一、高温合金概述
高温合金是指以Fe、Ni、Co为基,在600℃以上具有抗氧化和抗腐蚀性能,并在一定应力作用下可以长期工作的金属材料。图1为世界高温合金的发展趋势及其我国研制的合金,高温合金既是航空发动机的燃料室、导向器、涡轮叶片和涡轮盘等热端部件、航天火箭发动机高温部件的关键材料,又是工业燃气轮机、能源、化工等工业部门所需的高温耐蚀部件材料,是国民经济中不可或缺的一类重要材料[1]。
图1高温合金的发展历程[1]
目前,国际市场上每年消费的高温合金材料近30余万吨,图2为主要的消费区域分布,我国高温合金的市场规模年增速保持在20~30%,而全球范围内能够生产航空航天用高温合金的企业不超过50家,主要集中在美、英、日、德、法、俄罗斯等国家,例如,美国的GE、PW、Haynes Stellite、Inco Alloys International、Cannon-Muskegon、Westinghouse、Cabot、Martin Marietta、Standard Pressed Steel、Whittaker、Special Metal、Universal-Cyclops Steel、Howmet、Pratt & Whitney,俄罗斯的United Aircraft Company和加拿大的Mond Nickel Company等公司,具有明显的寡头特征。
图2 全球高温合金消费区域分布(2019年)
自1956年第一炉高温合金GH3030试炼成功,我国高温合金的研究、生产和应用已经历了六十多年的发展历程。目前,在国家发展与改革委员会、工业与信息化部、中国有色金属工业协会和国防科工局的统筹监管下,我国已经形成了一些生产装备比较先进、具有一定规模的生产基地和企业,例如,钢研高纳、抚顺特钢、宝钢特钢、中国航发、万航模锻、万泽股份、图南股份等,也形成了一批具有自主创新研发能力的科研院所,比如,钢铁研究总院高温材料研究所、北京航空材料研究院、中科院金属所、北京航空航天大学、北京科技大学、西北工业大学等[2]。
根据中国高温合金手册(2012年),我国高温合金共列入牌号194个,其中,等轴铸造镍基合金62个,镍基变形合金43个,铁基变形合金30个,金属间化合物基20个,ODS合金5个,粉末冶金高温合金3个[3]。我国高温合金市场占比最大的是变形高温合金,约为70%,其次是铸造高温合金,约为20%;按基体元素来说,占比最大的是镍基高温合金,约为整个市场的80%,其次是镍-铁基高温合金,约为14%,钴基高温合金约为6%左右。
二、我国高温合金的研究进展
我国高温合金经历了仿制、仿创结合到独创的发展过程,通过吸取发达国家的经验并结合我国的实际情况进行自主创新而形成了我国的高温合金体系。美、英等国家是以公司或厂家自成合金系统,而我国是以国家为统一的系统,并按合金制备方式、基体元素、强化方式的顺序构成高温合金系列和体系。按制备方式有变形高温合金、铸造高温合金(包括等轴晶、定向凝固柱晶和单晶高温合金)、粉末冶金高温合金、弥散强化高温合金、金属间化合物高温材料、焊接用高温合金丝,以及高温合金基自润滑材料等;在这些不同合金系列下再分为铁基、镍基、钴基及铬基高温合金;在相同的基体下,又分为固溶强化型和时效强化型[2]。
目前,我国的高温合金主要存在的问题和不足包括:冶金缺陷多,如黑斑、白斑、碳化物偏聚等;组织均匀性较差;杂质元素含量高,降低了强度和使用寿命;成本高,再利用率低。
2019年9月22~25日在湖北黄石召开了由北京科技大学、东北大学和大冶特钢承办的第十四届全国高温合金年会,集中展示了我国近年来在高温合金研究方面取得的成果,包括变形高温合金品种发展及其残余应力控制、铸造高温合金的研究发展、粉末高温合金及粉末纯净化技术、金属间化合物基高温结构材料的研究与应用进展等。
1、变形高温合金
变形高温合金是指通过铸造-变形工艺生产的高温合金,工作范围为-253~1320℃,包括盘、板、棒、丝、带、管等产品,例如GH128、GH4169等,广泛应用于航天、航空、能源、石化、核电等工业领域。近年来,变形高温合金分别在工艺流程、开发新合金和新技术等方面都取得了大量的突破和应用成果。
