铁路客车普遍采用“帽型柱”钢结构作为车体的骨架,骨架+蒙皮的车体结构自上世纪七、八十年代一直沿用至今。随着运行环境的不断变化,近年来,检修机构、铁路局屡次提到铁路客车钢结构腐蚀愈加严重。为此,铁路行业于2015年多次组织了关于铁路客车钢结构腐蚀问题的专题会议,并结合各制造厂、各铁路局、各涂料厂家,形成运辆客车函【2015 】 73号文件。随着73号文件的执行以及制造厂对客车防腐研究的不断深入,逐步得出造成客车钢结构腐蚀越来越严重的原因之一是客车“死角部位”无法彻底进行表面处理,“内腔”部位焊接后炭黑无法清除,局部死角无法进行“二次涂装”,使腐蚀从钢结构“边、角、孔、洞、缝”的部位开始腐蚀,同时在车体钢结构制造过程中,钢材表面需进行预涂底漆处理,作为暂时性防腐,是为了避免钢结构在车体制造过程中发生大面积腐蚀,然而预涂底漆本身防腐性较差,在后续整车涂装中,预涂底漆又无法彻底清除,这就造成整车的防腐性能存在一定的风险。
通过调研发现,自2009年至2012年铁路客车底架部位腐蚀数约占客车各部位总和的64% ,侧端墙部位次之,占比35% ,其他数据,见图1 。检修客车底架腐蚀速度相对全车腐蚀速度最快,且腐蚀量较大,并且底架大量腐蚀在3。5年、4年、4。5年时腐蚀达到高峰期,见图 2 。钢结构腐蚀部位主要表现在:( 1 )钢结构部件搭接面,如雨檐和顶板之间、侧墙板与边梁搭接处、地板横梁与铁地板的搭接处,侧门框与侧柱的搭接处、端墙板与缓冲梁搭接处;(2 )易积水或积垢的位置,如车窗下角、侧墙板下部、内外端墙下部、铁地板、车顶中部及通风器根部、侧柱中部及侧柱根部等;(3 )与腐蚀物接触的部位,如蓄电池箱、小间地板、脚蹬围板等。
为解决铁路客车耐腐蚀性问题,现从设计、工艺、运营等角度出发,分析影响防腐性能的主要因素,避免后续出现类似问题,为后续铁路客车新产品的开发与研究奠定防腐涂装基础。
一、 影响因素
1.1 设计方面
1.11 运行环境
目前,铁路客车的运行里程增长,运行距离增大,频次增多,受环境污染程度的加剧,运行环境越加恶劣,因此,充分考虑运行环境参数,气候条件的变化,尤其是温湿度。通常情况下,温度愈高,腐蚀速度愈快,相对湿度越高,腐蚀程度约严重,如图 3 。在临界相对湿度以下,相对湿度的变化对腐蚀速度的影响不大,一旦超过临界相对湿度,腐蚀速度就随相对湿度的增大而急剧上升。钢材腐蚀的临界相对湿度在70%左右,而我国长江以南地区夏季平均相对湿度在80%左右,所以在南方运行的车辆比在北方、西北地区运行的车辆腐蚀严重。另外,铁路车辆机车动力装置(锅炉及柴油机)以及车辆自身带的各种炉灶会排出大量的污染性气体,使车辆周围的空气中二氧化碳、二氧化硫、硫化氢、氮氧化物的浓度较高,尤其是在我国西南地区的铁路,由于山多隧道多,隧道内污染气体的浓度很高,再加上西南地区阴雨潮湿,高温季节周期长,导致西南地区车辆严重腐蚀。在沿海地区则由于空气中含有较多的氯离子、氟离子等盐雾离子,空气相对湿度较大,使沿海地区运行的车辆较西北地区运行的车辆容易产生腐蚀。散布在大气中的灰尘作为载体,凝结水蒸气形成水滴,吸附周围酸性含硫气体,接触钢结构表面后加速腐蚀。因此,要充分考虑运行环境对铁路客车耐腐蚀性的影响,制定针对性措施。如高温高湿地区,选用耐盐雾试验性能指标较高防腐底漆;高原、风沙地区,选用耐紫外线较强、抗风沙性较强的涂层体系。
图 3 常温下相对湿度对钢材腐蚀增量的影响
1.12 技术要求
