可以这样形容,对于仍处于“成长期”的我国高性能纤维及其复合材料行业来说,在“十三五”期间要想获得突破性发展,缩短“与发达国家之间仍存在的15年左右的差距(中国化学纤维工业协会会长端小平语)”,就必须打胜“陆地战役”和“空中战役”这两场“硬仗”。所谓“陆地战役”,是指在高铁、汽车等交通领域的轻量化技术和应用必须突破;所谓“空中战役”,是指在大飞机等领域的轻量化技术和应用必须突破。
众所周知,高性能纤维是航空、航天、国防建设、经济建设、科技进步等领域不可或缺的重要战略物资,也是低碳经济和先进制造业中轻量化的核心技术之一。中国工程院院士蒋士成指出:“建立中国自己的高性能纤维与复合材料产业,对国家安全和社会发展具有重要意义。目前,我国碳纤维、芳纶等高性能纤维已经走过了‘从无到有’的发展阶段,但是,产品的应用开发研究滞后于产能的发展,这已经成为制约高性能纤维与复合材料产业发展的瓶颈。”
因此,在查找我国高性能纤维及其复合材料在下游领域应用方面与发达国家存在差距的基础上,如何结合我国新能源汽车、高铁等行业快速发展的实际状况,寻找到下一步发展的突破口和着力点至关重要。
“汽车战”:
配合新能源汽车技术开发成突破口
高性能纤维具有众多的应用领域和市场,汽车轻量化是其潜在的最大应用领域,也是碳纤维市场的主要推动力。汽车轻量化碳纤维复合材料应用技术将可能成为汽车产业的关键技术,成为汽车产业的核心竞争力之一。
相关实验证明,如果汽车整车重量降低10%,燃油效率可提高6%~8%;若汽车整备质量每减少100千克,百公里油耗可降低0.3升~0.6升,汽车重量降低1%,油耗可降低0.7%。
由于环保和节能的需要,汽车轻量化已经成为世界汽车工业发展的潮流。而且,在轻量化的同时,复合材料的运用也可提升汽车外观和内饰设计的时尚度。
对此,中国工程院院士蒋士成指出,我国是汽车生产大国,如果能加大研发投入,突破掌握碳纤维在汽车轻量化方面的关键应用技术,对我国汽车产业提高核心竞争力和建立具有中国特色的高性能纤维与复合材料产业具有重要意义。
而谈汽车的轻量化,必须谈一个标志性事件。德国宝马公司于2014年实现了全碳纤维汽车的批量生产,而且价格与金属材料的汽车相当。BMWi3采用全碳纤维车身,车身由30多个零部件胶结而成,便于维修--整个模块由标准件替换。
东华大学纤维材料改性国家重点实验室副主任余木火指出:“轻量化是低碳经济和先进制造业的核心技术之一,是国家竞争力的核心技术之一。BMWi3碳纤维电动车的成功商业化表明,技术进步和用量的扩大,碳纤维复合材料的成本可以大幅度下降,复合材料可以部分代替钢,将极大提高制造业的水平和竞争力,甚至有可能颠覆汽车生产核心技术。”
数据显示,当前全球汽车产量6400万辆,碳纤维龙头企业日本东丽公司预测,将用碳纤维65万吨。而到2020年,碳纤维在汽车上的需求将由2013年的2600吨猛增到23000吨,将与航空航天应用持平。这充分表明了碳纤维产业在汽车轻量化方面将大有可为。
目前,我国也有一些企业开始探索碳纤维及其复合材料在汽车方面的应用。澳新汽车史j践总经理介绍,该公司研发了多款碳纤维电动车车身,正在建立2万辆生产线。长城华冠汽车公司研发成功了K50碳纤维超级跑车。威海光威复合材料股份有限公司董事长李书乡介绍,近几年公司与哈尔滨工业大学(威海)进行校企合作,摸索碳纤维无模块成型技术(板条法)在大学生方程式赛车方面的应用。但整体看,在这方面仍刚刚起步。