- 工艺流程
国内变形高温合金冶炼通常采用真空感应+真空自耗两联或真空感应+电渣重熔+真空自耗三联的熔炼方式。通过对真空感应炉内流槽的水模拟和数值模拟,并对结构进行优化设计,可以改善流槽内流场分布和温度分布,从而提高铸锭的质量和洁净度,如图3所示。
图3 真空感应熔炼流槽优化前后对比[4]
高温合金铸锭在凝固过程中会产生较严重的成分偏析,为减轻和改善成分偏析,提高材质的均匀性,除改进冶炼工艺外,最重要的技术措施是进行均匀化处理,通过高温下的长时间加热,促进溶质元素原子的扩散迁移,达到枝晶干与枝晶间元素浓度差异的最小化。随着铸锭尺寸的扩大,偏析情况会受到凝固冷速的影响而相应加剧,可以通过对比不同的均匀化制度下的二次枝晶间距和偏析系数,从而确定最终的均匀化温度和时间。
为了提高GH4720Li合金铸锭的开坯成材率以及棒材的质量水平,通过大量热模拟压缩试验,获得并建立不同热变形条件下的数学模拟和开裂判据,从而优化锻造工艺参数,包括逐级降温及火次变形量合理分配。相关研究表明,快锻开坯充分破碎铸锭铸态组织后,再辅之以径锻,可以改善棒材表面状态,提高成材率。
GH4706合金超大型涡轮盘是当代E/F级重型燃机的核心热端转动部件,锻件直径超过2000mm,重量达6t,是亟待国产化的最关键部件之一。该合金的成分接近于GH4169,是一种γ’相与γ”相强化的Fe-Ni基变形高温合金。涡轮盘的模锻既要实现盘件的热加工成型又要实现组织性能控制,二者相互影响、相互制约[4]。2013年,我国自主设计研制的世界最大的8*104t模锻液压机(图4)投入生产并试制成功了直径为1500mm的GH4738合金涡轮盘锻件,这为超大型GH4706合金涡轮盘的制备提供了一定的参考经验,但仍面临严峻的挑战。
图4 “国之重器”8万吨大型模锻压机
在张北江等人的研究基础上[5],构建了GH4706合金的本构关系与显微组织演化规律模型,应用数值模拟技术进行热加工工艺优化,最终实现了超大型GH4706合金涡轮盘锻件的国产化,如图5所示,性能达到了美国GE-B50A651标准的要求。
图5 直径为2100mm的超大型GH4706合金涡轮盘锻件[4]
残余应力源自材料制备过程中内部不均匀的塑性变形,本质上是残留在材料内部的晶格畸变。在再结晶温度附近进行的热变形,是难以形成高水平残余应力的;即便在低温锻造或锻后冷却中形成的残余应力通常也可以在后续的高温固溶处理中得以释放。因此,高温合金盘锻件一般在锻造成型后需要在固溶处理后快速冷却,以确保γ’或γ”相不发生粗化。图6为不同的残余应力测试技术对应的测试深度和分辨率。对于高温合金盘锻件,需要测试分析距表层10mm甚至更深的内部残余应力,分辨率要求为mm级,因此主要方法包括中子衍射法(neutron diffraction)、轮廓法(contour method)、深孔法(deep-hole drilling)和超声法(ultrasonic)。
图6 各种残余应力测试方法的测试深度和空间分辨率[6]
钢铁研究总院的毕中南等人总结了高温合金涡轮盘锻件内部残余应力的测试方法,阐明了固溶、淬火、时效、零件加工等制备工艺过程中残余应力的演化规律与机制[6]。
超声检测作为无损检测的一种重要方法,利用探头发出的超声波进入工件内部传播,当内部存在声学特性与基体不同的不连续或不均匀组织时,在界面处就会发生传播方式和信息的变化,从而为无损检测和评价提供定性和定量分析的依据。范兴义、林时钱等人对盘锻件组织的晶粒尺寸与超声杂波之间的关系进行了充分研究,以确定影响检测结构的主要原因和适宜的检测参数。
- 新合金
王庆增、陈国胜、孙文儒等人在对P强化和P、B复合强化机理研究的基础上,发展了GH4169G合金,该合金在保持GH4169合金优异的综合性能的同时,将使用温度提高了30℃,达到680℃;并使650℃下的使用寿命提高了3倍以上;同时焊接和热加工性能与GH4169合金相当,具有广阔的应用前景。