2015年底,中国铁路总公司为统一防腐标准,制定了运辆客车函【2015 】 73 号文件。此文件规定了新造、检修客车防腐涂装工艺技术要求,涂料使用技术标准,属于总体性文件。但在铁路客车的车体设计中,涂装技术要求在具体的图纸或相应的技术文件中不明确或模糊,往往在设计过程中被忽略或边缘化。这是由于防腐涂装涉及到车体制造过程中的方方面面,小到一个垫片,大到一个整车,非专业技术人员对防腐的认知程度相对较低,并且在设计管理上缺乏防腐环节的必要管控,造成防腐要求含糊或不明确现象发生。如车钩、底架横梁、心盘、缓冲梁等附件仅规定了防腐处理,具体处理的范围,厚度要求不明确,造成在车体制造过程中执行模糊。这就需要设计、工艺技术人员总体考虑,结合制造工艺,明确防腐要求,使防腐涂装的概念融入到车体制造的整个过程中。
另外,要结合相应车型的车内布置,不同区域的使用环境,有针对性的制定相应的防腐措施,包括更换材质、改变涂装体系、排水等,有效结合在一起。如图4 ,洗漱间、卫生间、脚蹬翻板、车厢通道区域,长期接触潮湿空气或水,环境相对恶劣;车内窗口区域受车内外温差影响,冷凝水较多,尤其是冬季,造成车内窗口区域板材腐蚀较为严重。
1.13 材质方面
基材选 用 铁 路 客 车 车 体 钢 结 构 主 要 普 遍 采 用05CuPCrNi 、 09CuPCrNi型号的耐候钢,耐候钢长期的耐腐蚀性较差,如防腐做不好,会造成后续腐蚀线性加剧。设计之初,要充分考虑车内布置,各部位钢结构在运行过程中容易出现的现象。如车内卫生间、洗漱间部位,在正常运行过程中易出现积水,地板长期处于腐蚀介质中,因此属于严重腐蚀区域。车门框、翻板脚蹬区域由于铁路客车长期处于运行过程中,遇多雨季节,若密封不彻底,雨水进入地板内部,后造成此区域腐蚀严重。因此要充分考虑局部更换材质解决,如上述所说部位,更换不锈钢或不锈铁;对于车外,尤其是底架,以提高整体的防腐性。另外,在材质选择上,要避免出现电位差相差较大的材质接触,避免电化学腐蚀。如耐候钢、铝合金直接接触。
1.14 结构方面
结构问题是制约铁路客车耐腐蚀性差的主要原因,是造成后续表面处理、防腐涂装无法实现或无效的根本原因。主要存在以下几个方面:
(1 )型腔结构
其主要表现在车体骨架采用“帽形”结构,骨架内部防腐无法实现。在车体制造过程中,若组焊前对内腔进行防腐处理,涂防腐底漆40~60 μ m ,则焊接部位会因涂层太厚,无法实现焊接,同时焊后内部烧蚀区域涂层无法二次处理,同理,与帽形骨架相搭接的墙板,朝向车内的一侧,在车体制造过程中亦需要进行暂短防腐,涂预涂底漆10~20 μ m ,焊接前亦无法进行防腐处理,否则会影响焊接,同时焊后无法进行二次处理,因此,铁路客车侧端墙骨架内腔部位防腐存在严重问题,内侧墙面仅一层厚度为10~20 μ m 的预涂底漆。如侧柱根部,根据对检修客车的腐蚀情况调查,侧柱根部区域截换率较高,从侧柱根部区域的结构来看(如图5 ),侧墙板与底架边梁外侧焊接为满焊;侧柱紧贴侧墙板,并且与底架边梁对接,形成封闭空腔;同时波纹地板与底架边梁搭接,搭接内侧为段焊要求,进而在封闭型腔内侧可能存在缝隙或段焊;搭接外侧为缝隙,并且波纹地板深入到侧柱封闭空腔内部;因此,在封闭空间内,形成一或两条狭窄的缝隙,底架外侧形成缝隙,同时,内腔及各搭接部位防腐无法实现防腐,焊接后表面的预涂底漆涂层又严重破坏,形成的封闭区域不易补救,无法进行后续处理,随着车辆的运行,侧柱根部逐渐形成冷凝水,并且不易排出,形成腐蚀介质,加速腐蚀。如图6 。
( 2 )搭接结构
搭接结构是铁路客车钢结构焊接中常见的结构之一,一般采用段焊或塞焊方式,如侧墙板与骨架的搭接、侧墙板与底架的搭接、侧墙板与上边梁的搭接、波纹地板与底架边梁的搭接等,焊接前对搭接区域使用角磨机进行打磨处理,然后按要求进行焊接,焊后对外露区域进行打磨,去除烧蚀涂层、焊接飞溅等,但对于搭接内部区域无法进行处理,目前,普遍采用后续涂装的方法使用油漆封堵,此方法在一定程度上起到防腐作用,但缝隙稍大时,油漆虽在外层覆盖上一层,但搭接结构内部,仍无法渗入,水汽亦可进入内部。若采用段焊密封工艺进行防腐密封,对于整个钢结构车体,此结构较多,在实际制造过程中,无法实现,成本较高,如图7、图8。