广州汽车集团乘用车有限公司专家委员会主任陈建伟指出,高性能纤维及其复合材料在汽车上的应用推广,可以分为3个阶段:第一阶段是解决“用不用”的问题,第二阶段是解决“如何用”的问题,第三阶段是解决“值得用”的问题。国际上目前仍处于第二阶段的中后期,部分先行企业刚步入第三阶段,而我国目前正处于第一阶段末期和第二阶段初期。
陈建伟认为,我国要实现高性能纤维及其复合材料在汽车上的应用并形成社会效益,还存在“基础技术应用”和“经济型”两大瓶颈。他建议,分两步进行技术攻关:
第一步,是以配合新能源汽车技术开发为突破口,以汽车主要总成(承载式车身、非承载式车身、底盘副车架等)为纽带,建设全产业链(包括典型件的设计、制造、试验、回收的技术和手段)的国家示范工程,形成开放的、可以进行复制推广的应用技术基础。
第二步,发挥示范工程的示范作用,向全产业链普及推广高性能纤维及其复合材料汽车新技术应用,吸引、鼓励社会资本、企业、机构参与新技术应用、二次开发和再创新,从而开发出更多和更经济的典型应用,应用成本预期可出现大幅下降,从而进一步推动新技术的应用普及,达到运用市场的力量,形成良性循环。
陈建伟还指出,以目前国内该产业链的资金能力,难以支撑第一步技术开发的资金需求,因此,“建议国家从全产业链的战略角度考虑,对国家示范工程项目给予资金扶持,用5年左右的时间,形成开放的全行业共享的共性技术。而且,在第二步的开始阶段,国家应提供适度的扶持资金,激发行业对这一新应用技术进行推广普及,起到‘催化剂’作用。
而为推进该项工作,中国工程院已专门成立了2015年度咨询研究项目“高性能纤维与汽车轻量化技术创新发展战略研究”项目,项目于今年3月20日在东华大学召开了启动会。据项目秘书长余木火介绍,该项目将通过考察调研、研讨会等形式对国内外高性能纤维与复合材料的现状和发展趋势进行研究,形成给政府的咨询建议报告。本次论坛也成为该项目的一个主要交流平台。
轨道交通:
抓住动车、高铁大发展机遇
高铁和城市轨道交通、海上交通运输装备也迫切需要高性能纤维与复合材料。而碳纤维复合材料、对位芳纶复合材料是高铁轻量化的关键材料,广泛用在车厢及其内饰、车门等部件。
据烟台泰和新材料股份有限公司副总经理马千里介绍,意大利ETR500高速机车头部前突部分采用芳纶复合材料,我国长春客车CRH5也全部采用环保、轻量化的芳纶纸蜂窝芯材作内装材料。
据测算,以CRH5型高速列车推算,采用芳纶蜂窝的一节车要比采用铝蜂窝的节约1775公斤,八节编组共计减重14200公斤。按照时速200公里、每牵引一吨重量大约需要消耗12千瓦电力计算,一组列车将降耗170千瓦。按照时速300公里、每牵引一吨重量大约需要消耗16千瓦~17千瓦电力计算,一组列车将降耗227千瓦~241千瓦。而且,这种减重也减少了对轮轨的摩擦和压力,减少了维护工作。
此外,芳纶复合材料也是制造防弹车的关键材料,如奔驰S600防弹车、宝马X5防弹车便应用了高强度的芳纶复合材料衬层保护车辆底部安全性,汽车地板也用芳纶装甲。
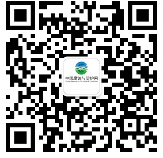
官方微信
《中国腐蚀与防护网电子期刊》征订启事
- 投稿联系:编辑部
- 电话:010-62313558-806
- 邮箱:fsfhzy666@163.com
- 中国腐蚀与防护网官方QQ群:140808414