GH4169D合金是在GH4169合金的基础上,通过降低Fe含量,加入固溶强化元素W和Co,调整Al、Ti含量及其比例,并适当提高Nb含量和调整微量元素含量而研制成功的,成功填补了世界上2个最广泛应用高温合金---650℃用GH4169和750℃用GH4738合金之间长期存在的空白。
在依托铸锻工艺发展高性能涡轮盘材料方面也取得了重要进展,相继研制了GH4065、GH4079和GH4975等高性能变形高温合金涡轮盘材料,特别是GH4065合金的综合性能达到了粉末冶金材料的水平,有望为我国先进航空发动机热端转动部件的选材提供成熟可靠的解决方案。
GH4282合金在保持一定数量的沉淀强化γ’相的基础上,通过控制γ’相的结构、组成和析出动力学,解决了高强度时效强化燃烧室合金中由于γ’相的大量析出导致的冷加工和焊接困难的问题,该合金在650~950℃范围内保持了极佳的高温强度和热稳定性,同时对焊接和冷加工性能进行了很好的平衡和优化。
- 新技术
我国开发了氮化物强化高温合金NGH5011,并针对内生弥散氮化物强化合金的氮化工艺流程中涉及的N在表面的吸附溶解、在基体的均匀扩散、反应界面的氮化物析出等关键物理化学过程开展了系统研究工作。
钢铁研究总院高温材料研究所利用增材制造技术,成功制备出3D-In718合金的燃气涡轮盘和整体叶轮,零件致密度达到99.9%,组织性能均远优于铸件,室温、高温拉伸强度、塑性和持久性能均可满足锻件标准。
此外,采用电渣重熔连续定向凝固冶炼+3D锻造制坯+等温锻造的新型铸锻工艺技术成功制备了变形FGH4096合金涡轮盘。
2、铸造高温合金
铸造高温合金具有较宽的成分范围,根据使用温度又分为三类:在-253~650℃使用的等轴晶铸造高温合金,如K4169;在650~950℃使用的等轴晶铸造高温合金,如K419;以及在950~1100℃使用的定向凝固柱晶铸造高温合金,如DD402。航空发动机机匣是典型的中低温条件下使用的等轴晶高温合金铸件,结构复杂化、尺寸精确化和薄壁轻量化是发展趋势,从而精密成形和凝固组织的协同控制是急需解决的重大技术难题。
等轴晶镍基高温合金主要以γ相为基体,通过添加Al、Ti、Nb和Ta等元素形成体积分数可达70%的γ’相或γ”相进行强化,并以C、B和Zr作为晶界强化元素在晶界偏聚或形成碳化物或硼化物来提高合金的综合性能。等轴晶铸造高温合金的发展方向主要为:根据合金化理论和冶金原理,结合计算机模拟技术设计具有良好综合性能的新型材料;针对不同合金的用途,通过对现有合金成分的调整来获得优异特定性能;改进和提高合金的冶炼工艺,提高合金的冶金质量;通过新型工艺技术改善铸件的质量和力学性能。
采用传统的“经验试错”方法,成本高、周期长、难度大,基于计算材料学、大数据处理、机器学习、高通量试验等手段开展合金成分设计将会成为一大趋势。基于电子空位理论、结合次数和合金元素的d轨道能发展和完善的相计算可以模拟和预测合金中TCP相的析出规律,而如何建立合金成分与高性能之间的量化关系是目前单晶合金设计的关键。傅恒志、介子奇等人研究了K4169高温合金的熔体凝固特性,获得了熔体过热温度对形核过冷度的影响规律,如图7所示,并进一步验证了熔体超温处理可明显细化晶粒尺寸、改善析出相的形貌和分布,有效减轻合金元素偏析,从而改善铸态高温合金的综合力学性能[7]。
图7 熔体过热温度对K4169高温合金形核过冷度的影响[7]
利用JMatPro、Thermal-calc和Panda软件可以较准确地计算出不同成分的镍基高温合金的初熔温度、合金密度,以及不同平衡态下的相组成及含量,并预测出热处理窗口和糊状区间等,在此基础上,制定合适的热力学判据,筛选出满足要求的合金成分进行试验测试,可以节省合金的开发时间和成本。