( 3 )排水及边界结构
铁路客车车体结构设计过程中,为避免腐蚀,提高防腐性能,延长使用寿命,应融入排水的设计理念,避免积水、积沉等现象,从而较少介质对基材的腐蚀。主要有以下几个方面,见图9 。
① 避免钢结构中出现开口向上或倾斜的现象,对于特殊要求设置排水孔或断口,如波纹地板;② 避免钢结构中出现凹槽或凹口,对于特殊要求设置排水孔或断口;③ 避免钢结构中出现锐边,避免涂装边界效应,涂层不易附着或涂层厚度薄的现象发生。
1.2 工艺方面
1.21 车体制造工艺
预涂底漆是影响铁路客车防腐的主要因素之一。
目前,普遍采用骨架+蒙皮结构组焊形成车体钢结构,组焊前为保证板材、型材在一定时间内具有一定的防腐性,需进行表面预处理,一般采用抛丸、喷沙或化学预处理方式,处理后表面涂覆一层预涂底漆作为车间底漆,进行暂时性防腐。而预涂底漆会造成两方面的影响: ①焊接质量变差。焊接过程中,焊缝表面易出现气孔,不利于后续防腐,并且焊接飞溅、焊渣、烧蚀涂层大量出现。由于结构原因,飞溅、焊渣、烧蚀涂层不易清除。 ②防腐性能差。预涂底漆是作为暂时性防腐使用,防腐性较差,一般情况下,耐盐雾试验仅要求不小于 48h ( GB /T 1771 ),但在后续涂装过程中,一般情况下预涂底漆无法彻底清除,均采用保留预涂底漆,从而出现底层预涂底漆差,外道涂层防腐性相对较高的现象,一旦腐蚀介质进入内部,会造成整个涂装体系的防腐性能下降。
焊接过程中冷却工艺与电磁调平工艺是影响铁路客车防腐的主要因素之二。目前,大多数的车体制造过程中,为避免焊接变形较大,焊接过程中普遍采用水冷,水作为腐蚀介质,若长期接触钢结构,会发生腐蚀,或在死角或型腔结构内积水,会造成腐蚀在车体制造过程中已经发生。因此,要引进新工艺,避免类似问题出现,当前要做好积水的及时清理工作。此外,为保证整车的平整度,车体组焊完成后要进行整车电磁调平、火焰激烤,此过程出现大量烧蚀涂层,若烧蚀清理不彻底,会降低整个涂装体系的防腐性,因此要控制激烤点的打磨处理质量。
另外,车体制造过程中,打磨、焊接必不可少,但往往忽略防腐,打磨处理后的板材或型材若不及时进行防腐处理,板材表面会发生腐蚀,一般来说,4h内进行防腐。这对于车体制造车间来说,难度较大,涉及到涂装质量控制、安全、人员配置管理等方面,不易控制。
1.22 涂装工艺
( 1 )打磨、清洁打磨、清洁处理是整车涂装前的最后环节,车体制造完成后不可避免会出现飞溅、焊渣、铁屑、油污、灰尘、水、锈迹、烧蚀涂层等影响涂层附着力的杂质,若处理不彻底,直接影响涂层附着力,并且部分腐蚀依然在涂层内部延续。因此,要重点控制车体涂装前表面的清洁度,一般要求达到Sa2。5级。对于锈迹,使用角磨机进行打磨处理,对于附着不牢的烧蚀涂层,使用打磨机打磨处理,所有打磨处理完成后风管吹尘,稀释剂去除油污,干净的擦车布去除水迹。然而,受车体结构、制造工艺限制,局部边、角、孔、洞、缝的部位无法处理到位,影响后续涂层的附着力,进而降低耐腐蚀性。
(2 )涂装施工涂装工艺属于特殊过程,过程控制至关重要。涂装过程中,边、角、孔、洞、缝区域,型材内部、型腔内部区域无法喷涂到位,出现虚喷、漏喷等现象。尤其是防腐底漆,会造成钢结构外露或预涂底漆外露,耐腐蚀性弱,并加剧腐蚀。
铁路客车的涂装工艺按照各部位运行条件,主要分为:
