效地检出复合材料内部的雷击损伤及其确切的分布特征、大小等。
(3) 超声C 扫描成像结果表明,雷击在复合材料内部引起的损伤要比在表面引起的损伤大的多。
(4) 借助高分辨率超声B- 扫描成像方法,可以十分有效地揭示出雷击损伤在复合材料试样断面中的分布、深度及其在厚度方向的拓展特征,与超声C- 扫描相结合,可以非常有效的得到雷击损伤在复合材料层压结构中的3D 分布特征,而且利用所采用的高分辨率超声B- 扫描成像技术,还可以得到复合材料层压结构厚度方向的铺层拓展特征。
因此,所研究的高分辨率超声反射法及其成像检测技术和检测系统为复合材料雷击损伤的无损检测与损伤行为的研究提供了一种非常有效的检测手段。目前,该项检测技术及其超声检测系统已经得到了大量的实际检测应用,取得了非常好的检测效果。
责任编辑:田双
《中国腐蚀与防护网电子期刊》征订启事
投稿联系:编辑部
电话:010-62313558-801
邮箱:ecorr_org@163.com
中国腐蚀与防护网官方 QQ群:140808414
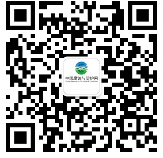
官方微信
《中国腐蚀与防护网电子期刊》征订启事
- 投稿联系:编辑部
- 电话:010-62313558-806
- 邮箱:fsfhzy666@163.com
- 中国腐蚀与防护网官方QQ群:140808414