通过铸件成型模拟技术,可以模拟充型过程中的温度场分布,从而合理设计冒口和浇注系统,优化浇注工艺参数,并预测缩孔、冷隔、欠铸和缩松等缺陷及其冷却后的残余应力,为实际生产提供理论指导。目前,铸件成形模拟技术的发展已经较为成熟,典型的商用模拟软件有:ProCAST、MAGMA、AFSolid和PAM-CAST等。柳百成等人提出了利用计算机技术改造铸造行业,在铸造过程宏、微观模拟仿真领域开展了大量研究,并开发了一系列工程应用的数值模拟软件[8]。
常见的组织模拟方法有:第一性原理、分子动力学法、Monte Carlo、元胞自动机法、相场法、有限元等。例如,将蠕变损伤的晶体模型耦合到相场模型中,可实现蠕变3个阶段的组织演化和性能的同步模拟,得到蠕变组织演化过程及蠕变曲线,如图8所示,这为高温合金蠕变模拟提供了新的途径,有利于以性能为导向的微观组织优化模拟工作的开展。
图8 相场模拟得到的950℃、300MPa蠕变条件下γ’相的演化过程[7]
单晶高温合金消除了晶界,具有优异的高温蠕变、抗氧化和抗腐蚀性能,其研发起始于20世纪70年代的美国Pratt & Whitney公司,自20世纪80年代PWA1480单晶高温合金成功研制和应用以来,国外单晶合金迅猛发展,在2000年左右研制了第四代单晶合金。从第一代发展到第四代单晶高温合金,工作温度已经提高到1827℃,远高于初熔温度(1280~1330℃),同时Re、Ru等贵金属元素的含量不断增加,成本也越来越高。
我国单晶合金的研制起步较晚,且多以仿制为主。近年来,我国单晶高温合金研制与应用取得了显著进展,并自主研制了第三代单晶合金DD33、DD9以及第四代单晶合金DD91、DD15等,已经具备了单晶高温合金新材料、新工艺自主研发能力,特别是在军民融合相关政策的引导和推动下,出现了一批高温合金相关的民营企业,其中大多数聚焦于单晶高温合金母合金和单晶叶片的生产。
目前,单晶高温合金的成分设计方面的研究主要集中在英、德和日本等国家的大学和科研院所,且设计空间越来越小,提高综合性能的难度越来越大,国外根据实际用途开始研发各种“定制”合金。例如,GE公司为了降低第二代单晶合金中Re含量,发展了性能接近René N5的René N515合金(1.5%Re),并逐渐替代René N5应用于航空发动机涡轮叶片。
晶粒细化可大幅度提高铸件低周疲劳性能,减少力学性能的分散度,改善机械加工性能。其主要机制是促进形核和抑制晶粒长大,常用的方法有热控法(FGP、Grainix法)、动力学法(铸型搅动、电磁振动和脉冲电流等)、化学法(细化剂)等。北京航空材料研究院、北京航空航天大学等对单晶高温合金的低周疲劳、高周疲劳、蠕变性能等方面都做了大量的分析研究[9,10]。此外,在一些新型工艺如反重力铸造技术、增材制造等方面也取得了一定的进展。
3、粉末高温合金
图9为国内外先后研制出的四代粉末高温合金,我国目前已研制出以FGH4095合金为代表的第一代高强型粉末高温合金和第二代损伤容限型FGH4096合金,近年来正在研制高强损伤容限第三代粉末高温合金,并对第四代粉末高温合金进行了初步探索研究[11]。
图9 国内外粉末高温合金的发展[11]
高品质高温合金粉末,是先进航空发动机粉末涡轮盘研制和生产的基础和保障。目前高温合金粉末制备主要有Ar气雾法制粉(AA粉)和等离子旋转电极法制粉(PREP粉)2种方法。北京航空材料研究院的张国庆课题组等人开展了一系列Ar气雾化高温合金粉末的制备装置和技术,用以制备粉末高温合金涡轮盘件等热端部件,同时也为3D打印增材制造提供原材料。他们分别在合金雾化过程、制粉过程粒度控制(图10)、O含量控制、非金属夹杂控制等方面取得了一定的成果和经验。
图10 不同粒径粉末颗粒轨迹图[11]
4、金属间化合物基高温合金
金属间化合物是由2种或2种以上金属元素或金属元素与类金属元素按照一定原子比组成的化合物。共价键和金属键的共存使得金属间化合物在较长范围内存在长程有序的超晶格结构。在高温下,金属间化合物的位错迁移率相对降低,从而具有较高的高温强度。比较典型的有Ti-Al、Ni-Al、Nb-Si,它们有着优异的高温强度和较低的密度,但也存在室温断裂韧性低、高温抗氧化性差等问题,使其在应用上受到限制,也成为该领域研究的难点和重点。