车内:底漆+重防腐涂料+阻尼涂料(隔音降噪作用);车下:底漆 + 重防腐涂料 + 阻尼涂料 + 水性底架面漆(隔音降噪作用);侧端墙:底漆 + 腻子 + 中涂 + 面漆 + 清漆;车顶:底漆 + 面漆 + 清漆。
要重点控制每道工序的油漆调配、喷涂前处理、喷涂环境、喷涂厚度、烘干条件,确保每道涂层彻底干燥,附着力及涂层厚度符合技术要求,严格按运辆客车函【2015 】 73 号文件执行。
1.3 运营方面
铁路客车在运营过程中需要定期保养,及时清除外皮、底架外表面的污物,尤其是无集便器的车辆。这是因为无集便器铁路客车在运营过程中,粪便废物自然排放路轨上,其中有很大一部分溅射到转向架、蓄电池箱体等底架悬挂件上,在回库保养清洗的过程中,未及时清理,造成局部漆膜表面长期浸渍在弱酸或弱碱的环境中,长此以往造成漆膜起泡,漆膜内部发生腐蚀。
在车辆清洗的过程中,为提高清洗效率、效果,使用浓度较大的碱水或草酸进行清洗,或使用硬刷进行刷车,造成油漆过早失光,耐老化性下降,易出现粉化现象。对于车内,为保证客室卫生,清洁时使用大量清水冲刷客室,水通过地板布缝隙及木地板,渗入铁地板缝隙或角落上,日积月累,造成铁地板大量腐蚀。
因此,在运行方面要使用中性清洗剂进行车体表面清洁,并及时用水清洗,同时尽量避免飞溅到其他部位。对于车内,禁止大量使用清水冲洗。
2 发展方向
未来从耐腐蚀性及使用寿命方面来讲,铁路客车的发展方向主要从制造技术水平与管理水平方面两个方面着手:
2.1 制造技术水平
首先要将防腐的观念融入到铁路客车设计开发、制造、运营、维护等整个产品及部件的生产过程中,引进新技术,改变铁路客车车体结构,优化焊接形式,取消预涂底漆,参考动车组车体设计、制造工艺,涂装前采用整车喷砂工艺,确保表面清洁度及粗糙度,为后续获得良好的附着力奠定基础。一旦技术成熟,可取消化学预处理,减少废酸、废碱等废液的排放,降低废液处理费用,减少对环境的污染;可改善车体钢结构的制造环境,避免打磨、焊接、涂漆在同一区域作业,降低安全系数;有利于表面处理、涂装特殊工艺过程的管控,提高防腐质量,延长铁路客车使用寿命,并且可打造精品碳钢铁路客车的技术水平。目前,已开发研究的车体结构有“乙型梁”骨架+蒙皮结构,但距离批量化生产还有一定难度。
2.2 管理水平
由于铁路客车防腐涉及到的范围广,从管理层次上包括了设计、工艺、制造、运营、检修等部门,从产品层次上,小到一个垫片、大到一个整车,任何一个环节出现漏洞,均会造成腐蚀现象发生。同时防腐涂装又具有隐蔽性强,短期不易发现,不易检测的特点,这就造成目前铁路客车制造、运营及检修基地对于车辆的防腐重视程度不够,缺乏防腐预防、整治、维护保养的观念,因此,应加强设计、工艺、操作、运营、检修等相关人员的防腐知识培训,使铁路客车的防腐观念渗透到每一个角落,在铁路客车运营的整个生命周期中形成一个庞大的管控体系,整体提高铁路客车的制造水平。
更多关于材料方面、材料腐蚀控制、材料科普等方面的国内外最新动态,我们网站会不断更新。希望大家一直关注中国腐蚀与防护网http://www.ecorr.org
责任编辑:殷鹏飞
投稿联系:编辑部
电话:010-62313558-806
中国腐蚀与防护网官方 QQ群:140808414
免责声明:本网站所转载的文字、图片与视频资料版权归原创作者所有,如果涉及侵权,请第一时间联系本网删除。
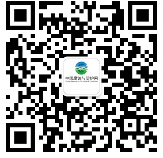
官方微信
《中国腐蚀与防护网电子期刊》征订启事
- 投稿联系:编辑部
- 电话:010-62316606-806
- 邮箱:fsfhzy666@163.com
- 中国腐蚀与防护网官方QQ群:140808414