近年来,我国在金属间化合物基高温合金材料的基础研究与工程应用方面取得了重要的进展,以TiAl、Ti3Al、Ti2AlNb、Ni3Al基合金为代表,在性能和工艺方面进步显著,并研发出一些具有自主知识产权的新型高温结构材料,为我国高性能航空发动机的研制做出了重要的贡献。Nb-Si基合金在凝固工艺和抗氧化涂层的基础研究方面也取得了显著的进展,并逐渐向实用化接近。例如,在Ti-Al系金属间化合物高温合金方面取得的重要进展有:新一代高铌含量TiAl合金成分设计与组织、性能关系研究发现新的规律和机制;二代TiAl合金工程应用取得突破;Ti3Al和Ti2AlNb合金工艺进步显著,应用范围不断扩大[12]。
三、高温合金专家简介
师昌绪——中国高温合金材料的开拓者
师昌绪(1920-2014),1957年负责主持我国高温合金方面的工作,并研制出我国第一个铁基高温合金GH135,领导研制出我国第一代空心气冷铸造镍基高温合金M17涡轮叶片,获得国家级奖励10余项。1980年当选中国科学院院士,1994年当选中国工程院院士,1995年当选第三世界科学院院士,2010年荣获国家最高科学技术奖,2015年被评为感动中国2014年度人物。他参与创办或主编了Journal of Materials Science and Technology、能源材料、中国科学基金、自然科学进展、金属学报等期刊。
胡壮麒
胡壮麒(1929-2016),长期从事高温合金的研制及亚稳态新材料和新工艺的研究,为我国科技和国防事业做出了重要贡献。他先后在发动机一级涡轮叶片K17G铸造镍基合金、抗热腐蚀DZ38G定向凝固镍基高温合金、单晶镍基高温合金非平衡凝固行为等方面都有重大科研成果,并发展了一系列性能优异的新材料,包括高温合金、定向结晶和单晶合金、金属间化合物和亚稳态材料。1985年获得国家科技进步奖一等奖,1986年获得国家科技进步奖二等奖,1995年当选为中国工程院院士,2003年获何梁何利基金科学与技术进步奖,2004年被中国金属学会高温合金学术委员会授予杰出贡献奖。
仲增墉
钟增墉,1961年开始从事高温合金研究和制造工作,负责研制成功了一系列难变形高温合金关键新材料,其中涡喷六发动机涡轮叶片用GH37镍基高温合金,使60年代初国家急需军工材料立足于国内,获得国防工办和冶金部的嘉奖;涡喷十三发动机用高热强(950℃)难变形镍基高温合金GH220获冶金部科技进步一等奖;成功研制了GH118(950℃)、GH38A、GH43、GH49、GH33和GH527等航空航天用高温合金;并首创了电渣熔炼高温合金工艺,达到了当时的国际水平;在国际上首先提出了高温合金的镁微合金化及其理论,改善了高温合金材料的性能;高温合金中弯曲晶界的形成及其作用研究、高热强合金中TCP相析出、影响及控制的研究等都达到了较高水平。
傅恒志
傅恒志(1929~),材料及冶金学专家。1988年,他创建了中国国内唯一的凝固技术国家重点实验室。1993年,成为中国首批入选由世界著名科学家、教育家组成的国际高校科学院院士。1995年,当选为中国工程院院士,并同年当选俄罗斯宇航科学院外籍院士。2013年,获得第三届中国机械工程学会“中国铸造终身成就奖”。先后获得国家科技进步二等奖1项,国家发明奖3项,国家优秀教学成果二等奖1项,省部级奖12项,发表论文1100余篇,出版专著7本。
黄伯云
黄伯云,1999年当选为中国工程院院士,2007年当选为发展中国家科学院院士,“十五”国家863计划新材料领域专家委员会主任,兼任中国材料研究学会理事长。他领导创建了粉末冶金国家重点实验室、粉末冶金国家工程中心、轻质高强国防科技重点实验室以及有色金属先进结构材料与制造协同创新中心等一系列创新平台,并获得留学回国人员成就奖、何梁何利科学与技术进步奖、全国国防科技工业系统先进工作者、中青年有突出贡献专家、全国杰出专业技术人才、“CCTV2005年感动中国”十大人物、全国劳动模范、全国优秀共产党员等荣誉称号。
柳百成
柳百成(1933.2~ ),铸造及材料工程专家。他长期从事用信息技术提升铸造行业技术水平及提高铸造合金性能的研究,致力于振兴中国制造业及推广先进制造技术等战略研究。曾主持及参加多项国家重大科技项目、973项目,先后获部委级科技进步一等奖、二等奖等十余项奖励,国外奖励2项及发明专利2项。1999年当选为中国工程院院士,2002年获光华工程科技奖,2011年、2015年先后获得中国机械工程学会中国铸造杰出贡献奖及中国铸造终身成就奖,2017年被评为海归中国梦年度人物奖。
干勇
干勇,1947年8月出生,冶金材料专家。1994年至今任连铸技术国家工程研究中心主任,2001年4月至今任钢铁研究总院院长,同年当选为中国工程院院士。他长期从事冶金、新材料及现代钢铁流程技术研究,是我国材料、冶金、现代钢铁流程的学术带头人之一。先后获国家科技进步二等奖2项及省部级科技进步一等奖5项,获准专利24项,其中发明专利15项,发表论文140余篇,出版著作3部。
宫声凯
宫声凯(1956.7~),北京航空航天大学教授,兼任中国腐蚀学会副理事长、中国金属学会高温材料分会副理事长。他长期从事新型金属间化合物基合金、单晶叶片及热障涂层研究。发明了新型高承温、低密度低铼Ni3Al基单晶合金和超高温热障涂层;研制出的超气冷单晶叶片,支撑了我国新型发动机研制,相关成果获得包括国家技术发明一等奖在内的省部级以上科技奖励8项,授权发明专利80余项,发表SCI论文近300篇。
参考文献
[1] 师昌绪、钟增墉,我国高温合金的发展与创新[J],金属学报,2010,45(11):1281-1288
[2] 中国高温合金50年1956~2006,师昌绪、仲增墉主编,冶金工业出版社,2006年
[3] 中国高温合金手册,中国金属学会高温材料分会,中国标准出版社,2012年
[4] 杜金辉、吕旭东、董建新、孙文儒、毕中南、赵光普、邓群、崔传勇、马惠萍、张北江,国内变形高温合金研制进展[J],金属学报,2019,55(9):1116-1134
[5] 张北江、黄烁、张文云、田强、陈石富,变形高温合金盘材及其制备技术研究进展[J],金属学报,2019,55(9):1095-1115
[6] 毕中南、秦海龙、董治国、王相平、王鸣、刘永泉、杜金辉、张继,高温合金盘锻件制备过程残余应力的演化规律及机制[J],金属学报,2019,55(9):1161-1176
[7] 张军、介子奇、黄太文、杨文超、刘林、傅恒志,镍基铸造高温合金等轴晶凝固成形技术的研究和进展[J],金属学报,2019,55(9):1145-1160
[8] 许庆彦、杨聪、闫学伟、柳百成,高温合金涡轮叶片定向凝固过程数值模拟研究进展[J],金属学报,2019,55(9):1176-1186
[9] 张健、王莉、王栋、谢光、卢玉章、申健、楼琅洪,镍基单晶高温合金的研发进展[J],金属学报,2019,55(9):1077-1095
[10] 李嘉荣、谢洪吉、韩梅、刘世忠,第二代单晶高温合金高周疲劳行为研究[J],金属学报,2019,55(9):1196-1205
[11] 张国庆、张义文、郑亮、彭子超,航空发动机用粉末高温合金及制备技术研究进展[J],金属学报,2019,55(9):1133-1145
[12] 宫声凯、尚勇、张继、郭喜平、林均品、赵希宏,我国典型金属间化合物基高温结构材料的研究进展与应用[J],金属学报,2019,55(9):1067-1177
免责声明:本网站所转载的文字、图片与视频资料版权归原创作者所有,如果涉及侵权,请第一时间联系本网删除。
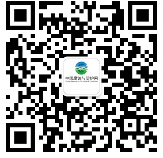
官方微信
《中国腐蚀与防护网电子期刊》征订启事
- 投稿联系:编辑部
- 电话:010-62316606-806
- 邮箱:fsfhzy666@163.com
- 中国腐蚀与防护网官方QQ群:140808414